Статьи по неразрушающему контролю
Химический (спектральный) анализ необходим для приемки металлолома, оценки автомобильных катализаторов, изучения горной породы, почвы и других объектов. Исследование позволяет определить присутствие примесей и прогнозировать эксплуатационные характеристики готового изделия. Наша лаборатория делает химический анализ состава черных и цветных металлов в диапазоне от углерода до урана (C⁶-U⁹²), в том числе алюминиевых сплавов, нержавейки, титана золота и других драгоценных металлов, а также черных сталей, отличающихся только по углероду. Анализ проводится рентгенофлуоресцентным (РФА) и лазерно-искровым (ЛИЭС) спектрометром. Результаты анализа показывают долю каждого элемента и наиболее близкие по элементному составу марки. Проведение анализа возможно в нашей лаборатории или на территории заказчика. Цена выездного химического анализа в Москве начинается от 30 000 руб. Сдать металл на химанализ в нашу лабораторию можно по адресу г. Лобня, ул. Борисова д. 14 к2. Заявки на направляйте по адресу kontrol@ntcexpert.ru.
Смотрите также разделы: Измерение ферритной фазы, Металлография, Измерение твердости, Спектральный анализ металлов и сплавов.
Проведение неразрушающего контроля возможно на территории Московской области и в других регионах РФ в том числе городах: Москва, Дмитров, Долгопрудный, Химки, Зеленоград, Красногорск, Балашиха, Королев, Жуковский, Люберцы, Лобня, Подольск, Электросталь, Коломна, Одинцово, Домодедово, Щелково, Серпухов, Ногинск, Пушкино, Сергиев Посад, Воскресенск, Ивантеевка, Дубна, Егорьевск, Чехов, Клин, Подольск, Реутов, Видное, Ступино, Наро-Фоминск, Фрязино, Лыткарино, Дзержинский, Солнечногорск, Кашира, Котельники, Нахабино, Красноармейск, Протвино, Истра, Шатура, Луховицы, Можайск, Дедовск, Ликино-Дулево, Апрелевка, Красноармейск, Озеры, Санкт-Петербург, Екатеринбург, Владимир, Иваново, Калуга, Кострома, Курск, Липецк, Муром, Новосибирск, Обнинск, Омск, Орёл, Псков, Ржев, Ростов, Рязань, Смоленск, Сочи, Тамбов, Тверь, Тобольск, Томск, Тула, Уфа, Челябинск, Ярославль и другие города.
Определение химического состава необходимо для проверки марок сталей и сплавов, в том числе алюминиевых, медных, титановых, а также, черных сталей, отличающихся только по углероду. Исследование позволяет определить присутствие примесей и прогнозировать эксплуатационные характеристики готового изделия. Наша аккредитованная лаборатория определяет химический состав черных и цветных металлов в диапазоне от углерода до урана (C⁶-U⁹²). Результаты анализа показывают долю каждого элемента и наиболее близкие по элементному составу марки. Анализ проводится рентгенофлуоресцентным (РФА) и лазерно-искровым (ЛИЭС) спектрометром. Результаты анализа показывают долю каждого элемента и наиболее близкие по элементному составу марки. Проведение анализа возможно в нашей лаборатории или на территории заказчика. Цена выездного химического анализа в Москве начинается от 30 000 руб. Сдать металл на химанализ в нашу лабораторию можно по адресу г. Лобня, ул. Борисова д. 14 к2. Заявки на направляйте по адресу kontrol@ntcexpert.ru.
Смотрите также разделы: Измерение ферритной фазы, Металлография, Измерение твердости, Спектральный анализ металлов и сплавов.
Проведение неразрушающего контроля возможно на территории Московской области и в других регионах РФ в том числе городах: Москва, Дмитров, Долгопрудный, Химки, Зеленоград, Красногорск, Балашиха, Королев, Жуковский, Люберцы, Лобня, Подольск, Электросталь, Коломна, Одинцово, Домодедово, Щелково, Серпухов, Ногинск, Пушкино, Сергиев Посад, Воскресенск, Ивантеевка, Дубна, Егорьевск, Чехов, Клин, Подольск, Реутов, Видное, Ступино, Наро-Фоминск, Фрязино, Лыткарино, Дзержинский, Солнечногорск, Кашира, Котельники, Нахабино, Красноармейск, Протвино, Истра, Шатура, Луховицы, Можайск, Дедовск, Ликино-Дулево, Апрелевка, Красноармейск, Озеры, Санкт-Петербург, Екатеринбург, Владимир, Иваново, Калуга, Кострома, Курск, Липецк, Муром, Новосибирск, Обнинск, Омск, Орёл, Псков, Ржев, Ростов, Рязань, Смоленск, Сочи, Тамбов, Тверь, Тобольск, Томск, Тула, Уфа, Челябинск, Ярославль и другие города.
Спектральный (химический) анализ драгоценных металлов применяется на всех этапах от добычи до повторной переработки. Анализ может определить содержание золота в горной породе, подтвердить пробу ювелирных изделий или чистоту технического золота, извлекаемого вторичной переработкой. Наша лаборатория делает спектральный анализ состава золота, серебра, платины, родия и палладия. Для анализа применяется современный РФА спектрометр, за несколько секунд определяющий процентное содержание драгметаллов и других элементов. Пакет специальных настроек позволяет видеть распределение золота на анализируемом участке породы и определять наличие сопутствующих золоту элементов-маркеров. Проведение анализа возможно в нашей лаборатории либо с выездом на объект заказчика. В Москве цена выездного спектрального анализа драгоценных металлов начинается от 30 000 руб. Сдать металл на химанализ в нашу лабораторию можно по адресу г. Лобня, ул. Борисова д. 14 к2. Заявки на направляйте по адресу kontrol@ntcexpert.ru.
Сфера применения | Объекты анализа |
Геологоразведка и добыча | Содержание золота в породе, самородках, сплаве Доре (лигатурное золото) |
Банковская деятельность | Чистота золотых слитков, реже серебра, платины и палладия. |
Ювелиры и нумизматы | Проверка пробы ювелирных изделий и подлинности монет |
Вторичная переработка | Содержание Au, Ag, Rh, Pd, Pt в автокатализаторах и переработанном радиоломе. |
Прочие сферы | Антиквариат, сусальное золото |
Дополнительные материалы:
- ГОСТ 17234-71. Золотые сплавы. Метод определения содержание золота и серебра.
- ГОСТ 27973.1-88. Золото. Методы атомно-эмиссионного спектрального анализа.
- ГОСТ 12563.2-83. Золото-палладиевые сплавы. Метод спектрального анализа.
- ГОСТ 16321.2-70. Серебряно-медные сплавы. Метод спектрального анализа.
- ГОСТ 12551.2-82. Платино-медные сплавы. Методы спектрального анализа.
- ГОСТ 12553.2-77. Платино-палладиевые сплавы. Метод спектрального анализа.
- ГОСТ 12556.2-82. Платино-родиевые сплавы. Методы спектрального анализа.
- ГОСТ 12227.0-76. Родий. Метод спектрального анализа.
- ГОСТ 12559.2-82. Платино-иридиевые сплавы. Методы спектрального анализа.
- ГОСТ 12223.0-76. Иридий. Метод спектрального анализа.
Смотрите также разделы: Измерение ферритной фазы, Металлография, Измерение твердости, Спектральный анализ металлов и сплавов.
Проведение неразрушающего контроля возможно на территории Московской области и в других регионах РФ в том числе городах: Москва, Дмитров, Долгопрудный, Химки, Зеленоград, Красногорск, Балашиха, Королев, Жуковский, Люберцы, Лобня, Подольск, Электросталь, Коломна, Одинцово, Домодедово, Щелково, Серпухов, Ногинск, Пушкино, Сергиев Посад, Воскресенск, Ивантеевка, Дубна, Егорьевск, Чехов, Клин, Подольск, Реутов, Видное, Ступино, Наро-Фоминск, Фрязино, Лыткарино, Дзержинский, Солнечногорск, Кашира, Котельники, Нахабино, Красноармейск, Протвино, Истра, Шатура, Луховицы, Можайск, Дедовск, Ликино-Дулево, Апрелевка, Красноармейск, Озеры, Санкт-Петербург, Екатеринбург, Владимир, Иваново, Калуга, Кострома, Курск, Липецк, Муром, Новосибирск, Обнинск, Омск, Орёл, Псков, Ржев, Ростов, Рязань, Смоленск, Сочи, Тамбов, Тверь, Тобольск, Томск, Тула, Уфа, Челябинск, Ярославль и другие города.
Спектральный (химический) анализ породы необходим в геологии и геохимии для разведки и добычи полезных ископаемых, оценки загрязнённости почвы тяжелыми металлами и другими опасными элементами. Применяемые нашей лабораторией рентгенофлуоресцентные и лазерно-искровые спектрометры оснащены специальным приложением «GeoChem Pro», содержащим калибровки для элементного анализа горных пород, руды, почвы и минералов. Данное приложение позволяет работать в расширенном диапазоне (Li3-U92) и определять содержание элементов с большей точностью. Предусмотрены функции перевода элементов в их оксиды, выбор единиц измерения (ppm или %), а также функция карты распределения элементов. Проведение спектрального анализа возможно в полевых условиях либо в нашей лаборатории. Цена анализа с выездом в Москве начинается от 30 000 руб. Сдать металл на химанализ в нашу лабораторию можно по адресу г. Лобня, ул. Борисова д. 14 к2. Заявки на направляйте по адресу kontrol@ntcexpert.ru.
Смотрите также разделы: Измерение ферритной фазы, Металлография, Измерение твердости, Спектральный анализ металлов и сплавов.
Проведение неразрушающего контроля возможно на территории Московской области и в других регионах РФ в том числе городах: Москва, Дмитров, Долгопрудный, Химки, Зеленоград, Красногорск, Балашиха, Королев, Жуковский, Люберцы, Лобня, Подольск, Электросталь, Коломна, Одинцово, Домодедово, Щелково, Серпухов, Ногинск, Пушкино, Сергиев Посад, Воскресенск, Ивантеевка, Дубна, Егорьевск, Чехов, Клин, Подольск, Реутов, Видное, Ступино, Наро-Фоминск, Фрязино, Лыткарино, Дзержинский, Солнечногорск, Кашира, Котельники, Нахабино, Красноармейск, Протвино, Истра, Шатура, Луховицы, Можайск, Дедовск, Ликино-Дулево, Апрелевка, Красноармейск, Озеры, Санкт-Петербург, Екатеринбург, Владимир, Иваново, Калуга, Кострома, Курск, Липецк, Муром, Новосибирск, Обнинск, Омск, Орёл, Псков, Ржев, Ростов, Рязань, Смоленск, Сочи, Тамбов, Тверь, Тобольск, Томск, Тула, Уфа, Челябинск, Ярославль и другие города.
Химический (спектральный) анализ стали – это качественное или количественное определение химических элементов, содержащихся в исследуемом образце. Исследование позволяет определить присутствие примесей и прогнозировать эксплуатационные характеристики готового изделия. По химическому составу стали делятся на углеродистые и легированные. Каждый тип в свою очередь включает подгруппы с низким, средним и высоким содержанием углерода и легирующих элементов. Помимо химического состава, стали группируют по назначению, качеству, структуре и другим характеристикам.
Наша аккредитованная лаборатория оказывает услуги по химическому анализу металлов и сплавов в диапазоне от углерода до урана (C6-U92), в том числе алюминиевых сплавов, нержавейки, титана золота и других драгоценных металлов, а также черных сталей, отличающихся только по углероду. Анализ проводится рентгенофлуоресцентным (РФА) и лазерно-искровым (ЛИЭС) спектрометром. Результаты анализа показывают долю каждого элемента и наиболее близкие по элементному составу марки стали. Проведение анализа возможно в нашей лаборатории или на территории заказчика. Цена выездного химического анализа в Москве начинается от 30 000 руб. Сдать металл на химанализ в нашу лабораторию можно по адресу г. Лобня, ул. Борисова д. 14 к2. Заявки на направляйте по адресу kontrol@ntcexpert.ru.
Дополнительные материалы:
- Статьи по спектральному анализу
- ГОСТ 22536.0-87 Сталь углеродистая и чугун нелегированный. Методы анализа
- ГОСТ Р 54153-2010. Сталь. Метод атомно-эмиссионного спектрального анализа.
- ГОСТ 12344-2003 Стали легированные и высоколегированные. Методы определения углерода
- ГОСТ 27809-95. Чугун и сталь. Метод спектрографического анализа.
- ГОСТ 27611-88. Чугун. Методы фотоэлектрического спектрального анализа.
- ГОСТ 9717.1-82. Медь. Методы спектрального анализа.
- ГОСТ 9716.2-79. Сплавы медно-цинковые. Метод спектрального анализа по металлическим стандартным образцам
- ГОСТ 6012-98. Никель. Методы химико-атомно-эмиссионного спектрального анализа.
- ГОСТ 15483.10-2004. Олово. Методы атомно-эмиссионного спектрального анализа.
- ГОСТ 8857-77. Свинец. Метод спектрального анализа.
- ГОСТ 17261-77. Цинк. Спектральный метод анализа.
- ГОСТ 23328-95. Сплавы цинковые. Методы спектрального анализа.
- ГОСТ 23902-79. Сплавы титановые. Методы спектрального анализа.
- ГОСТ 3221-85. Алюминий первичный. Методы спектрального анализа.
Смотрите также разделы: Измерение ферритной фазы, Металлография, Измерение твердости, Спектральный анализ металлов и сплавов.
Проведение неразрушающего контроля возможно на территории Московской области и в других регионах РФ в том числе городах: Москва, Дмитров, Долгопрудный, Химки, Зеленоград, Красногорск, Балашиха, Королев, Жуковский, Люберцы, Лобня, Подольск, Электросталь, Коломна, Одинцово, Домодедово, Щелково, Серпухов, Ногинск, Пушкино, Сергиев Посад, Воскресенск, Ивантеевка, Дубна, Егорьевск, Чехов, Клин, Подольск, Реутов, Видное, Ступино, Наро-Фоминск, Фрязино, Лыткарино, Дзержинский, Солнечногорск, Кашира, Котельники, Нахабино, Красноармейск, Протвино, Истра, Шатура, Луховицы, Можайск, Дедовск, Ликино-Дулево, Апрелевка, Красноармейск, Озеры, Санкт-Петербург, Екатеринбург, Владимир, Иваново, Калуга, Кострома, Курск, Липецк, Муром, Новосибирск, Обнинск, Омск, Орёл, Псков, Ржев, Ростов, Рязань, Смоленск, Сочи, Тамбов, Тверь, Тобольск, Томск, Тула, Уфа, Челябинск, Ярославль и другие города.
Спектральный (химический) анализ алюминия применяется на всех этапах от добычи до повторной переработки. Анализ может определить содержание Al в горной породе, подтвердить заявленную поставщиком марку или чистоту технического алюминия, извлекаемого вторичной переработкой. Спектральный анализ алюминия можно условно разделись на базовый и тонкий. Базовая сортировка не определяет легкие элементы (Al, Mg, Si), показывая только их суммарную долю. Такой функционал имеют бюджетные и устаревшие модели с полупроводниковым PIN детектором, рассчитанные на работу с титаном и более тяжелыми элементами. Базовый анализ неприменим для точного определения марки алюминия и сплавов на его основе отличающихся только содержанием дополнительных элементов, таких как магний, кремний или марганец.
Наша аккредитованная лаборатория оснащена современным рентгенофлуоресцентным (РФА) и лазерно-искровым (ЛИЭС) спектрометром, дающие возможность тонкой сортировки с определением марки алюминия и его сплавов в том числе Al-Si, Al-Mg, Al-Fe, Al-Li. Пределы обнаружения по магнию и кремнию составляют 0.25% и 0.1% соответственно. Это позволяет быстро идентифицировать марки, отличающиеся только низкими концентрациями данных элементов, например АК8, Д16, АмЦ и Д12. Проведение спектрального анализа возможно лабораторно или с выездом на объект заказчика. Цена выездного анализа в Москве начинается от 30 000 руб. Сдать алюминий на спектральный анализ в нашу лабораторию можно по адресу г. Лобня, ул. Борисова д. 14 к2. Заявки на спектрометрию направляйте по адресу kontrol@ntcexpert.ru.
Дополнительные материалы:
- ГОСТ 7727-81 Сплавы алюминиевые. Методы спектрального анализа
- ГОСТ 3221-85. Алюминий первичный. Методы спектрального анализа.
Сортировка алюминия
Подпишитесь на наш канал YouTube
Смотрите также разделы: Измерение ферритной фазы, Металлография, Измерение твердости, Спектральный анализ металлов и сплавов.
Проведение неразрушающего контроля возможно на территории московской области и в других регионах РФ в том числе городах: Москва, Дмитров, Долгопрудный, Химки, Зеленоград, Красногорск, Балашиха, Королев, Жуковский, Люберцы, Лобня, Подольск, Электросталь, Коломна, Одинцово, Домодедово, Щелково, Серпухов, Ногинск, Пушкино, Сергиев Посад, Воскресенск, Ивантеевка, Дубна, Егорьевск, Чехов, Клин, Подольск, Реутов, Видное, Ступино, Наро-Фоминск, Фрязино, Лыткарино, Дзержинский, Солнечногорск, Кашира, Котельники, Нахабино, Красноармейск, Протвино, Истра, Шатура, Луховицы, Можайск, Дедовск, Ликино-Дулево, Апрелевка, Красноармейск, Озеры, Санкт-Петербург, Екатеринбург, Владимир, Иваново, Калуга, Кострома, Курск, Липецк, Муром, Новосибирск, Обнинск, Омск, Орёл, Псков, Ржев, Ростов, Рязань, Смоленск, Сочи, Тамбов, Тверь, Тобольск, Томск, Тула, Уфа, Челябинск, Ярославль и другие города.
Для защиты трубопроводов от коррозии применяются изоляционные покрытия разных типов. В процессе эксплуатации могут возникать дефекты изоляции, нарушающие их сплошность и защитные свойства. В связи с этим, контроль изоляции трубопроводов является важным условием безаварийной эксплуатации в течение всего срока их службы.
Наиболее часто применимым методом неразрушающего контроля изоляции трубопроводов является электроискровой метод. Искровые дефектоскопы фиксируют электрические пробои информируя пользователя о наличии дефекта звуковой и световой сигнализацией. Такие приборы работают с напряжением от 0,5 до 35 кВ, позволяя контролировать покрытия толщиной от 40 мкм до 40 мм, и выявлять дефекты размером от 50 мкм. К преимуществам этого метода можно отнести высокие скорость контроля и достоверность результатов. В России данный метод регламентирован ГОСТ 34395-2018.
Другим методом электрического контроля, получившим широкое распространение в зарубежной практике является метод влажной губки (Holiday Testing) описанный в ASTM D 5162: 2015. В отличии от искрового, данный метод использует низковольтное напряжение до 100 В, при котором возможность повреждения покрытия искровым пробоем полностью исключена. Недостатками метода являются низкая производительности (губку надо постоянно смачивать и протирать поверхность покрытия после обнаружения дефекта) и низкая чувствительность к дефектам типа утонения и включения.
Наша аттестованная лаборатория оказывает услуги по неразрушающему контролю изоляции трубопроводов. Работы проводятся дефектоскопистами, аттестованными на II и III уровни согласно СДАНК-02-2020 и имеющими всё необходимое оборудование (дефектоскоп, толщиномер, трещиномер). По результатам контроля выдается заключение о качестве контролируемого покрытия (примеры). Стоимость электрического контроля сплошности покрытий начинается от 100 рублей за погонный метр. Для составления КП необходимо дать описание объекта и контролируемого покрытия, сообщить место проведения и количество объектов контроля. Работы возможны в Москве и на всей территории РФ. Заявки направляйте по адресу kontrol@ntcexpert.ru
Статьи и нормативы по контролю изоляции трубопроводов:
- ГОСТ 34395-2018 - Материалы лакокрасочные. Электроискровой метод контроля сплошности диэлектрических покрытий на токопроводящих основаниях
- ГОСТ Р51164–98 - Трубопроводы стальные магистральные. Общие требования к защите от коррозии.
- Технологическая инструкция компании Роснефть «Антикоррозионная защита металлических конструкций на объектах нефтегазодобычи, нефтегазопереработки и нефтепродуктообеспечения компании»
- ASTM D 5162: 2015 - Стандартный порядок испытания нарушений сплошности (тест Холидей) непроводящих защитных покрытий на металлических подложках
- ВСН 210-87 - Инструкция по применению комплекса устройств для неразрушающего контроля сплошности изоляционных покрытий заглубленных трубопроводов
- Контроль и диагностика поверхностных слоев и покрытий. Тенденции и перспективы
- Приборы контроля сплошности покрытий
Контроль покрытий электроискровым дефектоскопом Elcometer
Подпишитесь на наш канал YouTube
Заявки на услуги по контролю изоляции трубопроводов направляйте по адресу kontrol@ntcexpert.ru. Смотрите так же разделы – Услуги по измерению твердости, Услуги по УЗК, Услуги по измерению шероховатости.
О качестве бетона судят в первую очередь по его прочности. Прочность бетона — это величина, выражающая его способность сопротивляться разрушению под внешним воздействием. Способы определения прочности бетона можно условно поделить на разрушающие и неразрушающие. К первому относятся испытания контрольных образцов на сжатие под прессом. Второй способ более вариативен и предусматривает семь различных методик, применяемых в зависимости от задач и условий контроля. Неразрушающие методы определения прочности особенно актуальны при невозможности выборки образцов, при больших объемах контроля, в процессе строительства, эксплуатации и реконструкции.
Общие правила контроля прочности бетона изложены в ГОСТ 18105-2010. Определение прочности бетона механическими методами неразрушающего контроля посвящен ГОСТ 22690-2015. Описание ультразвукового метода измерения прочности содержится в ГОСТ 17624-2012. Оборудование для контроля прочности бетона должно быть поверено. Персонал должен быть аттестован в одной из систем оценки соответствия. Нормативные предписания по различным методам приведены в таблице. Другие нормативы и статьи по данной теме можно найти в конце страницы.
Наша аттестованная лаборатория оказывает услуги определения прочности бетона неразрушающими методами. Работы проводятся специалистами, аттестованными по СДАНК-02-2020 и имеющими всё необходимое оборудование. По результатам контроля выдается подробное заключение (примеры). Стоимость работ по измерению прочности начинается от 500 руб. за 1 образец. Для составления КП необходимо сообщить метод необходимых испытаний, чертеж или фото, место проведения и количество контролируемых объектов. Контроль возможен в Московском регионе и за его пределами. Помимо услуг по контролю наша компания занимается поставкой оборудования для контроля бетона методами НК. Заявки направляйте по адресу kontrol@ntcexpert.ru.
Неразрушающие методы определения прочности бетона
Косвенные методы неразрушающего контроля прочности бетона | Прямые методы неразрушающего контроля бетона (методы местных разрушений) | ||||||
Ударный импульс | Упругий отскок | Пластическая деформация | Ультразвуковое обследование | Скалывание ребра | Отрыв со скалыванием | Отрыв металлических дисков | |
Диапазон прочности МПа | 5-150 | 5-50 | 5-50 | 10-40 | 10-70 | 5-100 | 5-60 |
Погрешность измерений | ± 50% | ± 50% | ± 30-40% | ± 30-50% | Нет данных | Нет данных | Нет данных |
Количество измерений | 10 | 9 | 5 | 3 или 4 | - | 150 | 50 |
Мин. расстояние от края изделия, мм | 50 | 50 | 50 | - | 2 | 1-2 | 1 |
Мин. расстояние между местами измерений мм | 15 | 30 | 30 | - | 200 | 5h | 2 диаметра диска |
Минимальная толщина образца, мм | 50 | 100 | 70 | - | 170 | 2h | 50 |
Типовое оборудование | ИПС-МГ4 | Молоток Шмидта | Молоток Кашкарова | Тестер UK1401 | ПОС-60МГ4 | ПСО-ХМГ4 | Оникс-1 |
Преимущества | Простота. Возможность определять класс бетона. | Простота и скорость исследования. | Простота и дешевизна. | Возможность определения прочности глубинных слоев. | Простота. Подготовка образцов не требуется. |
Высокая точность. Наличие градуировочных зависимостей по ГОСТ | Подходит для густоармированных конструкций. Менее трудоёмкий, чем отрыв со скалыванием. |
Недостатки | Низкая точность. Контролируется только верхний слой 25-30 мм. | Нужна подготовка поверхности. Контролируется только верхний слой 25-30 мм. | Низкая точность. | Нужна подготовка поверхности и высокая квалификация контроллера. | Не применим для поврежденного бетона и при толщине меньше 2 см | Трудоёмкость. Неприменимость для густоармированных и тонкостенных объектов. |
Нужна подготовка: на бетон нужно наклеить диски за 3-24 часа до проверки. |
Дополнительная информация:
- ГОСТ 18105-2010 Бетоны. Правила контроля и оценки прочности
- ГОСТ 22690-2015 Бетоны. Определение прочности механическими методами неразрушающего контроля
- ГОСТ 17624-2012 Бетоны. Ультразвуковой метод определения прочности
- ГОСТ 24332-88 Кирпич и камни силикатные. Ультразвуковой метод определения прочности при сжатии
- ГОСТ 10180-2012 Бетоны. Методы определения прочности по контрольным образцам
- Определение прочности бетона с использованием молотка Шмидта (по DIN EN 12504-2: 2001-12)
- Определение прочности бетона на отрыв адгезии нанесённых на бетон покрытий
- Оценка прочности бетона в конструкциях при их возведении и эксплуатации
Смотрите также разделы: Дефектоскопы для бетона, Услуги по контролю бетона, Приборы для поиска арматуры, Обучение и аттестация специалистов.
Автоматизация процессов неразрушающего контроля является одним из векторов развития мирового рынка НК. Основное преимущество автоматизации - это повышение качества контроля при снижении стоимости и сроков. Высокоточный автоматизированный контроль все чаще становится обязательным требованием для работы с крупными российскими и зарубежными заказчиками в нефтегазовой, металлургической, атомной и военной отраслях. Наибольший эффект от использования автоматизации достигается на предприятиях проводящих поточный контроль однотипных изделий, обычно это металлические и пластиковые трубы, листовой прокат, литые заготовки и рельсы. В ряде случае автоматизация необходима для контроля труднодоступных или опасных для человека объектов, например на атомных станциях.
Наша лаборатория НК предлагает услуги по разработке и производству автоматизированных систем ультразвукового, вихретокового, капиллярного и оптического контроля, в том числе с применением современных методов ФР, TODF, ЭМАП. Мы разрабатываем и внедряем как уже широко известные комплексы, так и узкопрофильные системы для контроля нестандартных объектов. Опишите вашу задачу, а наши специалисты помогут подобрать подходящее оборудование по оптимальной цене.
Смотрите также разделы: Услуги по ультразвуковому контролю, Услуги по капиллярному контролю, Услуги по магнитному контролю.
Проведение неразрушающего контроля возможно на территории московской области и в других регионах РФ в том числе городах: Москва, Дмитров, Долгопрудный, Химки, Зеленоград, Красногорск, Балашиха, Королев, Жуковский, Люберцы, Лобня, Подольск, Электросталь, Коломна, Одинцово, Домодедово, Щелково, Серпухов, Ногинск, Пушкино, Сергиев Посад, Воскресенск, Ивантеевка, Дубна, Егорьевск, Чехов, Клин, Подольск, Реутов, Видное, Ступино, Наро-Фоминск, Фрязино, Лыткарино, Дзержинский, Солнечногорск, Кашира, Котельники, Нахабино, Красноармейск, Протвино, Истра, Шатура, Луховицы, Можайск, Дедовск, Ликино-Дулево, Апрелевка, Красноармейск, Озеры, Санкт-Петербург, Екатеринбург, Владимир, Иваново, Калуга, Кострома, Курск, Липецк, Муром, Новосибирск, Обнинск, Омск, Орёл, Псков, Ржев, Ростов, Рязань, Смоленск, Сочи, Тамбов, Тверь, Тобольск, Томск, Тула, Уфа, Челябинск, Ярославль и другие города.
Лаборатория НТЦ «Эксперт» и оказывает услуги по тепловизионному обследованию промышленных и жилых объектов. Целью тепловизионного обследования является поиск аномальных температурных участков, по которым можно судить о техническом состоянии объектов контроля. Основные задачи, решаемые тепловизионным обследованием это снижение теплопотерь зданий, поиск перегрева электросетей, мониторинг производственных процессов, выявление очагов плесени и других проблемных участков для своевременного обслуживания и снижения расходов.
По результатам тепловизионного обследования составляется подробный отчет, включающий наглядную тепловую карту (термограмму), заключение о качестве объекта. Заключение выдается аттестованной лабораторией теплового контроля и может быть использовано как для решения производственных задач, так и аргументировать позицию заказчика в спорах с подрядными организациям. Наша компания работает с юридическими и физическими лицами. Обследование возможно в московском регионе и за его пределами. Помимо проведения контроля, наша организация оказывает услуги по аттестации специалистов и лабораторий теплового контроля, помощь в подборе необходимого оборудования.
Тепловизионное обследование проводится с применением современных промышленных тепловизоров и других приборов. Используемые в работе приборы внесены в Госреестр и имеют свидетельство о поверке. Тепловизоры обладают высокой температурной чувствительностью позволяющей различать на термограмме объекты с разницей температур менее 1°С. Диапазон измеряемой температуры находится в пределах от -20°C до 350°C.
Условная классификация обследуемых объектов и типов выявляемых нарушений приведена в таблице:
Группа объектов | Тип объекта | Тип выявляемых нарушений | Основные нормативы | Примеры термограммы |
Промышленные, жилые и административные здания | цеха, многоквартирные дома, квартиры, дачи, школы, больницы |
|
ГОСТ Р 54852-2011 СП 50.13330.2012 (актуализированная редакция СНиП 23-02-2003) ГОСТ 25380-2014 |
![]() ![]() ![]() |
Промышленные сооружения | дымовые трубы, мосты, градирни, стальные конструкции |
|
РД-13-04-2006 | ![]() |
Машины и оборудование | Транспорт, котлы, холодильники, двигатели, конвейеры, насосы, лопатки турбин, компрессоры, зубчатые передачи |
|
РД-13-04-2006 | ![]() |
Энергетические сети | трубопроводы, ЛЭП, ЦТП, печи, котлы, радиаторы отопления, солнечные батареи |
|
РД-13-04-2006 РД 153-34.0-20.364-00 |
![]() ![]() ![]() |
Электрооборудование | распределительные щиты, трансформаторы, конденсаторы, генераторы, предохранители, силовые кабели, радиоэлектроника, печатные платы |
|
РД 153-34.0-20.363-99 | ![]() |
Примерные цены тепловизионного обследования
Объекты | Стоимость работ | |
Квартиры | 1 комната | 3 500 - 5 000 руб. (термограмма / полный отчет) |
2 комнаты | 4 500 - 6 000 руб. (термограмма / полный отчет) | |
3-5 комнатные | 5 000 - 7 000 руб. (термограмма / полный отчет) | |
Коттеджи | до 150 м2 | 4 000 - 6 000 руб. (термограмма / полный отчет) |
150 - 350 м2 | 6 000 - 8 000 руб. (термограмма / полный отчет) | |
350 - 500 м2 | 7 000 - 10 000 руб. (термограмма / полный отчет) | |
Здания | до 1000 м2 | 30 руб. за 1 м2 |
1000 - 5000 м2 | 25 руб. за 1 м2 | |
5000 -10000 м2 | 20 руб. за 1 м2 | |
Электрощиты | до 1 м2 | 1000 руб. за щит |
1 - 3 м2 | 2000 руб. за щит | |
3 - 5 м2 | 3000 руб. за щит | |
Трансформаторы | 6-10 кВ | 6 000 руб. |
35 кВ | 15 000 руб. | |
110-220 кВ | 20 000 руб. | |
Кабели и трубопроводы | 1 пог. м. шириной до 1 м | 30 руб. за погонный метр |
1 пог. м. шириной до 2 м | 40 руб. за погонный метр | |
1 пог. м. шириной до 3 м | 50 руб. за погонный метр | |
Аренда тепловизора (с оператором) | 3 500 руб. за 1 час работ |
Дополнительная информация:
- Пример отчета по результатам тепловизионного контроля
- Практическое руководство по термографии от компании Testo
- Введение в термографию от компании Fluke
- Применение тепловизоров в профилактическом техническом обслуживании (Flir)
- Пособие по выбору тепловизора
- Ассортимент поставляемых тепловизоров и других приборов теплового контроля
- Перечень ГОСТов по тепловому контролю
- Статья - «Диагностика строительных конструкция методом инфракрасной термографии»
- Статья – «Комплексный тепловой контроль зданий и строительных сооружений
- Статья – «Оценка фактической теплозащиты зданий методом теплового контроля»
- Статья – «Опыт применения теплового контроля в нефтепереработке»
- Статья – «Тепловой контроль изделий микроэлектроники»
- Аттестация специалистов по тепловому методу
- Аттестация лабораторий по тепловому методу
- Квалификационное удостоверение НОАП
- Свидетельство о поверке тепловизора
- Свидетельство об аттестации лаборатории
Заявки на тепловизионное обследование можно отправить по адресу kontrol@ntcexpert.ru. Смотрите так же разделы – Услуги по тепловому контролю, Аренда тепловизора, Проведение работ по НК, Аттестация лабораторий НК, Обучение и аттестация дефектоскопистов, Нормативная база по НК в том числе ГОСТы, РД, ПНАЭ, EN, ISO
Проведение теплового (тепловизионного) обследования возможно на территории Московской области и в других регионах РФ в том числе городах: Москва, Дмитров, Долгопрудный, Химки, Зеленоград, Красногорск, Балашиха, Королев, Жуковский, Люберцы, Лобня, Подольск, Электросталь, Коломна, Одинцово, Домодедово, Щелково, Серпухов, Ногинск, Пушкино, Сергиев Посад, Воскресенск, Ивантеевка, Дубна, Егорьевск, Чехов, Клин, Подольск, Реутов, Видное, Ступино, Наро-Фоминск, Фрязино, Лыткарино, Дзержинский, Солнечногорск, Кашира, Котельники, Нахабино, Красноармейск, Протвино, Истра, Шатура, Луховицы, Можайск, Дедовск, Ликино-Дулево, Апрелевка, Красноармейск, Озеры, Санкт-Петербург, Екатеринбург, Владимир, Иваново, Калуга, Кострома, Курск, Липецк, Муром, Новосибирск, Обнинск, Омск, Орёл, Псков, Ржев, Ростов, Рязань, Смоленск, Сочи, Тамбов, Тверь, Тобольск, Томск, Тула, Уфа, Челябинск, Ярославль и другие города.
Тепловизор достаточно дорогой прибор, поэтому для решения разовых задач, аренда выгоднее покупки. Аренда тепловизора особенно актуальна при сдаче-приемке квартиры или коттеджа, поиске источников потери тепла, перегрева электросетей, выявлении очагов плесени и других проблемных участков для своевременного обслуживания и снижения расходов. В настоящее время наша компания предоставляет услугу аренды тепловизора только с оператором. Наша компания работает с юридическими и физическими лицами. Аренда возможна для обследования объектов в Москве, области и ближайших регионах.
Помимо проведения контроля, наша организация оказывает услуги по аттестации специалистов и лабораторий теплового контроля, помощь в подборе необходимого оборудования. Обследование тепловизором проводится с применением современных промышленных тепловизоров с матрицей 320x240 пикселей. Рабочие тепловизоры внесены в Госреестр и имеют свидетельство о поверке.
Лаборатория НТЦ «Эксперт» также оказывает профессиональные услуги по тепловизионному обследованию промышленных и жилых объектов. По результатам тепловизионного обследования составляется подробный отчет, включающий наглядную тепловую карту (термограмму), заключение о качестве объекта. Заключение выдается аттестованной лабораторией теплового контроля и может быть использовано как для решения производственных задач, так и аргументировать позицию заказчика в спорах с подрядными организациям.
Примерная стоимость аренды тепловизора (с оператором)
Объекты | Стоимость работ | |
Квартиры | 1 комната | 3 500 - 5 000 руб. (термограмма / полный отчет) |
2 комнаты | 4 500 - 6 000 руб. (термограмма / полный отчет) | |
3-5 комнатные | 5 000 - 7 000 руб. (термограмма / полный отчет) | |
Коттеджи | до 150 м2 | 4 000 - 6 000 руб. (термограмма / полный отчет) |
150 - 350 м2 | 6 000 - 8 000 руб. (термограмма / полный отчет) | |
350 - 500 м2 | 7 000 - 10 000 руб. (термограмма / полный отчет) | |
Здания | до 1000 м2 | 30 руб. за 1 м2 |
1000 - 5000 м2 | 25 руб. за 1 м2 | |
5000 -10000 м2 | 20 руб. за 1 м2 | |
Электрощиты | до 1 м2 | 1000 руб. за щит |
1 - 3 м2 | 2000 руб. за щит | |
3 - 5 м2 | 3000 руб. за щит | |
Трансформаторы | 6-10 кВ | 6 000 руб. |
35 кВ | 15 000 руб. | |
110-220 кВ | 20 000 руб. | |
Кабели и трубопроводы | 1 пог. м. шириной до 1 м | 30 руб. за погонный метр |
1 пог. м. шириной до 2 м | 40 руб. за погонный метр | |
1 пог. м. шириной до 3 м | 50 руб. за погонный метр | |
Аренда тепловизора (с оператором) | 3 500 руб. за 1 час работ |
Условная классификация обследуемых объектов и типов выявляемых нарушений приведена в таблице:
Группа объектов | Тип объекта | Тип выявляемы нарушений | Основные нормативы | Примеры термограммы |
Промышленные, жилые и административные здания | цеха, многоквартирные дома, квартиры, дачи, школы, больницы |
|
ГОСТ Р 54852-2011 СП 50.13330.2012 (актуализированная редакция СНиП 23-02-2003) ГОСТ 25380-2014 |
![]() ![]() ![]() |
Промышленные сооружения | дымовые трубы, мосты, градирни, стальные конструкции |
|
РД-13-04-2006 | ![]() |
Машины и оборудование | Транспорт, котлы, холодильники, двигатели, конвейеры, насосы, лопатки турбин, компрессоры, зубчатые передачи |
|
РД-13-04-2006 | ![]() |
Энергетические сети | трубопроводы, ЛЭП, ЦТП, печи, котлы, радиаторы отопления, солнечные батареи |
|
РД-13-04-2006 РД 153-34.0-20.364-00 |
![]() ![]() ![]() |
Электрооборудование | распределительные щиты, трансформаторы, конденсаторы, генераторы, предохранители, силовые кабели, радиоэлектроника, печатные платы |
|
РД 153-34.0-20.363-99 | ![]() |
Дополнительная информация:
- Пример отчета по результатам тепловизионного контроля
- Практическое руководство по термографии от компании Testo
- Введение в термографию от компании Fluke
- Применение тепловизоров в профилактическом техническом обслуживании (Flir)
- Пособие по выбору тепловизора
- Ассортимент поставляемых тепловизоров и других приборов теплового контроля
- Перечень ГОСТов по тепловому контролю
- Статья - «Диагностика строительных конструкция методом инфракрасной термографии»
- Статья – «Комплексный тепловой контроль зданий и строительных сооружений
- Статья – «Оценка фактической теплозащиты зданий методом теплового контроля»
- Статья – «Опыт применения теплового контроля в нефтепереработке»
- Статья – «Тепловой контроль изделий микроэлектроники»
- Аттестация специалистов по тепловому методу
- Аттестация лабораторий по тепловому методу
- Квалификационное удостоверение НОАП
- Свидетельство о поверке тепловизора
- Свидетельство об аттестации лаборатории
Заявки на тепловизионное обследование можно отправить по адресу kontrol@ntcexpert.ru. Смотрите так же разделы – Услуги по тепловому контролю, Тепловизионное обследование, Проведение работ по НК, Аттестация лабораторий НК, Обучение и аттестация дефектоскопистов, Нормативная база по НК в том числе ГОСТы, РД, ПНАЭ, EN, ISO
Аренда тепловизора для физических и юридических лиц возможно на территории Московской области и в других регионах РФ в том числе городах: Москва, Дмитров, Долгопрудный, Химки, Зеленоград, Красногорск, Балашиха, Королев, Жуковский, Люберцы, Лобня, Подольск, Электросталь, Коломна, Одинцово, Домодедово, Щелково, Серпухов, Ногинск, Пушкино, Сергиев Посад, Воскресенск, Ивантеевка, Дубна, Егорьевск, Чехов, Клин, Подольск, Реутов, Видное, Ступино, Наро-Фоминск, Фрязино, Лыткарино, Дзержинский, Солнечногорск, Кашира, Котельники, Нахабино, Красноармейск, Протвино, Истра, Шатура, Луховицы, Можайск, Дедовск, Ликино-Дулево, Апрелевка, Красноармейск, Озеры, Санкт-Петербург, Екатеринбург, Владимир, Иваново, Калуга, Кострома, Курск, Липецк, Муром, Новосибирск, Обнинск, Омск, Орёл, Псков, Ржев, Ростов, Рязань, Смоленск, Сочи, Тамбов, Тверь, Тобольск, Томск, Тула, Уфа, Челябинск, Ярославль и другие города.
Наша лаборатория оказывает услуги по тепловому контролю промышленных и жилых объектов. По результатам контроля составляется подробный отчет, включающий наглядную тепловую карту и заключение о качестве объекта (примеры). Заключение выдается аттестованной лабораторией теплового контроля и может быть использовано как для решения производственных задач, так и аргументировать позицию заказчика в спорах с подрядными организациям. Высокий уровень организации рабочих процессов нашей ЛНК дополнительно подтвержден сертификатом соответствия ISO 9001. Наша компания работает с юридическими и физическими лицами. Проведение работ возможно в московском регионе и за его пределами. Помимо проведения контроля, наша организация оказывает услуги по аттестации специалистов и лабораторий теплового контроля, помощь в подборе необходимого оборудования.
Целью теплового контроля является поиск аномальных температурных участков, по которым можно судить о техническом состоянии объектов контроля. Основные задачи, решаемые с применением теплового контроля это снижение теплопотерь, поиск перегрева электросетей, мониторинг производственных процессов, выявление очагов плесени и других проблемных участков для своевременного техобслуживания и снижения расходов. Тепловой контроль проводится с применением современных промышленных тепловизоров и других приборов. Используемые в работе приборы внесены в Госреестр и имеют свидетельство о поверке. Тепловизоры обладают высокой температурной чувствительностью позволяющей различать на термограмме объекты с разницей температур менее 1°С. Диапазон измеряемой температуры находится в пределах от -20°C до 350°C.
Условная классификация контролируемых объектов и типов выявляемых нарушений приведена в таблице:
Группа объектов | Тип объекта | Тип выявляемых нарушений | Основные нормативы | Примеры термограммы |
Промышленные, жилые и административные здания | цеха, многоквартирные дома, квартиры, дачи, школы, больницы |
|
ГОСТ Р 54852-2011 СП 50.13330.2012 (актуализированная редакция СНиП 23-02-2003) ГОСТ 25380-2014 |
![]() ![]() ![]() |
Промышленные сооружения | дымовые трубы, мосты, градирни, стальные конструкции |
|
РД-13-04-2006 | ![]() |
Машины и оборудование | Транспорт, котлы, холодильники, двигатели, конвейеры, насосы, лопатки турбин, компрессоры, зубчатые передачи |
|
РД-13-04-2006 | ![]() |
Энергетические сети | трубопроводы, ЛЭП, ЦТП, печи, котлы, радиаторы отопления, солнечные батареи |
|
РД-13-04-2006 РД 153-34.0-20.364-00 |
![]() ![]() ![]() |
Электрооборудование | распределительные щиты, трансформаторы, конденсаторы, генераторы, предохранители, силовые кабели, радиоэлектроника, печатные платы |
|
РД 153-34.0-20.363-99 | ![]() |
Примерная стоимость работ по тепловому контролю
Объекты | Стоимость работ | |
Коттеджи и квартиры | до 150 м2 | 8 000 - 10 000 руб. (термограмма / полный отчет) |
150 - 350 м2 | 10 000 - 15 000 руб. (термограмма / полный отчет) | |
350 - 500 м2 | 15 000 - 20 000 руб. (термограмма / полный отчет) | |
Здания | до 1 000 м2 | 30 руб. за 1 м2 |
1 000 – 5 000 м2 | 25 руб. за 1 м2 | |
5 000 -10 000 м2 | 20 руб. за 1 м2 | |
Трансформаторы и электрощиты | 6-10 кВ | 6 000 руб. |
35 кВ | 15 000 руб. | |
110-220 кВ | 20 000 руб. | |
Аренда тепловизора (с оператором) | 3 500 руб. за 1 час работ |
Дополнительная информация:
- Пример отчета по результатам тепловизионного контроля
- Практическое руководство по термографии от компании Testo
- Введение в термографию от компании Fluke
- Применение тепловизоров в профилактическом техническом обслуживании (Flir)
- Пособие по выбору тепловизора
- Ассортимент поставляемых тепловизоров и других приборов теплового контроля
- Перечень ГОСТов по тепловому контролю
- Статья - «Диагностика строительных конструкция методом инфракрасной термографии»
- Статья – «Комплексный тепловой контроль зданий и строительных сооружений
- Статья – «Оценка фактической теплозащиты зданий методом теплового контроля»
- Статья – «Опыт применения теплового контроля в нефтепереработке»
- Статья – «Тепловой контроль изделий микроэлектроники»
- Аттестация специалистов по тепловому методу
- Аттестация лабораторий по тепловому методу
- Квалификационное удостоверение НОАП
- Свидетельство о поверке тепловизора
- Свидетельство об аттестации лаборатории
Заявки на услуги по тепловому контролю можно отправить по адресу kontrol@ntcexpert.ru. Смотрите так же разделы – Аренда тепловизора, Тепловизионное обследование, Проведение работ по НК, Аттестация лабораторий НК, Обучение и аттестация дефектоскопистов, Нормативная база по НК в том числе ГОСТы, РД, ПНАЭ, EN, ISO
Проведение теплового (тепловизионного) контроля возможно на территории московской области и в других регионах РФ в том числе городах: Москва, Дмитров, Долгопрудный, Химки, Зеленоград, Красногорск, Балашиха, Королев, Жуковский, Люберцы, Лобня, Подольск, Электросталь, Коломна, Одинцово, Домодедово, Щелково, Серпухов, Ногинск, Пушкино, Сергиев Посад, Воскресенск, Ивантеевка, Дубна, Егорьевск, Чехов, Клин, Подольск, Реутов, Видное, Ступино, Наро-Фоминск, Фрязино, Лыткарино, Дзержинский, Солнечногорск, Кашира, Котельники, Нахабино, Красноармейск, Протвино, Истра, Шатура, Луховицы, Можайск, Дедовск, Ликино-Дулево, Апрелевка, Красноармейск, Озеры, Санкт-Петербург, Екатеринбург, Владимир, Иваново, Калуга, Кострома, Курск, Липецк, Муром, Новосибирск, Обнинск, Омск, Орёл, Псков, Ржев, Ростов, Рязань, Смоленск, Сочи, Тамбов, Тверь, Тобольск, Томск, Тула, Уфа, Челябинск, Ярославль и другие города.
Принцип измерения по методу Leeb
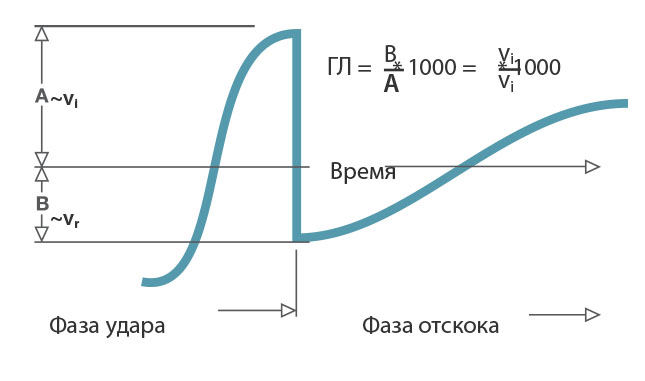
Принцип измерения твердости по Leeb основывается на динамическом методе (отскок). Боек с твердосплавным индентором приводится в движение силой сжатия пружины перпендикулярно поверхности тестируемого образца. Удар о поверхность деформирует поверхность тестируемого образца, и приводит к потере кинетической энергии бойка. Эта потеря энергии определяется путем сравнения скоростей vi и vr бойка на определенном расстоянии от поверхности образца до и после удара о поверхность, соответственно.
Скорости измеряются при помощи постоянного магнита в бойке, который создает индуктивное напряжение в катушке, расположенной в точно заданном месте датчика. Наводимая ЭДС пропорциональна скорости бойка. Дальнейшая обработка сигнала обеспечивает индикацию твердости. Описание динамических твердомеров работающих по методу Leeb здесь.
Шкалы | Приборы | Диапазон | ||
Диапазон измерений |
Сталь и литая сталь | Vickers Brinell Rockwell Shore Rm Н/мм² |
HV HB HRB HRC HRA HS σ1 σ2 σ3 |
81-955 81-654 38-100 20-68 30-99 275-2194 616-1480 449-847 |
Инструментальная сталь холодной обработки | Vickers Rockwell |
HV HRC |
80-900 21-67 |
|
Нержавеющая сталь | Vickers Brinell Rockwell |
HV HB HRB HRC |
85-802 85-655 46-102 20-62 |
|
Чугун, слоистый графит GG | Brinell Vickers Rockwell |
HB HV HRC |
90-664 90-698 21-59 |
|
Чугун, графит шаровидный GGG | Brinell Vickers Rockwell |
HB HV HRC |
95-686 96-724 21-60 |
|
Алюминиевые сплавы | Brinell Vickers Rockwell |
HB HV HRB |
19-164 22-193 24-85 |
|
Медноцинковые сплавы (латунь) | Brinell Rockwell |
HB HRB |
40-173 14-95 |
|
Сплавы CuAI/CuSn (бронза) | Brinell | HB | 60-290 | |
Кованные сплавы меди, низколегированные | Brinell | HB | 45-315 | |
» Другие комбинации можно получить путем пользовательских преобразований | ||||
Требования к тестируемому образцу |
Подготовка поверхности | Шероховатость, класс ISO 1302 | N7 | |
Максимальная глубина шероховатости Rt (мкм/мкдюйм) | 10 / 400 | |||
Средняя шероховатость Ra (мкм/мкдюйм) | 2 / 80 | |||
Минимальная масса образца | Образец (непосредственно) (кг / фунт) | 5 / 11 | ||
На массивной плите (кг / фунт) | 2 / 4,5 | |||
Притертый к плите (кг / фунт) | 0,05 / 0,2 | |||
Минимальная толщина образца | Непритертый (мм / дюйм) | 25 / 0,98 | ||
Притертый (мм / дюйм) | 3 / 0,12 | |||
Толщина поверхностного слоя (мм / дюйм) | 0,8 / 0,03 | |||
Размер отпечатка на контролируемой поверхности | при 300 HV, 30 HRC | Диаметр (мм / дюйм) | 0,54 / 0,021 | |
Глубина (мкм/мкдюйм) | 24 / 960 | |||
при 600 HV, 55 HRC | Диаметр (мм / дюйм) | 0,45 / 0,017 | ||
Глубина (мкм/мкдюйм) | 17 / 680 | |||
при 800 HV, 63 HRC | Диаметр (мм / дюйм) | 0,35 / 0,013 | ||
Глубина (мкм/мкдюйм) | 10 / 400 |
Разработка эталона твердости по Либу второго разряда
Источник: журнал "В мире НК" 2017. Том 20. №1.
Авторы:
Гоголинский Кирилл Валерьевич - директор Всероссийского научно-исследовательского института метрологии имени Д.И. Менделеева (Санкт-Петербург), д.т.н.
Никазов Артём Александрович - аспирант кафедры «Приборостроение» Национального минерального университета «Горный» (Санкт-Петербург).
Рассмотрены технические принципы метода измерения твёрдости по шкалам Либа и текущее состояние метрологического обеспечения метода. В связи с разработкой гармонизированного стандарта и необходимостью реализации метрологической цепи согласно структуре обеспечения прослеживаемости, а также определения и распространения шкал твёрдости рассмотрены и обоснованы методические и технологические решения для реализации стационарного прибора, воспроизводящего метод Либа, для эталона второго разряда. Исходя из проведённого анализа, предложена система измерения скорости на основе двух катушек индуктивности и представлен расчёт её параметров. Приведены результаты испытания макета стационарного прибора, воспроизводящего метод Либа, подтвердившие его соответствие требованиям иностранных стандартов и проекту гармонизированного стандарта.
V. A. Syasko , К. V. Gogolinskiy , A. A. Nikazov
Elaboration of Leeb hardness calibration machine
The article deals with the development of Leeb hardness secondary calibration machine. The article describes the technical principles of the Leeb hardness measurement method and the current state of metrological assurance in the Russian Federation. The analysis of Leeb hardness calibration machines of Germany and Switzerland are con ducted. The draft of metrological traceability (metrological chain) for disseminating of Leeb hardness scales is proposed. In connection with the development of harmonized standard and the need for the implementation of the metrological traceability of Leeb hardness method, as well as the identifying and disseminating of hardness scales, methodological and technological solutions for the Leeb hardness secondary calibration machine are considered. Based on the analysis of required metrological characteristics of secondary calibration machine and hardness reference blocks, the construction of velocity measuring system with two inductors and system parameters calculation with required metrological characters tics are suggested. Test results of Leeb hardness secondary calibration machine layout for HLD scale confirmed its compliance with international standards and the draft of harmonized standard. The obtained results can be used to develop the Leeb hardness secondary calibration machine to equip the standardization and metrology centers of the Russian Federation and abroad.
Применение динамических методов контроля твёрдости, основанных на измерении параметров отскока падающего ударника, получило широкое распространение в последние десятилетия. Преимущества таких методов — малые габариты твердомеров и возможность их использования вне измерительных лабораторий непосредственно на поверхностях деталей, трубопроводах, объектах энергетики и т.д.
Чаще всего в портативных динамических твердомерах реализуется метод измерения твёрдости по Либу, разработанный в Европе в 1970-х гг. сотрудниками фирмы Proceq. Суть метода заключается в измерении соотношения скоростей V падающего ударника до и после соударения с поверхностью испытуемого образца, при этом твёрдость по Либу HL рассчитывается в соответствии с формулой [1] HL = 100VR/VА, где VR — скорость отскока ударника; VA — скорость удара.
На сегодняшний день существует несколько различных шкал твёрдости по Либу для преобразователей, отличающихся радиусом R сферического индентора и массой т ударника, а также его кинетической энергией ЕА при ударе, зависящей от VА.
Метрологическое обеспечение метода Либа в США и Европе регламентируется стандартами: DIN 50156 (части 1, 2 и 3) [2-4], ASTM А956 [5], ISO/DIS 16859 (1-3) [6-8]. До настоящего времени из-за отсутствия стандарта на метод измерения твёрдости по Либу в Российской Федерации динамические твердомеры вносятся в Госреестр средств измерений под видом твердомеров по стандартизованным шкалам статических методов. На практике производители твердомеров, обозначаемых как «динамические», «портативные», «малогабаритные» или «переносные», по сути, реализуют с теми или иными допущениями метод измерения твёрдости по Либу. Ситуация с метрологическим обеспечением динамических методов подробно рассмотрена в [9,10].
В ООО «КОНСТАНТА» разработан проект гармонизированного стандарта на метод измерения твёрдости по Либу на основе стандартов [6-8]. На проект стандарта получены положительные отзывы, в том числе из ФГУП ВНИИФТРИ. Стандарт определяет требования к твердомерам, предназначенным для измерения твёрдости металлов и сплавов по Либу, ударникам, испытуемым образцам, методикам поверки твердомеров, требования к производству и поверке эталонных мер твёрдости, а также требования к эталонам и средствам измерений.
Для реализации метрологической цепи согласно структуре обеспечения прослеживаемости, а также для определения и распространения шкал твёрдости (рис. 1) необходима разработка эталона не только первого, но и второго разряда, для многочисленных центров стандартизации и метрологии (ЦСМ).
Рис. 1. Обобщенная структура обеспечения прослеживаемости (метрологической цепи) для определения и распространения шкал твердости Либа.
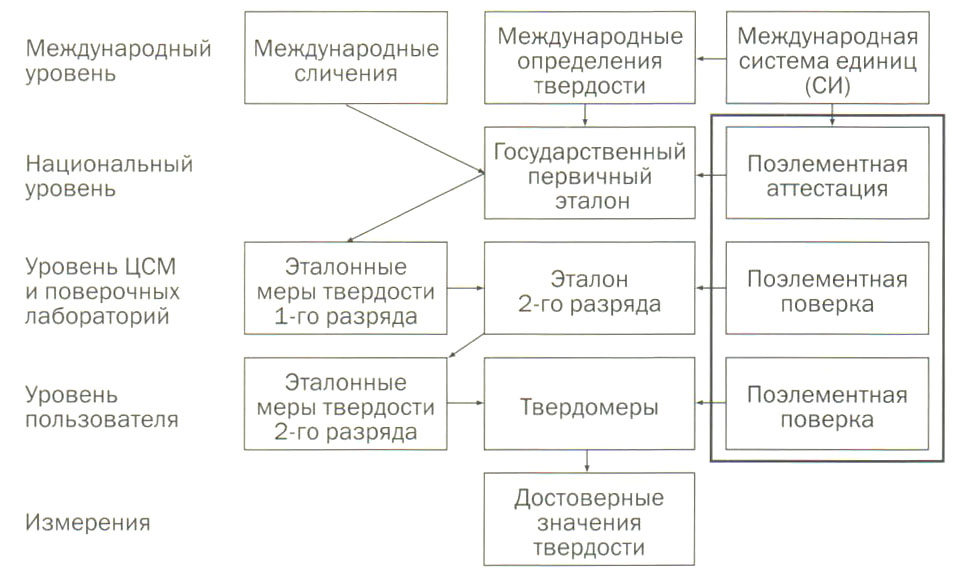
После принятия стандарта должно будет произойти достаточно быстрое увеличение парка твердомеров, реализующих метод Либа, а также мер твердости для их поверки. В связи с этим необходимо будет оснастить большое число ЦСМ эталонами второго разряда, которые должны иметь заданные технические характеристики при минимальной цене, определяемой их себестоимостью. Рассмотрим их возможные конструкции.
Проект стандарта определяет комплект (стационарный прибор, воспроизводящий метод Либа, и комплект средств измерений для поэлементного контроля его параметров) и параметры эталона второго разряда: VA, m, R и материал индентора, проверяемые при поэлементной поверке (табл. 1), а также диапазоны твёрдости и метрологические характеристики при поверке по эталонным мерам твёрдости 1-го разряда. В ударных преобразователях рабочих средств измерений (твердомерах) ударник разгоняется до необходимой скорости при помощи пружины. В известных эталонных установках ударник разгоняется под воздействием гравитационного поля Земли.
Табл. 1. Параметры эталона второго разряда по методу Либа
Параметр | Ед. измерения | Тип ударного преобразователя | ||||||
D | S | E | DL | D+15 | C | G | ||
Скорость удара VА | м/с | 2,05 | 2,05 | 2,05 | 1,82 | 1,70 | 1,40 | 3,00 |
Предельно допустимое отклонение скорости удара | м/с | ±0.0025 | ±0.0025 | ±0.0025 | ±0.0020 | ±0.0020 | ±0.0020 | ±0.0050 |
Масса ударника m | г | 5,45±0,03 | 5,45±0,03 | 5,45±0,03 | 7,25±0,03 | 7,25±0,03 | 3,10±0,03 | 20,00±0,03 |
Радиус сферического наконечника индентора R | мм | 1,500±0,003 | 1,500±0,003 | 1,500±0,003 | 1,390±0,003 | 1,500±0,003 | 1,500±0,003 | 2,500±0,003 |
Материал индентора | WC-Co* | с** | PCD*** | WC-Co | WC-Co | WC-Co | WC-Co | |
Твердость индентора по Виккерсу | HV2 | 1600 ± 50 | 1600 ± 50 | >4500 | 1600 ± 50 | 1600 ± 50 | 1600 ± 50 | 1600 ± 50 |
* Вольфрам-карбид кобальта ** Керамика *** Поликристаллический алмаз |
Табл. 2. Диапазоны твердости по Либу и метрологические характеристики эталонов второго разряда при поверке по эталонным мерам твердости первого разряда.
Тип ударного преобразователя | Диапазоны твердости, HL* | Минимальная повторяемость, % | Предельная погрешность, % | |||||
D, D + 15 | <500 500-700 >700 |
1,0 1,0 1,0 |
±2,0 ±1,5 ±1,0 |
|||||
DL, S | <700 700-850 >850 |
1,0 1,0 1,0 |
±2,0 ±1,5 ±1,0 |
|||||
С, Е | <600 600-750 >750 |
1,0 1,0 1,0 |
±2,0 ±1,5 ±1,0 |
|||||
G | <450 450-600 >600 |
1,0 1,0 1,0 |
±2,0 ±1,5 ±1,0 |
|||||
*HLD для ударных преобразователей типа D; HLD+15 для ударных преобразователей типа D+15; HLDL для ударных преобразователей типа DL; HLS для ударных преобразователей типа S; HLC для ударных преобразователей типа С; HLE для ударных преобразователей типа Е; HLG для ударных преобразователей типа G. |
Известны две реализации эталонных установок, принципиально отличающихся способом измерения скорости ударника: на основе лазерного интерферометра и на основе катушки индуктивности.
Система измерения скорости на основе лазерного интерферометра используется в эталоне, разработанном в Германии (рис. 2). Установка реализует непрерывное измерение скорости движения ударника в процессе падения и отскока. Для измерения используется лазерный интерферометр на базе He-Ne-лазера фирмы SIOS Messtechnik GmbH, который имеет стабилизированную частоту излучения. В данной конструкции форма ударников отличается от применяемых в твердомерах, так как они должны обеспечивать отражение луча интерферометра.
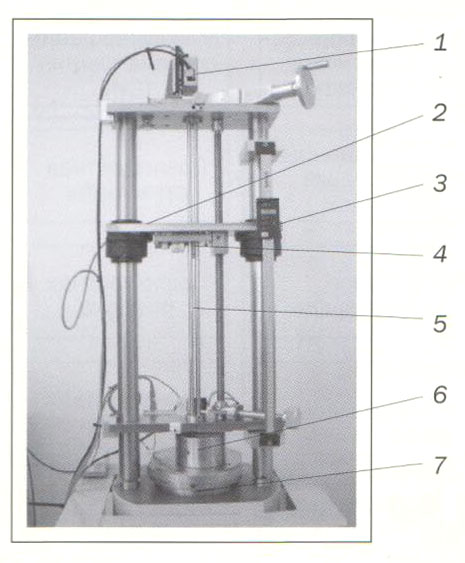
Рис. 2. Структура и техническая реализация эталона на основе интерферометра:
- лазерный интерферометр,
- система позиционирования высоты сброса ударника,
- цифровая линейка,
- ударник,
- направляющие стержни,
- мера твердости,
- стол.
Система измерения скорости с катушкой индуктивности реализована в эталоне, разработанном на базе твердомера Equotip 3 (рис. 3). В системе используется катушка индуктивности и ударник с постоянным магнитом в корпусе, аналогичный рабочим средствам измерения швейцарского производителя. Ударник с встроенным магнитом, пролетая сквозь катушку индуктивности со скоростью VА при падении, наводит в ней ЭДС, амплитудой ЕА. При отскоке, двигаясь через катушку вверх со скоростью VR, наводит в ней ЭДС амплитудой ER противоположной полярности (рис. 4). В рамках работы над стандартом был разработан макет стационарного прибора, воспроизводящего метод Либа, для эталона второго разряда. Для решения задачи измерения скорости была выбрана система с использованием катушек индуктивности. Согласно стандартам для вычисления кода Либа используется отношение скоростей удара и отскока, однако в рабочих средствах измерений, в соответствии с теми же стандартами, расчёт кода по Либу выполняется по формуле: HL = 100 ЕR/ЕА.
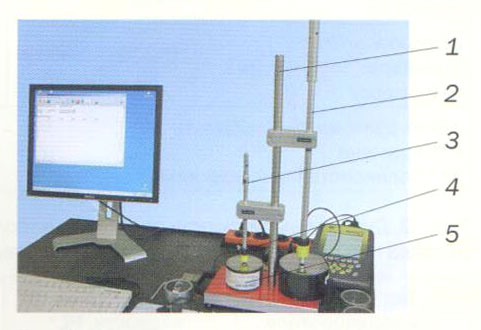
Рис. 3. Эталон на базе твердомера Equotip 3 фирмы Proceq (Швейцария):
- несущая стойка,
- направляющая трубка для датчика типа D,
- направляющая трубка для датчика типа G,
- катушка индуктивности,
- мера твердости.
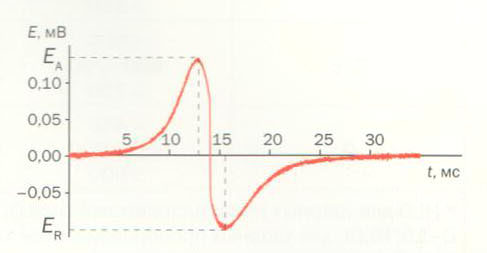
Рис. 4. Диаграмма ЭДС, наведенной на катушке индуктивности при измерении твердости.
На взгляд авторов система с катушкой индуктивности является предпочтительной ввиду того, что она аналогична технологическому решению, используемому в рабочих средствах измерений. При этом для измерения VA предлагается установка дополнительной катушки индуктивности.
Система измерения VA (рис. 5) состоит из двух катушек L1 и L2, расположенных друг от друга на расстоянии ∆h. ЭДС с катушек поступают через измерительные усилители на входы аналого-цифровых преобразователей микроконтроллера, вычисляющего значение скорости.
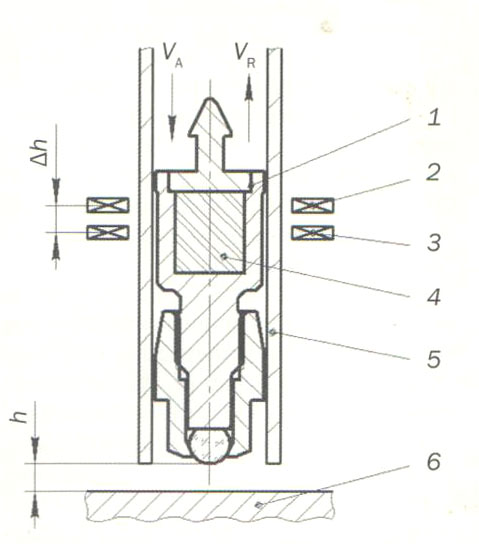
Рис. 5. Структура системы измерения VA с двумя катушками индуктивности:
- ударник,
- дополнительная катушка L1,
- основная катушка L2,
- постоянный магнит ударника,
- направляющая трубка,
- испытуемый образец.
Расчеты показали, что для ударника типа D VA =2,05±0,0025 м/с обеспечивается при сбросе свободно падающего ударника с высоты H = 214±0,26 мм.
Скорость ударника должна измеряться при h не более 2 мм. После прохождения катушки L2 со скоростью V скорость ударника продолжает линейно увеличиваться до требуемой скорости VA = V + gt.
При этом h = t(VA + V)/2.
Время t прохождения расстояния h может быть найдено из решения квадратного уравнения: h = t(VA+V)/2 = t(VA + VA - gt)/2 = VAt - gt2/ 2;
откуда gt2 - 2 VAt + 2h = 0
и t=[VA- (VA2 - 2hg)1/2]/ g=[2,05 - (2,052- 2*0,002*9,819)1/2]/9,819≈ 0,978 мс.
Для обеспечения требуемых характеристик необходимо контролировать фактическую скорость и высоту h. Выполнить это можно по фиксации моментов прохождения ударником катушек L1 и L2, соответствующих амплитудам EА1 и ЕА2 (рис. 4). Фиксация t1 выполняется по пику ЭДС при прохождении катушки L1, а фиксация t2 — при прохождении катушки L2 на расстоянии ∆h между ними. Параметры определяются из решения системы уравнений:
h = VAt1+gt12/2;
h + ∆h = VAt2+gt22/2.
Расстояние между измерительными катушками ∆h = VA(t2 – t1) +g(t22 – t12)/2.
Скорость в момент удара:
VA = [∆h - g(t22 – t12)/2]/(t2 – t1).
С учётом того, что ∆t=t2-t1, имеем: VА=(∆h/∆t)-g(t12 + ∆t/2).
На точность вычисления скорости влияют погрешности измерения ∆h и ∆t. Чувствительность к вариации ∆h: SVA(∆h) = d(V0)/d(∆h) = (1/∆t).
При допустимой погрешности задания расстояния между катушками от истинного значения δ∆h погрешность измерения скорости VA составит: ∆VA=SVA(∆h)* δ∆h = δ∆h/∆t.
Допустимое отклонение скорости определено стандартом: ∆VA = ±2,5 мм/с. Тогда предельно допустимая погрешность задания расстояния между катушками: δ∆h= ∆VA ∆t.
Чувствительность к погрешности измерения времени движения ударника после пика ЭДС:
SVA(t1) = d |VA | /d(t1) = d | [∆h/(t2 – t1)] - g [t1 + (t2 - t1)/2] | /d(t1) = ∆h/∆t2+g/2;
SVA(t2) = d | VA | /d(t2) = d | [∆h/(t2 – t1)]- g [t1 + (t2 - t1)/2] | /d(t2) = ∆h/∆t2 + g/2.
Общая чувствительность к погрешности измерения времени с учётом равной вероятности знака погрешности:
SVA(t)= ISVA(t1) I+ ISVA(t2)l = 2∆h/∆t2+g.
При допустимой погрешности измерения времени δ1 погрешность измерения скорости VA составит:
∆VA = SV0(t) δ1 = (2∆h/∆t2+g) δ1.
Так как ∆VA = ±2,5 мм/с, то предельно допустимая погрешность измерения времени δ1 = ∆VA /(2∆h/∆t2 + g) = ∆VA∆t2/(2∆h + g∆t2).
Анализ показывает, что оцифровка ЭДС с выходов катушек должна производиться с частотой fкв = 1 МГц. При этом определение моментов t1 и t2, соответствующих пикам ЭДС. а также момента удара должны производиться после оцифровки ЭДС с полосой пропускания 100 кГц. Расстояние ∆h = 1 мм должно быть обеспечено с погрешностью не хуже ±10 мкм.
По результатам проведённой работы был разработан макет стационарного прибора, воспроизводящего метод Либа, для эталона твёрдости второго разряда по шкале D, параметры которого приведены в табл. 3. Катушки индуктивности L1 и L2 имели следующие размеры: внутренний диаметр 12 мм, внешний диаметр 17 мм, длина намотки 0,5 мм.
Табл. 3. Параметры макета эталона твердости по Либу второго разряда (по шкале D)
Параметры | Ед. измерения | Значения |
Скорость удара, VA | м/с | 2,05 ±0,0025 |
Высота сброса ударника | мм | 214 ±0,26 |
Масса ударника, m | г | 5,45 ±0,03 |
Радиус сферического индентора, R | мм | 1,5 ±0,003 |
Материал индентора | WC-Co | |
Твердость индентора по Виккерсу | HV2 | 1600 ±50 |
Частота оцифровки ЭДС | МГц | 1 |
Расстояние между катушками, ∆h | мм | 1±0,01 |
Расстояние h | мм | <2 |
Предварительные испытания макета эталона были произведены с использованием комплекта мер твёрдости HLD491.5. HLD608 и HLD770, изготовленных компанией Proceq и поверенных в Physikalisch-Technische Bundesanstalt (РТВ). При измерениях на мерах ∆VA < ±2,5 мм/с. Результаты измерений представлены в табл. 4.
Табл. 4. Результаты экспериментов
Шкала твердости | HLD | |||
Твердость эталонной меры твердости, ед.тв. | 491,5 | 608 | 770 | |
Показания прибора, ед.тв. | 1 | 484 | 600 | 770 |
2 | 487 | 599 | 765 | |
3 | 489 | 601 | 766 | |
4 | 488 | 605 | 766 | |
5 | 490 | 605 | 767 | |
6 | 483 | 607 | 769 | |
7 | 484 | 603 | 761 | |
8 | 485 | 604 | 762 | |
9 | 486 | 607 | 759 | |
10 | 487 | 605 | 761 | |
Среднее значение показаний, ед.тв. | 487 | 604 | 764 | |
Абс. погрешность, ед.тв. | 5 | 4 | 6 | |
Размах показаний, ед.тв. | 5 | 2 | 1 | |
СКО | 2,3 | 2,8 | 3,3 | |
Повторяемость, % | 0,5 | 0,5 | 0,4 | |
Предельная погрешность, % | 0,97 | 0,72 | 0,78 |
Выполненные эксперименты с использованием разработанного макета стационарного прибора, воспроизводящего метод Либа, показали, что предложенные технические решения могут быть положены в основу при разработке эталона твёрдости по Либу второго разряда для центров стандартизации и метрологии.
Литература
- Leeb D. New dynamic method for hardness testing of metallic materials. — In: VDI-Report №308,1978. pp. 123-128.
- DIN 50156-1:2007/Metallic materials — Leeb hardness test — Part 1: Test Method.
- DIN 50156-2:2007/Metallic materials — Leeb hardness test — Part 2: Verification and calibration of the testing devices.
- DIN 50156-3:2007/Metallic materials — Leeb hardness test — Part 3: Calibration of reference blocks.
- ASTM A956/Standard Test Method for Leeb Hardness Testing of Steel Products. 2012.
- ISO/DIS 16859-l:2015/Metallic materials — Leeb hardness test — Part 1: Test method.
- ISO/DIS 16859-2:2015/Metallic materials — Leeb hardness test — Part 2: Verification and calibration of the testing devices.
- ISO/DIS 16859-3:2015/Metallic materials — Leeb hardness test — Part 3: Calibration of reference test blocks.
- Гоголинский К. В., Сясько В. А. Метрологическое обеспечение динамических методов измерения твёрдости в Российской Федерации: существующие проблемы и пути их решения. — В мире НК. 2014. № 1 (63). С. 69-76.
- Потапов А.И., Сясько В.А.. Гоголинский К. В., Никазов А. А. Обеспечение единства измерений твёрдости динамическим методом в Российской Федерации. — Контроль. Диагностика. 2016. № 12. С. 44-50.
Методы и приборы неразрушающего контроля бетона
Для оценки состояния бетонных конструкций необходим всесторонний анализ факторов, влияющих на их эксплуатационные характеристики, такие как прочность, толщина защитного слоя, диаметр арматуры, теплопроводность, влажность, адгезия покрытий и т.д. Неразрушающие методы контроля особенно актуальны, когда характеристики бетона и арматуры неизвестны, а объёмы контроля значительны. Методы НК дают возможность контроля как в лабораторных условиях, так и на строительных площадках в процессе эксплуатации.
В чём плюсы неразрушающего контроля:
- Возможность не организовывать на площадке лабораторию оценки бетона.
- Сохранение целостности проверяемой конструкции.
- Сохранение эксплуатационных характеристик сооружений.
- Широкая сфера применения.
Лаборатория НТЦ «Эксперт» оказывает услуги по контролю бетона методами УЗК, магнитной индукции и методом упругого отскока. Данные методы дают возможность определять прочность бетона, наличие внутренних дефектов, глубину и диаметр арматуры. Неразрушающие методы применимы, когда нет возможности изъятия образцов для контроля прямыми методами, особенно в процессе строительства и реконструкции. Процедура обследования бетонных конструкций регламентирована ГОСТ 22690-2015 и ГОСТ 17624-2012. Общие правила проверки качества бетона изложены в ГОСТ 18105-2010.
При всем многообразии контролируемых параметров контроль прочности бетона занимает особое место, поскольку при оценке состояния конструкции определяющим фактором является соответствие фактической прочности бетона проектным требованиям.
Процедура обследований регламентирована ГОСТ 22690-2015 и ГОСТ 17624-2012. Общие правила проверки качества бетона изложены в ГОСТ 18105-2010. Неразрушающий контроль прочности бетона подразумевает применение механических методов (удар, отрыв, скол, вдавливание) и ультразвукового сканирования.
Контроль прочности готовых бетонных конструкций как правило проводится по графику, в установленном проектом возрасте, либо при необходимости, например, когда планируется реконструкция. Контроль прочности строящихся конструкций даёт возможность оценить распалубочную и отпускную прочность, сравнить реальные характеристики материала с паспортными.
Методы неразрушающего контроля прочности бетона делят на две группы
Прямые (методы местных разрушений) | Косвенные |
|
|
Прямые методы испытания бетона (методы местных разрушений)
Методы местных разрушений относят к неразрушающим условно. Их основное преимущество – достоверность. Они дают настолько точные результаты, что их используют для составления градуировочных зависимостей для косвенных методов. Испытания проводятся по ГОСТ 22690-2015.
Метод | Описание | Плюсы | Минусы |
Метод отрыва со скалыванием | Оценка усилия, которое требуется, чтобы разрушить бетон, вырывая из него анкер (видео). | - Высокая точность. - Наличие общепринятых градуировочных зависимостей, зафиксированных ГОСТом. |
- Трудоёмкость. - Невозможность использовать в оценке прочности густоармированных сооружений, сооружений с тонкими стенами. |
Скалывание ребра | Измерение усилия, которое требуется, чтобы сколоть бетон на углу конструкции. Метод применяется для исследования прочности линейных сооружений: свай, колонн квадратного сечения, опорных балок. | - Простота использования. - Отсутствие предварительной подготовки. |
- Не применим, если слой бетона меньше 2 см или существенно повреждён. |
Отрыв дисков | Регистрация усилия для разрушения бетона при отрыве от него металлического диска. Способ широко использовался в советское время, сейчас почти не применяется из-за ограничений по температурному режиму. | - Подходит для проверки прочности густоармированных конструкций. - Не такой трудоёмкий, как отрыв со скалыванием. |
- Необходимость подготовки: диски нужно наклеить на бетонную поверхность за 3-24 часа до проверки. |
Основные недостатки методов местных разрушений – высокая трудоёмкость, необходимость расчёта глубины прохождения арматуры, её оси. При испытаниях частично повреждается поверхность конструкций, что может повлиять на их эксплуатационные характеристики.
Косвенные методы испытания бетона
В отличие от методов местных разрушений, методы, основанные на ударно-импульсном воздействии на бетон, имеют большую производительность. Однако, контроль прочности бетона ведется в поверхностном слое толщиной 25-30 мм, что ограничивает их применение. В упомянутых случаях необходима зачистка поверхности контролируемых участков бетона или удаление поврежденного поверхностного слоя.
Неразрушающий контроль прочности бетона на заводах ЖБИ и в строительных лабораториях осуществляется после приведения градуировочных зависимостей приборов в соответствие с фактической прочностью бетона по результатам испытания контрольных партий в прессе.
Метод | Описание | Плюсы | Минусы |
Ударного импульса | Регистрация энергии, которая появляется при ударе специального бойка. Для обследований используется молоток Шмидта. Как работает молоток Шмидта |
- Компактное оборудование. - Простота. - Возможность одновременно устанавливать класс бетона. |
- Относительно невысокая точность |
Упругого отскока | Измерение пути бойка при ударе о бетон. Для обследования используют склерометр Шмидта и аналогичные устройства. | - Простота и скорость исследования. | - Жёсткие требования к процедуре подготовки контрольных участков. - Техника требует частой поверки. |
Пластической деформации | Измерение отпечатка, оставшегося на бетоне при ударе металлическим шариком. Метод устаревший, но используется часто. Для оценки применяют молоток Кашкарова и аппараты статического давления. Оценка прочности бетона молотком Кашкарова. |
- Доступность оборудования. - Простота. |
- Невысокая точность результатов. |
Ультразвуковой метод | Измерение скорости колебаний ультразвука, проходящего сквозь бетон. | - Возможность проводить массовые изыскания неограниченное число раз. - Невысокая стоимость исследований. - Возможность оценить прочность глубинных слоёв конструкции. |
- Повышенные требования к качеству поверхности. - Требуется высокая квалификация сотрудника. |
Метод ударного импульса
Метод ударного импульса – самый распространённый среди неразрушающих методов из-за простоты измерений. Он позволяет определять класс бетона, производить измерения под разными углами к поверхности, учитывать пластичность и упругость бетона.
Суть метода. Боёк со сферическим ударником под действием пружины ударяется о поверхность. Энергия удара расходуется на деформации бетона. В результате пластических деформаций образуется лунка, в результате упругих возникает реактивная сила. Электромеханический преобразователь превращает механическую энергию удара в электрический импульс. Результаты выдаются в единицах измерения прочности на сжатие.
К достоинствам метода относят оперативность, низкие трудозатраты, отсутствие сложных вычислений, слабую зависимость от состава бетона. Недостатком считается определение прочности в слое глубиной до 50 мм.
Метод упругого отскока
Метод упругого отскока заимствован из практики определения твёрдости металла. Для испытаний применяют склерометры – пружинные молотки со сферическими штампами. Система пружин допускает свободный отскок после удара. Шкала со стрелкой фиксирует путь ударника при отскоке. Прочность бетона определяют по градуировочным кривым, которые учитывают положение молотка, так как величина отскока зависит от его направления. Среднюю величину вычисляют по данным 5-10 измерений, выполненных на определённом участке. Расстояние между местами ударов – от 30 мм.
Диапазон измерений методом упругого отскока – 5-50 МПа. К достоинствам метода относят простоту и скорость измерений, возможность оценки прочности густоармированных конструкций. Ключевые недостатки такие же, как у других ударных методов: контроль прочности в поверхностном слое (глубина 20-30 мм), необходимость частых поверок (каждые 500 ударов), построение градуировочных зависимостей.
Ниже представлены измерители прочности бетона, работающие по принципу ударного импульса, из ассортимента нашей компании
![]() |
![]() |
![]() |
![]() |
Молоток Шмидта ORIGINAL SCHMIDT | Молоток Шмидта SILVER SCHMIDT | Молоток Шмидта Original Schmidt Live | Измерители прочности бетона ИПС-МГ4 |
Метод пластической деформации
Метод пластической деформации считается одним из самых дешёвых. Его суть – в определении твёрдости поверхности посредством измерения следа, который оставляет стальной шарик/стержень, встроенный в молоток. При проведении испытаний молоток располагают перпендикулярно поверхности бетона и совершают несколько ударов. С помощью углового масштаба измеряют отпечатки на бойке и бетоне. Для облегчения измерений диаметров используют листы копировальной или белой бумаги. Полученные характеристики фиксируют и вычисляют среднее значение. Бетонная прочность определяется по соотношению размеров отпечатков.
Принцип действия приборов для испытаний методом пластических деформаций основан на вдавливании штампа при помощи удара либо статического давления. Устройства статических давлений применяются ограниченно, более распространены приборы ударного действия – ручные и пружинные молотки, маятниковые устройства с шариковым/дисковым штампом. Твёрдость стали штампов минимум HRC60, диаметр шарика — минимум 10 мм, толщина диска — не меньше 1 мм. Энергия удара должна быть равна или больше 125 H.
Метод прост, может применяться в густоармированных конструкциях, отличается быстротой, но подходит для оценки прочности бетона не больше М500.
Ультразвуковое обследование
Ультразвуковой метод – это регистрация скорости прохождения ультразвуковых волн. По технике проведения испытаний можно выделить сквозное ультразвуковых прозвучивание, когда датчики располагают с разных сторон тестируемого образца, и поверхностное прозвучивание, когда датчики расположены с одной стороны. Сквозной метод позволяет, в отличие от всех остальных методов НК прочности, контролировать прочность в приповерхностных и глубоких слоях конструкции.
Ультразвуковые приборы неразрушающего контроля бетона могут использоваться не только для контроля прочности бетона, но и для дефектоскопии, контроля качества бетонирования, определения глубины и поиска арматуры в бетоне. Они позволяют многократно проводить массовые испытания изделий любой формы, вести непрерывный контроль нарастания или снижения прочности.
На зависимость «прочность бетона – скорость ультразвука» влияют количество и состав заполнителя, расход цемента, способ приготовления бетонной смеси, степень уплотнения бетона. Недостатком метода считается довольно большая погрешность при переходе от акустических характеристик к прочностным.
Ниже даны ссылки на приборы неразрушающего контроля бетона, представленные в ассортименте нашей компании
Кроме перечисленных способов контроля прочности существуют менее распространённые. На стадии экспериментального использования метод электрического потенциала, инфракрасные, вибрационные, акустические методы.
Опыт ведущих специалистов по неразрушающему контролю прочности бетона показывает, что в базовый комплект специалистов, занятых обследованием, должны входить приборы, основанные на разных методах контроля: отрыв со скалыванием (скалывание ребра), ударный импульс (упругий отскок, пластическая деформация), ультразвук, а также измерители защитного слоя и влажности бетона, оборудование для отбора образцов.
Погрешность методов неразрушающего контроля прочности бетона
№ | Наименование метода | Диапазон применения*, МПа | Погрешность измерения** |
1 | Пластическая деформация | 5 ... 50 | ± 30 ... 40% |
2 | Упругий отскок | 5 ... 50 | ± 50% |
3 | Ударный импульс | 10 ... 70 | ± 50% |
4 | Отрыв | 5 ... 60 | нет данных |
5 | Отрыв со скалыванием | 5 ... 100 | нет данных |
6 | Скалывание ребра | 10 ... 70 | нет данных |
7 | Ультразвуковой | 10 ... 40 | ± 30 ... 50% |
* по ГОСТ 17624 и ГОСТ 22690; ** источник: Джонс Р., Фэкэоару И. Неразрушающие методы испытаний бетонов. М., Стройиздат, 1974. 292 с. |
Процедура оценки
Общие правила контроля прочности бетона изложены в ГОСТ 18105-2010. Требования к контрольным участкам приведены в следующей таблице
Метод | Общее число измерений на участке | Минимальное расстояние между местами измерений на участке, мм | Минимальное расстояние от края конструкции до места измерения, мм | Минимальная толщина конструкции, мм |
Упругий отскок | 9 | 30 | 50 | 100 |
Ударный импульс | 10 | 15 | 50 | 50 |
Пластическая деформация | 5 | 30 | 50 | 70 |
Скалывание ребра | 2 | 200 | -0 | 170 |
Отрыв | 1 | 2 диаметра диска | 50 | 50 |
Отрыв со скалыванием при рабочей глубине заделки анкера: 40 мм < 40 мм |
1 2 |
5h |
150 |
2h |
Наиболее сложными для контроля бетонных конструкций являются случаи воздействия на них агрессивных факторов: химических (соли, кислоты, масла), термических (высокие температуры, замораживание в раннем возрасте, переменное замораживание и оттаивание), атмосферных (карбонизация поверхностного слоя). При обследовании необходимо визуально, простукиванием, либо смачиванием раствором фенолфталеина (случаи карбонизации бетона), выявить поверхностный слой с нарушенной структурой. Подготовка бетона таких конструкций для испытаний неразрушающими методами заключается в удалении поверхностного слоя на участке контроля и зачистке поверхности наждачным камнем. Прочность бетона в этих случаях необходимо определять преимущественно методами местных разрушений или путём отбора образцов. При использовании ударно-импульсных и ультразвуковых приборов шероховатость поверхности не должна превышать Ra 25.
Прочность бетона по маркам
Класс бетона (В) по прочности на сжатие | Ближайшая марка бетона (М) по прочности на сжатие | Средняя прочность бетона данного класса кгс/см² | Отклонения ближайшей марки бетона от средней прочности бетона этого класса,% |
В3,5 | М50 | 45,84 | +9,1 |
В5 | М75 | 65,48 | +14,5 |
В7,5 | М100 | 98,23 | +1,8 |
В10 | М150 | 130,97 | +14,5 |
В12,5 | М150 | 163,71 | -8,4 |
В15 | М200 | 196,45 | +1,8 |
В20 | М250 | 261,94 | -4,6 |
В22,5 | М300 | 294,68 | +1,8 |
В25 | М350 | 327,42 | +6,9 |
В27,5 | М350 | 360,16 | -2,8 |
В30 | М400 | 392,90 | +1,8 |
В35 | М450 | 458,39 | -1,8 |
В40 | М500 | 523,87 | -4,6 |
В45 | М600 | 589 | |
В50 | М650 | 655 | |
В55 | М700 | 720 | |
В60 | М800 | 786 |
Измерение защитного слоя и диаметра арматуры
Основная задача защитного слоя – обеспечить надежное сцепление бетона с арматурой на этапах монтажа и эксплуатации бетонной конструкции. Кроме того, он выполняет функцию защиты от перепадов температур, повышенной влажности, агрессивных химических реагентов. Толщина защитного слоя бетона диктуется условиями эксплуатации конструкции, видом и диаметром используемой арматуры.
При создании защитного слоя бетона руководствуются указаниями СНиП 2.03.04-84 и СП 52-101-2003. Контроль толщины защитного слоя проводится по ГОСТ 22904-93.
Для оперативного контроля качества армирования железобетонных конструкций и определения толщины защитного бетонного слоя используют приборы для поиска арматуры в бетоне - локаторы арматуры. Они работают по принципу импульсной магнитной индукции. Помимо измерения толщины защитного слоя, измеритель способен поиск арматуры в бетоне и определять наличие арматуры на определенном участке, фиксировать сечение, диаметр и другие параметры арматурных включений.
Оборудование для измерения толщины защитного слоя и оценки расположения арматуры
![]() |
![]() |
![]() |
![]() |
![]() |
![]() |
Локатор арматуры Profoscope | Локатор арматуры Profometer PM-600 | Локатор арматуры Proceq GPR Live | Анализатор коррозии Canin+ | Измеритель защитного слоя бетона ИПА-МГ4 | Прибор диагностики свай ПДС-МГ4 |
Неразрушающий контроль влажности
Влажность бетона оценивают по ГОСТ 12730.0-78: Бетоны. Общие требования к методам определения плотности, влажности, водопоглощения, пористости и водонепроницаемости. Некоторое количество влаги (в ячеистом бетоне до 30–35%) остаётся в стройматериалах в ходе производственного процесса (технологическая влага). В нормальных условиях содержание влаги в бетонных конструкциях в течение первого отопительного периода сокращается до 4-6% по весу.
Для получения полной картины целесообразно использовать несколько различных по физическому принципу методов оценки. Для измерения влажности бетона применяют влагомеры или измерители влажности. Принцип действия влагомера основан на зависимости диэлектрической проницаемости материала и содержания в нем влаги. Следует учитывать, что содержание влаги в бетоне отличается от ее содержания на поверхности. Методы измерения на поверхности дают результат для глубины до 20 мм и не всегда отражают реальное положение вещей.
Оборудование для измерения влажности и проницаемости бетона
![]() |
![]() |
![]() |
![]() |
Измеритель влажности бетона Hygropin | Тестер проницаемости бетона Torrent | Измеритель влажности бетона МГ4Б | Измеритель влажности бетона МГ4БМ |
Адгезия защитных и облицовочных покрытий
Адгезия измеряется при помощи прямых (с нарушением адгезионного контакта), неразрушающих (с измерением ультразвуковых или электоромагнитных волн) и косвенных (характеризующих адгезию лишь в сопоставимых условиях) методов. Наиболее распространен метод оценки с помощью адгезиметра. Методика оценки установлена ГОСТ 28574-2014: Защита от коррозии в строительстве. Конструкции бетонные и железобетонные. Методы испытаний адгезии защитных покрытий.
Оценка бетона с помощью адгезиметра проводится при диагностике повреждений покрытия, контроле качества антикоррозийных работ, а также при проверке качества строительных материалов. Интенсивность адгезии определяется давлением отрыва, которое следует приложить к покрытию (штукатурке, краске, герметику и т.д.), чтобы отделить его от бетонной основы.
Оборудование для измерения адгезии
![]() |
![]() |
Измеритель адгезии DY-2 | Измеритель адгезии ПСО-ХМГ4 |
Морозостойкость
В большинстве нормативных документов устойчивость покрытий и изделий из застывшей смеси определяется количеством переходов через нулевую отметку, после которого начинается падение эксплуатационных характеристик. Морозостойкость бетона – способность выдерживать температурные перепады, а также количество циклов заморозки и оттаивания бетонной смеси. В ГОСТ 10060-2012 выделяют 11 марок бетона с различной морозостойкостью, которая имеет градацию на циклы от F50 до F1000.
Группы бетонов по морозостойкости
Группа морозостойкости | Обозначение | Примечание |
Низкая | менее F50 | Не находит широкого использования |
Умеренная | F50 – F150 | Морозостойкость и водонепроницаемость бетона этой группы имеет оптимальные показатели. Такие смеси встречаются наиболее часто. |
Повышенная | F150 – F300 | Морозостойкость бетонной смеси в этом диапазоне дает возможность эксплуатировать здания в достаточно суровых условиях. |
Высокая | F300 – F500 | Такие растворы требуются в особых случаях, например, при эксплуатации с переменным уровнем влаги. |
Особо высокая | более F500 | Бетон морозостойкий получается впрыскиванием особых добавок. Применяется при сооружении конструкций на века. |
Дополнительная информация
- Методы неразрушающего контроля прочности бетона
- Определение прочности бетона с использованием молотка Шмидта (по DIN EN 12504-2: 2001-12)
- Определение прочности бетона на отрыв адгезии нанесённых на бетон покрытий
- Трещины в бетоне (по DIN 1045-1: 2008). Наблюдение за трещиной и определение ширины раскрытия трещины в бетоне
- Способы измерения твёрдости металла, резины, бетона
Морозостойкость бетона оценивают ультразвуковыми методами по ГОСТ 26134-2016. Ультразвуковая диагностика отличается невысокой стоимостью, даёт возможность проводить обследования неограниченное число раз. При этом предъявляются высокие требования к качеству бетонной поверхности и квалификации сотрудника.
Подробную консультацию по контролю бетонных сооружений вы можете получить у наших специалистов по телефонам +7 (495) 972-88-55, +7 (495) 660-49-68.
Смотрите так же разделы: Дефектоскопы для бетона, Услуги по неразрушающему контролю бетона, Определение прочности бетона, Приборы для поиска арматуры, Обучение и аттестация специалистов по УЗК.
Оборудование для неразрушающего контроля бетона можно купить с доставкой до двери либо до терминалов транспортной компании в городах: Москва, Санкт-Петербург, Екатеринбург, Саратов. Амурск, Ангарск, Архангельск, Астрахань, Барнаул, Белгород, Бийск, Брянск, Воронеж, Великий Новгород, Владивосток, Владикавказ, Владимир, Волгоград, Волгодонск, Вологда, Иваново, Ижевск, Йошкар-Ола, Казань, Калининград, Калуга, Кемерово, Киров, Кострома, Краснодар, Красноярск, Курск, Липецк, Магадан, Магнитогорск, Мурманск, Муром, Набережные Челны, Нальчик, Новокузнецк, Нарьян-Мар, Новороссийск, Новосибирск, Нефтекамск, Нефтеюганск, Новочеркасск, Нижнекамск, Норильск, Нижний Новгород, Обнинск, Омск, Орёл, Оренбург, Оха, Пенза, Пермь, Петрозаводск, Петропавловск-Камчатский, Псков, Ржев, Ростов, Рязань, Самара, Саранск, Смоленск, Сочи, Сыктывкар, Таганрог, Тамбов, Тверь, Тобольск, Тольятти, Томск, Тула, Тюмень, Ульяновск, Уфа, Ханты-Мансийск, Чебоксары, Челябинск, Череповец, Элиста, Ярославль и другие города. А так же Республики Казахстан, Белоруссия и другие страны СНГ.
Способы измерения твёрдости металла, резины, бетона
Первоисточник статьи - https://vostok-7.ru/articles/tverdost/
Единого общепринятого определения термина «ТВЁРДОСТЬ» не существует поскольку методы определения этой метрологической величины настолько разнообразны, что нет возможности их объединить в одной фразе или описании. При этом даже для одного типа материала (напр. металлов) методов определения твердости существует более 5… Также именно по этой причине приборы для измерения твёрдости именуются не только твердомерами, но и другими названиями, указывающими на метод или материал измерения: дюрометр (для резин), склерометр (для минералов) и т.д.
Лаборатория НТЦ «Эксперт» оказывает услуги по измерению твердости различных деталей. Лаборатория укомплектована твердомерами различных типов и имеет аттестованных специалистов II уровня. По результатам измерений выдается заключение лаборатории неразрушающего контроля или заключение метрологической службы по выбору заказчика. Мы работаем с юридическими и физическими лицами. Проведение работ возможно как лабораторно, так и с выездом.
Твёрдость минералов
Шкала твёрдости минералов Мооса (склерометры царапающие) – метод определения твёрдости минералов путём царапания одного минерала другим минералом для сравнительной диагностики твёрдости минералов между собой по системе мягче-твёрже. Испытываемый минерал либо не царапается другим минералом (эталоном Мооса или склерометром) и тогда его твёрдость по Моосу выше, либо царапается - и тогда его твёрдость по Моосу ниже.
Типы исследуемых материалов:
- минералы (природные и искусственные), в т.ч. измеряется твёрдость камней горных пород
- бетон и другие строительные материалы: твёрдость искусственных камней, плитки, стекла и др.
Молотки Шмидта (склерометры-молотки) – метод определения твёрдости и прочности на сжатие без разрушения строительный материалов: бетона, кирпичей, строительного раствора и пр. Оценка материалов происходит по предварительно установленной градуировочной зависимости между прочностью эталонных образцов и значением отскока бойка молотка Шмидта от поверхности материала.
Типы исследуемых материалов:
- бетон
- кирпич
- строительный раствор
- природные камни и горные породы
Твёрдость металлов
Твёрдость металлов – наиболее глубоко изученное и стандартизированное международной практикой измерение твёрдости. Наиболее распространены следующие методы:
Измерение твёрдости металлов по Бринеллю (твердомеры)
Один из старейших методов, твёрдость определяется по диаметру отпечатка, оставляемому металлическим шариком, вдавливаемым в поверхность. Обозначается HB, где H — Hardness (твёрдость, англ.), B — Brinell (Бринелль, англ.)
Измерение твёрдости металлов по Роквеллу (твердомеры)
Это самый распространённый из методов начала XX века, твёрдость определяется по относительной глубине вдавливания металлического шарика или алмазного конуса в поверхность тестируемого материала. Обозначается HR, где H — Hardness (твёрдость, англ.), R — Rockwell (Роквелл, англ.), а 3-й буквой идёт обозначение типа шкалы, напр. HRA, HRB, HRC и т.д.
Измерение твёрдости металлов по Виккерсу (твердомеры и микротвердомеры)
Самая широкая по охвату шкала, твёрдость определяется по площади отпечатка, оставляемого четырёхгранной алмазной пирамидкой, вдавливаемой в поверхность. Обозначается HV, где H — Hardness (твёрдость, англ.), V — Vickers (Виккерс, англ.).
Измерение твёрдости металлов по Шору (твердомеры и склероскопы)
Данный метод крайне редко используется, твёрдость определяется по высоте отскока бойка от поверхности. Обозначается HS, где H — Hardness (твёрдость, англ.), S — Shore (Шор, англ.), а 3-й буквой идёт обозначение типа шкалы, напр. HSD
Измерение твёрдости металлов по Либу (твердомеры)
Это самый широко применяемый на сегодня метод в мире, твёрдость определяется как отношение скоростей до и после отскока бойка от поверхности. Обозначается HL, где H — Hardness (твёрдость, англ.), L — Leeb (Либ, англ.), а 3-й буквой идёт обозначение типа датчика, напр. HLD, HLC и т.д.
Твёрдость резины
Определить твердость резины сегодня можно несколькими методами:
Измерение твёрдости резины по Шору (твердомеры и дюрометры)
Самый широко применяемый на сегодня метод в мире, твёрдость резины определяется по глубине проникновения в материал специальной закаленной стальной иглы (индентора) под действием калиброванной пружины. Твёрдость резины обозначается в международной практике как H, где H — Hardness (твёрдость, англ.), а 2-й буквой идёт обозначение типа шкалы, напр. HA, HB, HC, HD и т.д., в практике России пишется как «твёрдость по Шору тип А» или «твёрдость по Шору тип D».
Измерение твёрдости по Аскеру (твердомеры и дюрометры)
Это национальный японский метод, сходный с методом измерения твёрдости резины по Шору, но отличающийся от него типом инденторов, пружин и пр. Твёрдость резины обозначается в международной практике как Asker (Аскер, англ.), а далее идёт обозначение типа шкалы, напр. Asker С, Asker D и т.д. В России не применяется.
Измерение твёрдости по Роквеллу (твердомеры)
В этом случае используется стандартный твердомер Роквелла для измерения твёрдости металлов, но вместо индентора-конуса используются инденторы со стальными шариками. Твёрдость резины обозначается HR, где H — Hardness (твёрдость, англ.), R — Rockwell (Роквелл, англ.), а 3-й буквой идёт обозначение типа шкалы, напр. HRP, HRL, HRM или HRE.