Статьи по неразрушающему контролю
Сравнение характеристик малогабаритных твердомеров
Струтынский А.В., Худяков С.А.
Первоисточник статьи - https://vostok-7.ru/articles/3/
В практике судоремонта нередко возникает необходимость измерения твердости рабочих поверхностей деталей. Зачастую применение классических методов – Бринелля [1], Роквелла [2], Виккерса [3] оказывается невозможным, либо неоправданно трудоемким и непроизводительным. К таким случаям можно отнести контроль твердости крупногабаритных деталей, измерение без полной разборки узлов и в труднодоступных местах. Эти задачи могут быть решены при помощи малогабаритных твердомеров. Применение этих приборов имеет ряд особенностей и ограничений, которые необходимо учитывать. В таких приборах используется метод ультразвукового контактного импеданса (UCI - Ultrasonic Contact Impedance) и метод упругого отскока (динамический). Рассмотрим каждый из них с учетом преимуществ и недостатков.
1. Метод ультразвукового контактного импеданса
Суть метода заключается в следующем: при калиброванной нагрузке алмазная пирамидка, закрепленная на металлическом стержне, колеблющемся на резонансной частоте, внедряется в материал изделия. Частота колебаний стержня пропорциональна площади отпечатка на объекте контроля, то есть твердости материала. Метод несколько напоминает метод Виккерса [3], только площадь отпечатка оценивается без снятия нагрузки, то есть, совместно с упругой составляющей деформации. Поскольку фиксация датчика на объекте осуществляется рукой, величина рабочей нагрузки небольшая – около 10Н. При такой нагрузке и, соответственно, таком размере отпечатка метод занимает промежуточное положение между методом Виккерса [3] и методом микротвердости [4] по локальности воздействия на объект. Метод позволяет измерять твердость при любом пространственном положении датчика.
2. Метод упругого отскока
Методом упругого отскока определяется значение твердости HL по Либу (в некоторых переводах - Лейбу). Эта величина, введенная в практику измерений в 1978 г., является частным величины скорости отскока ударника к величине скорости удара, умноженным на 1000. В более твердых материалах возникает большая скорость отскока, чем в тех, у которых твердость меньше. Применительно к определенной группе материалов (например, сталь, алюминий и др.), значение HL совпадает со значением твердости, поэтому оно непосредственно и используется.
В ходе проведения испытания ударник с наконечником из твердого сплава приводится в действие пружиной, ударяется о поверхность и отскакивает. Скорости удара и отскока измеряются следующим образом: постоянный магнит, встроенный в тело ударника, проходит через катушку и в процессе своего поступательного и возвратного движения создает электрический ток. Величины возникающих при этом токов пропорциональны скоростям удара и отскока; результаты обрабатываются и представляются на дисплее индикаторного блока в виде значения твердости.
Для наиболее часто встречающихся материалов разработаны специальные кривые, позволяющие сравнивать полученные значения со стандартными статистическими (по Бринеллю, Роквеллу) и переводить их в эти системы. Метод напоминает метод Шора, только определяется не высота отскока ударника, а отношение величины скорости отскока ударника к величине скорости удара. С использованием поправок, метод позволяет измерять твердость при любом пространственном положении датчика (в отличие от метода Шора).
Следует понимать, что сопоставление величины твердости, приведенное, например, в [5], измеренной различными методами и даже одним методом, но с разными параметрами (величина, продолжительность и скорость нагружения, форма, размеры и материал индентора) не является строгим, точным и универсальным. Еще менее точной является оценка прочности сталей (временного сопротивления) по величине твердости. При подобном сопоставлении кроме [6], использующего пересчет по эмпирическому соотношению, близкому к σв = 9,8·0,35·НВ (МПа) [7], используются и другие зависимости. Например, используемая в теплоэнергетике формула σв = 9,8·(0,46·НВ – 22) лучше подходит для низкоуглеродистых сталей с твердостью до 200 НВ (см. рис.1).
Эти формулы не единственные и не претендуют на универсальность и точность. В случае измерения твердости переносным прибором происходит двойное сопоставление. Сначала динамическая твердость пересчитывается в НВ, затем во временное сопротивление. При таком "пересчете" перемножаются и коэффициенты корреляции, которые и так существенно меньше 1. Оценка пластических характеристик по твердости (относительного удлинения и сужения, ударной вязкости) обычно не проводится, так как между этими величинами нет корреляционной связи.
2.1. Сравнение основных характеристик датчиков малогабаритных твердомеров
Основные характеристики твердомеров определяют, прежде всего, характеристики датчиков. Наличие развитых сервисных функций только повышает удобство пользования прибором, что немаловажно при большом объеме измерений.
Для сравнения были выбраны датчики отечественных динамических твердомеров МЕТ-УД, ТЭМП-3 и ТДМ-2. Ультразвуковой датчик твердомера МЕТ-УД сравнивался с датчиком твердомера MICRODUR фирмы Крауткремер (рис.2).
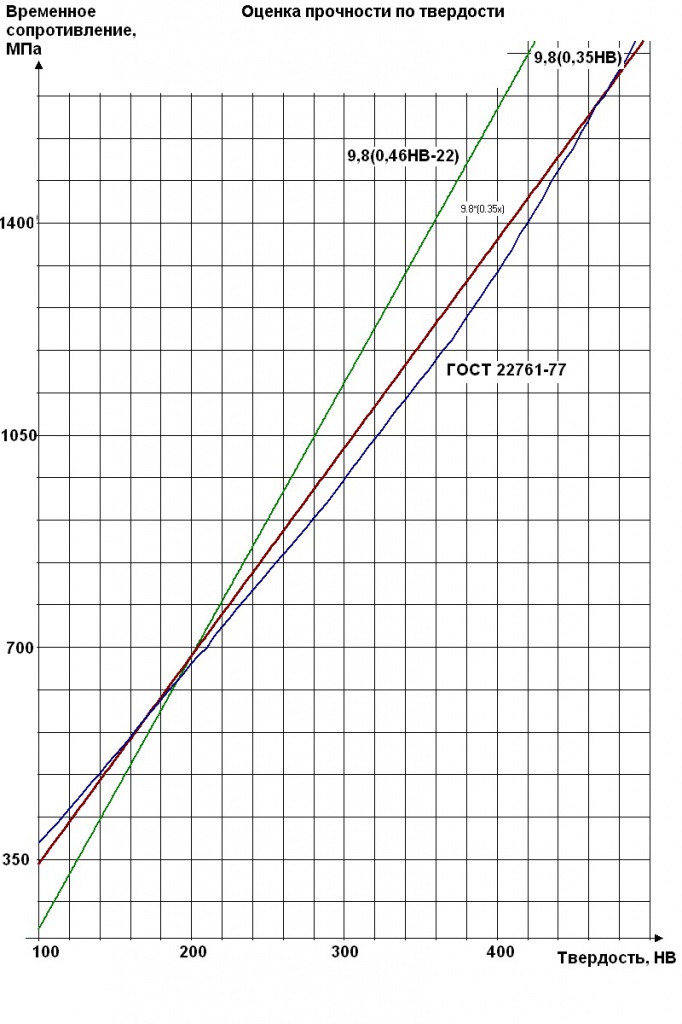
Рис. 1 Сопоставление твердости и прочности по разным методикам.
Сравнение датчика МЕТ с датчиком к прибору MICRODUR производства КРАУТКРЕМЕР не в пользу МЕТ. В датчике "MICRODUR" применен электрический привод нагружения, обеспечивающий стабильную скорость и время нагружения и значительно уменьшающий случайную составляющую погрешности измерения, в том числе, субъективный человеческий фактор. Датчик МЕТ-УД упрощенный. Такое упрощение требует от оператора хороших навыков, тщательности и аккуратности и приводит к повышенной случайной погрешности измерения.
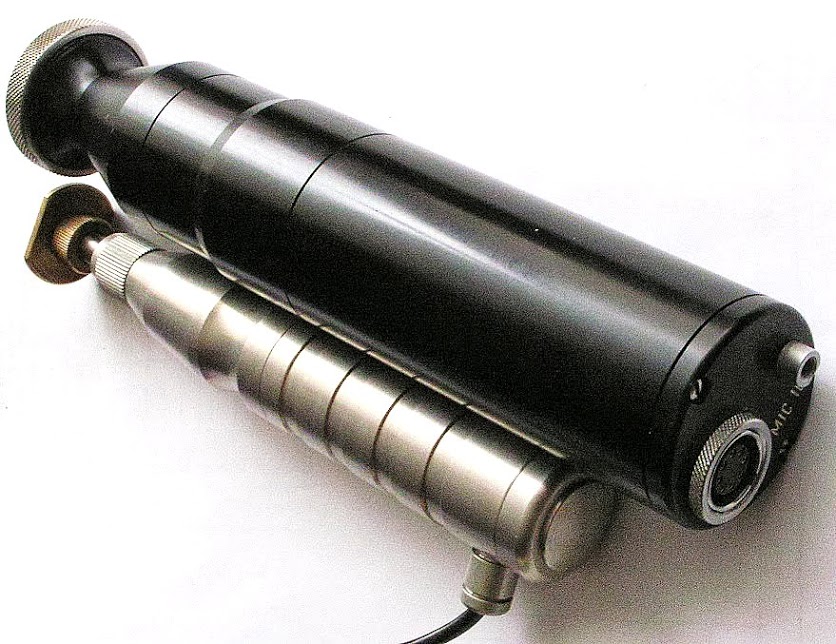
а) МЕТ-УД; б) MICRODUR
Рис.2. Внешний вид ультразвуковых датчиков.
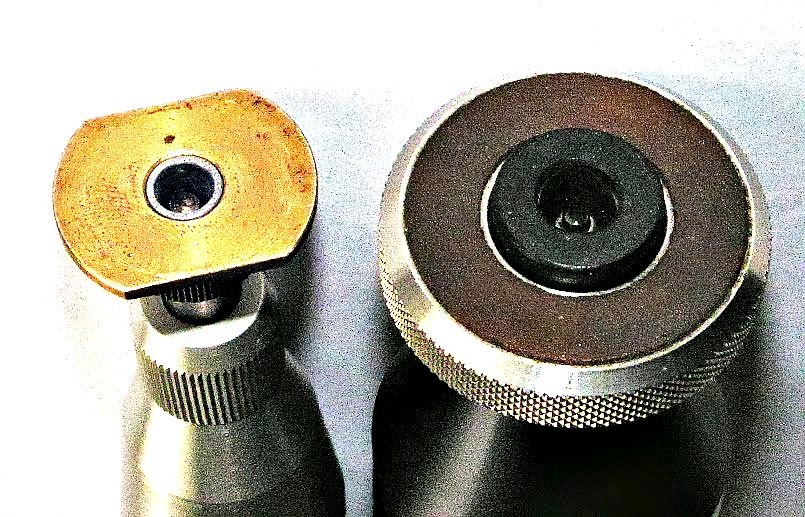
а) МЕТ-УД; б) MICRODUR
Рис.3. Поверхность базирования ультразвуковых датчиков.
Поверхность базирования датчика MICRODUR выполнена с эластичным нескользящим кольцом, обеспечивающим лучшую фиксацию датчика на объекте (рис.3).
Оба датчика оставляют отпечатки примерно одинакового размера (около 0,1 мм на стали с твердостью 150 НВ), то есть, имеют примерно одинаковые рабочие нагрузки.
В названии немецкого прибора присутствует слово "микро", напоминающее, что нагрузка и размер отпечатка приближаются к способу микротвердости [4], значительно ограничивая область применения "вслепую", без оценки микроструктуры и точности позиционирования на объекте. Производитель МЕТ-УД ограничивает только измерение твердости чугуна и, в качестве преимущества метода, указывает возможность использования этого датчика (метода) для тонкостенных конструкций (в том числе трубопроводов). Для термически упрочненных объектов с априори мелкозернистой, однородной микроструктурой (мартенсит, бейнит) проблем не предвидится, а даже для феррито-перлитной структуры возможны ограничения применения. Рассмотрим углеродистую сталь (0,1-0,2 % углерода характерно для сварных конструкций). По правилам (законам) Н. С. Курнакова известно, что твердость феррита составляет около 100 НВ, перлита -200 НВ. Твердость феррито-перлитной структуры линейно увеличивается от 100 до 200НВ пропорционально доле перлита в микроструктуре. При заявленной погрешности ± 10 НВ необходимо иметь чувствительность не менее 5 НВ, что соответствует 5 % изменению доли перлитной составляющей. То есть, минимальное количество зерен в отпечатке (при равномерном распределении структурных составляющих и одинаковой деформации под воздействием индентора) – 20. Учитывая пирамидальную форму отпечатка и, соответственно, неоднородность деформации на площади отпечатка, удвоим это число (а можно и утроить). Как указывалось выше, размер отпечатка - 0,1 мм на стали с твердостью 150 НВ, то есть, площадь – 0,01 мм2, это соответствует 4000 зерен на мм2. В [8], таблица 1, среднему значению 4096 зерен на мм2 соответствует зерно №9. То есть, метод с заявленной погрешностью работает на конструкционной стали с зерном более мелким, чем №9 (№10–14). Зерно № 7 – 8 – не редкость в стальном прокате, еще хуже может быть ситуация с поковками и отливками, где и размер зерна и неоднородность структуры значительно выше. На лицо явное недокументированное ограничение применимости метода.
2.2. Сравнение динамических датчиков
Российские производители не приводят основных характеристик датчиков, поэтому необходимо снять их самостоятельно. Для этого надо измерить диаметры шариков, массы ударников и их среднюю скорость. Для приближенного определения средней скорости необходимо записать электрические сигналы датчиков и проанализировать их.
2.2.1 Сравнение диаметров шариков
Различие диаметров шариков представлено на рис. 4
МЕТ, ТЭМП ТДМ
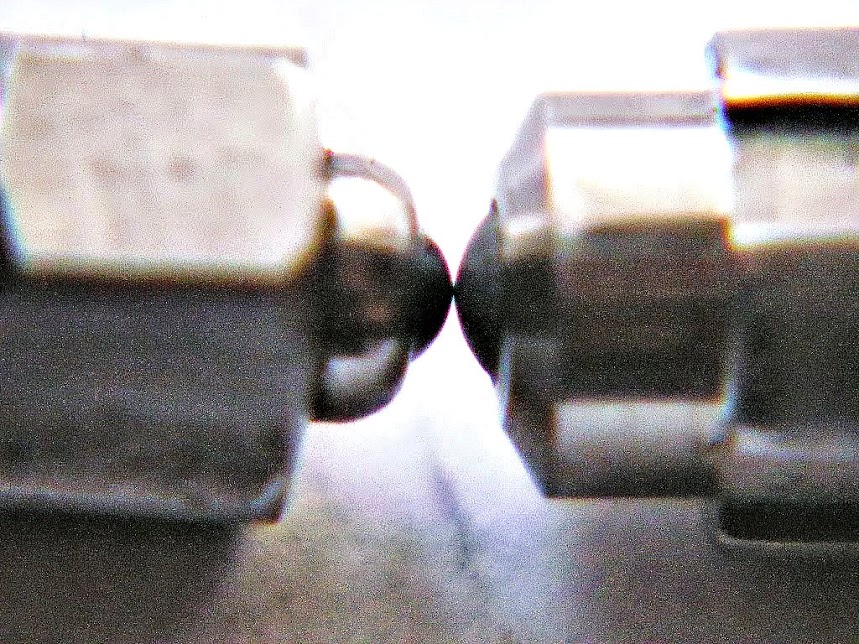
Рис. 4. Сравнение диаметров шариков
Отношение диаметров шариков составляет
DМЕТ, ТЭМП/DТДМ ≈ 0,67.
Диаметры шариков датчиков твердомеров МЕТ-УД и ТЭМП-3 составляют 2,0 мм, твердомера ТДМ-2 – 3,0 мм.
2.2.2. Сигналы датчиков
Сигналы датчиков снимались при помощи компьютерного осциллографа. Датчики устанавливались на массивную стальную плиту твердостью 150 НВ.
Осциллограммы представлены на рис. 5-7.
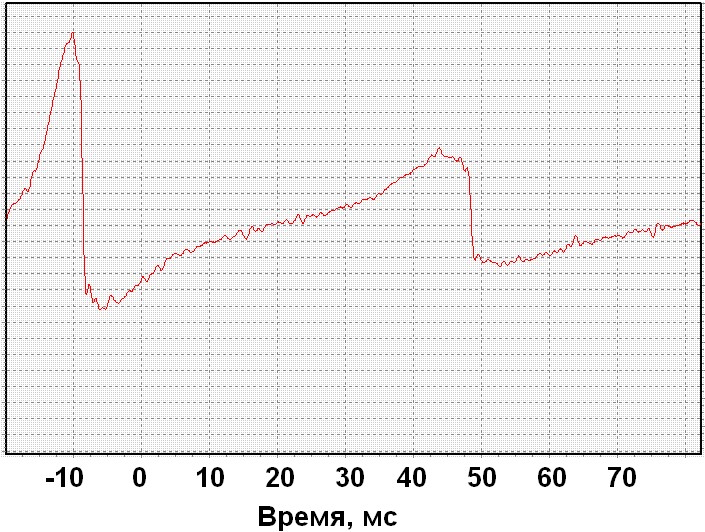
Рис. 5. Сигнал датчика твердомера МЕТ-УД.
Интервал времени между импульсами – τ = 58 мс
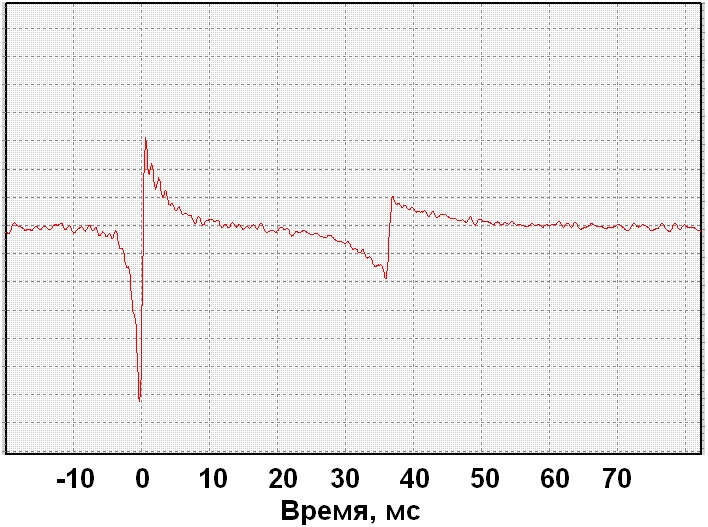
Рис. 6. Сигнал датчика твердомера ТДМ-2.
Интервал времени между импульсами – τ = 37 мс
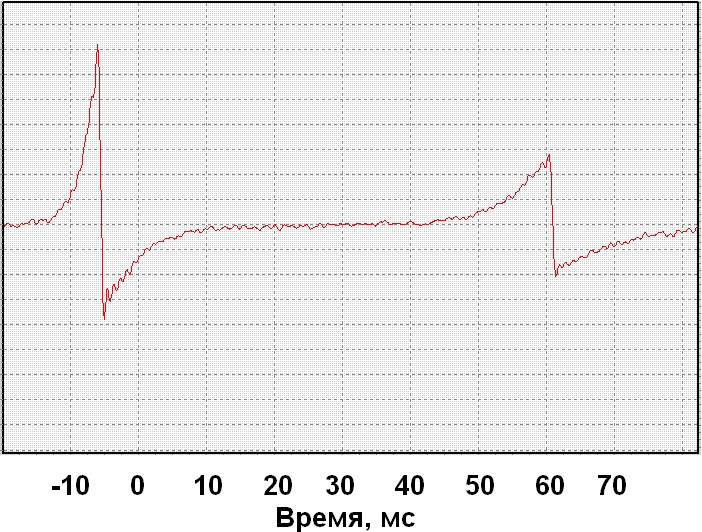
Рис. 7. Сигнал датчика твердомера ТЭМП-3.
Интервал времени между импульсами – τ = 69 мс
Сглаженный пик импульса отскока датчика МЕТ может вызывать дополнительную нестабильность показаний. Разная полярность и амплитуда – конструктивная особенность, учитываемая электронными блоками твердомеров.
2.2.3. Сравнение энергии удара (упрощенно)
Анализ сигналов позволяет определить время пролета ударника от середины катушки до поверхности объекта контроля и отскока до середины катушки. Приняв, что положение середины катушки соответствует свободному ходу ударника, среднюю скорость ударника определим по формуле:
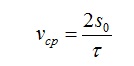
Энергию удара можно определить по формуле для кинетической энергии
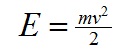
Скорость в момент удара v максимальна и составляет с учетом расходования энергии на пластическую деформацию около 4·vср то есть,
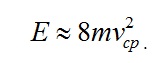
Такое упрощение не позволяет точно рассчитать энергию удара, но, с учетом того, что измерения проводились на одном образце, отношение энергий различных датчиков определяется корректно.
Результаты измерений и расчетов приведены в таблице 1.
Таблица 1. Основные характеристики датчиков твердомеров
Характеристики | МЕТ-УД | ТЭМП-3 | ТДМ-2 |
Диаметр шарика, D, мм | 2,0 | 2,0 | 3,0 |
Масса ударника, m, г | 7,0 | 8,2 | 5,5 |
Полный ход ударника, S, мм | 20 | 30 | 30 |
Свободный ход ударника, S0, мм | 8 | 15 | 12 |
Время между импульсами, τ, мс | 58 | 69 | 37 |
Средняя скорость ударника, v, м/с | 0,28 | 0,43 | 0,69 |
Энергия удара, E, мДж | 4,4 | 12,1 | 20,9 |
Энергию удара можно также оценить по характеристикам пружин:
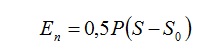
Потенциальная энергия ударника составляет:
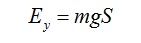
Полная энергия:
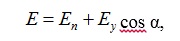
где α – угол между осью датчика и нормалью к поверхности Земли.
Отношение Еу/Еп определяет величину поправки на изменение пространственного положения датчика.
Результаты измерений и расчетов приведены в таблице 2.
Таблица 2. Основные характеристики пружин датчиков твердомеров
Характеристики | МЕТ-УД | ТЭМП-3 | ТДМ-2 |
Усилие взведенной пружины, Р, Н | 1,7 | 3,1 | 4,5 |
Полный ход ударника, S, мм | 20 | 30 | 30 |
Свободный ход ударника, S0, мм | 8 | 15 | 12 |
Потенц. энергия пружины, Eп, мДж | 10,2 | 23,25 | 40,5 |
Потенц. энергия ударника, Eу, мДж | 1,40 | 2,46 | 1,65 |
Eу / Eп | 0,137 | 0,105 | 0,041 |
Как видно из приведенных результатов, энергия удара датчиков твердомеров отличается более чем в 4 раза, причем производители твердомеров не приводят этой характеристики в паспортах и технических описаниях приборов. Это, вероятно, следствие отсутствия стандарта на метод. Если обратиться к [1], то обнаружится что результаты измерений твердости по Бринеллю при различных условиях испытаний записываются с соответствующими дополнениями (диаметр шарика, нагрузка, время). Те же данные приводятся и на мерах твердости, а в этом косвенном методе такие большие вольности, которые могут привести к различным результатам измерений на реальных объектах при одинаковых показаниях на мерах твердости.
2.2.4. Анализ граничных условий применимости
Понятно, что датчики с различной энергией удара должны иметь разные, обоснованные границы применимости. Паспортные границы применимости приведены в табл. 3.
Таблица 3. Паспортные границы применимости твердомеров
Характеристики | МЕТ-УД | ТЭМП-3 | ТДМ-2 |
Шероховатость поверхности, Ra, мкм | 3,2 | 2,5 | 2,5 |
Минимальный радиус кривизны, мм | 10 | 15 | 15 |
Минимальная масса объекта контроля, кг | 3 | 1,5 | 3 |
Минимальная толщина объекта контроля, мм | 12 | 6 | 10 |
Поправка на положение датчика | нет | есть | есть |
Логично предположить, что датчик с минимальной энергией удара (МЕТ-УД) должен иметь меньшие пределы по минимальной массе и толщине объекта контроля. Возможно, искусственное увеличение этих границ является маркетинговым ходом, цель которого – привлечение внимания к универсальному твердомеру, использующему два метода измерения твердости. Отсутствие поправки на пространственное положение датчика вызывает недоумение, так как влияние изменения пространственного положения для этого датчика максимально. Шероховатость поверхности Ra 3,2 мкм также не объяснима: при измерении твердости по Бринеллю [1] при значительно больших нагрузках требует подготовки поверхности с шероховатостью не более Ra 2,5 мкм. Чувствительность к наклепу при подготовке поверхности у датчика МЕТ-УД самая высокая, что необходимо учитывать при работе с этим прибором.
Выводы
1. Малогабаритные твердомеры, удобные и незаменимые при решении ряда задач измерения твердости, имеют ряд недокументированных ограничений и особенностей применения.
2. Энергия удара датчиков трех отечественных динамических твердомеров отличается более чем в 4 раза, причем, производители твердомеров не приводят этой характеристики в паспортах и технических описаниях приборов. Это, вероятно, следствие отсутствия стандарта на метод.
3. Динамические датчики с высокой энергией удара (ТДМ-2) имеют некоторое преимущество при контроле конструкционных сталей и сварных соединений. Применение датчиков с низкой энергией удара целесообразно для более тонкостенных и легких объектов, тонких слоев, либо когда нежелательны большие отпечатки на объекте. В других случаях применение датчиков с низкой энергией удара может привести к необходимости увеличения числа замеров для усреднения результатов и излишней чувствительности к наклепу поверхностного слоя, возможному при подготовке поверхности и к изменению пространственного положения.
4. При обнаружении нехарактерных значений твердости отдельных точек необходимо проводить дополнительные измерения вблизи (3… 5 мм) от выпавшей точки, так как причиной может быть не только промах при измерении, но и неоднородности объекта контроля.
5. Диаметр отпечатка от динамических датчиков на стали с твердостью 150 НВ составляет около 0,50 мм для твердомера МЕТ-УД и 0,82 мм для ТДМ-2. Учитывая малую площадь контакта с объектом, при значительной структурной и химической неоднородности объектов контроля (поковки, отливки), превышающей или сравнимой с размером отпечатка, необходимо использовать приборы с большим диаметром шарика и, соответственно, большей энергией удара. Более простое и эффективное решение при единичных измерениях – использование метода Польди [9].
6. Существует диапазон толщины и микроструктуры, в котором использование датчиков с рассмотренными параметрами не обеспечивает корректного подхода к измерению твердости: конструкция имеет недостаточную жесткость для применения динамического датчика, а малая нагрузка импедансного датчика определяет излишнюю локальность зоны воздействия.
7. Для широкого спектра задач контроля твердости целесообразно иметь малогабаритный твердомер не только поддерживающий импедансный и динамический методы. Желательно еще иметь набор датчиков с разными характеристиками – энергией удара и диаметром шарика для динамического датчика и рабочей нагрузкой для импедансного датчика.
8. В случае возникновения разногласий при измерении твердости малогабаритными твердомерами, необходимо сравнивать характеристики датчиков, а в качестве арбитражных методов использовать классические методы измерения твердости.
Литература
1. ГОСТ 9012 – 59 Металлы и сплавы. Методы определения твердости по Бринеллю.
2. ГОСТ 9013 – 59 Металлы и сплавы. Методы определения твердости по Роквеллу.
3. ГОСТ 2999 – 75 Металлы и сплавы. Методы определения твердости по Виккерсу.
4. ГОСТ 4950 – 76 Измерение микротвердости вдавливанием алмазных наконечников.
5. ОСТ5. 9287 – 78 Детали стальные изделий судового машиностроения и приборостроения, термически обработанные. Технические требования, правила приемки и методы испытаний.
6. ГОСТ 22761 – 77 Металлы и сплавы. Методы определения твердости по Бринеллю переносными твердомерами статического действия.
7. Испытание материалов. Справочник под ред. Х. Блюменауэра пер. с нем. 1979., 448 с. М. «Металлургия»
8. ГОСТ 5639 – 82 Стали и сплавы. Метод выявления и определения величины зерна.
9. ГОСТ18661 – 73 Сталь. Измерение твердости методом ударного отпечатка.
10. В. С. Золотаревский. Механические свойства металлов. 1983., 350 с. М. «Металлургия»
Рекомендации по выбору дозиметра
В данном перечне содержатся ссылки на модели дозиметров, которые в большинстве случаев удовлетворяют требованиям перечисленных отраслей.
1 группа – лаборатории неразрушающего контроля, использующие импульсные рентгеновские аппараты - ДКС АТ-1123, ДКС-96.
2 группа – медицинские учреждения: приборы на гамма-рентген излучения для контроля установок, индивидуальный контроль персонала; (ДКС-АТ1123, ДКР-АТ1103М, ДКС-АТ3509)
3 группа – строительные организации: контроль территорий под застройку (поисковые приборы Дозы, ДКГ-03Д Грач, ДКГ-07Д Дрозд, ДКГ-02У Арбитр, ДКС-96)
4 группа – предприятия, занимающиеся сбором и отгрузкой металлолома: (приборы поисковые на гамма излучение ИСП-РМ1401МА, ИСП-РМ1701М, ДКГ-РМ1703МО-1/2)
5 группа – атомные структуры: контроль территорий АЭС, индивидуальный контроль персонала (МКС-АТ1117М, ДКС-96, ДКС-АТ3509, ДКГ-РМ1610, РМ1603А/В)
6 группа – банковские структуры: контроль загрязненности денежных знаков (МКС-РМ1405, МКС-151)
7 группа – частные лица (СИГ-РМ1208М, РМ1904 - для айфонов)
8 группа - военные ведомства, силовые структуры: поисковые приборы и индивидуальные дозиметры (МКС-РМ1402М, ДКГ-РМ1603А/В )
Источники излучения для промышленного радиационного контроля можно условно разделить на рентгеновские аппараты и гамма-дефектоскопы, использующие в качестве источника излучения радионуклид вместо рентгеновской трубки. Каждый тип имеет свои достоинства и недостатки и более применим в конкретной области НК. Рентгеновские аппараты в общем виде можно классифицировать на аппараты постоянного и действия и импульсные. Импульсные рентгеновские аппараты как правило дешевле, легче и проще в управлении. Аппараты с постоянным напряжением дороже, но при этом долговечней и обеспечивают лучшее качество снимков.
Основным документом, регулирующим правила аттестации и основные требования к лабораториям неразрушающего контроля, является СДАНК-01-2020, в соответствии с положениями данного норматива выделяются общие и специальные требования к лабораториям НК, а так же требования к оборудованию и специалистам лаборатории.
II. Статус, административная подчиненность и структура ЛНК
2.1. ЛНК может быть юридическим лицом или подразделением юридического лица, которые несут юридическую ответственность за ее деятельность. ЛНК может быть организована физическим лицом (индивидуальным предпринимателем), осуществляющим свою деятельность в установленном законодательством порядке.
2.2. Деятельность ЛНК структурируется и управляется таким образом, чтобы обеспечивалась беспристрастность.
2.3. Статус, административная подчиненность и структура ЛНК обеспечивают объективность результатов контроля, исключают возможность любого воздействия на сотрудников лаборатории с целью оказать влияние на результаты контроля.
2.4. ЛНК несет ответственность за беспристрастность своей деятельности и не допускает коммерческое, финансовое или иное давление, ставящее беспристрастность под угрозу:
2.4.1. ЛНК, имеющая статус юридического лица или индивидуального предпринимателя, удовлетворяет следующим критериям беспристрастности:
- независима от сторон, заинтересованных в результатах НК;
- не участвует в разработке, изготовлении, строительстве, монтаже, ремонте, реконструкции и эксплуатации или не является покупателем, собственником, потребителем объектов, НК которых осуществляет.
2.4.2. ЛНК, являющаяся структурным подразделением юридического лица или индивидуального предпринимателя, удовлетворяет следующим критериям беспристрастности:
- в рамках организационной структуры четко разграничены функциональные обязанности по осуществлению НК, а также установлена отчетность лаборатории перед руководством юридического лица или индивидуального предпринимателя, структурным подразделением которых она является;
- персонал ЛНК не участвует в разработке, изготовлении, строительстве, монтаже, ремонте, реконструкции и эксплуатации объектов, НК которых осуществляет;
- лаборатория не выполняет работы, которые могут повлиять на объективность результатов НК.
2.5. ЛНК идентифицирует и минимизирует риски для своей беспристрастности на постоянной основе. Это включает риски, которые возникают в процессе ее деятельности, в результате ее отношений или отношений ее персонала.
Примечание. Отношения, которые угрожают беспристрастности ЛНК, могут основываться на праве собственности, управлении, руководстве, персонале, финансах, договорах, маркетинге или на других видах стимулирования в отношении заказчиков и т.п.
III. Помещения и специальные требования для НК
3.1. Помещения ЛНК (размещение персонала, места проведения НК, архив и фонд НТД, хранение и эксплуатация технических средств) по производственной площади, характеру и объему выполняемых работ и окружающая среда при проведении контроля вне помещения должны соответствовать методическим документам по НК и условиям эксплуатации средств НК.
Помещения по месту (местам) осуществления деятельности лаборатории (в том числе по месту осуществления временных работ) должны находиться в собственности юридического лица или индивидуального предпринимателя или использоваться на ином законном основании, предусматривающем право владения и пользования.
Лаборатория может проводить НК по месту осуществления временных работ, если в соответствии с документами по НК работы проводятся за пределами места (мест) осуществления деятельности лаборатории, но с использованием средств НК, а также иных технических средств и материальных ресурсов, соответствующих требованиям раздела V настоящих Правил.
3.2. При НК с использованием источников ионизирующего излучения (ИИИ) обеспечивается выполнение требований по радиационной безопасности, установленных Федеральным законом от 9 января 1996года №3-ФЗ «О радиационной безопасности населения», требований по защите людей от вредного радиационного воздействия ИИИ, установленныхСанПиН2.6.1.2523-09 «Нормы радиационной безопасности (НРБ-99/2009)» (зарегистрированы Министерством юстиции Российской Федерации 14 августа 2009 года, регистрационный №14534).
3.2.1. Деятельность по НК с использованием ИИИ осуществляется при наличии у юридического лица или индивидуального предпринимателя санитарно-эпидемиологического заключения и специального разрешения (лицензии) на право осуществления этой деятельности, выданных уполномоченными на это органами.
При создании временных хранилищ источников излучения вне территории организации, в том числе для гамма-дефектоскопических аппаратов, используемых в полевых условиях, необходимо иметь санитарно-эпидемиологическое заключение о соответствии условий работы с источниками излучения (физическими факторами воздействия на человека) санитарным правилам.
3.2.2. Получение и передача источников ионизирующего излучения и содержащих их изделий, за исключением источников, освобожденных от необходимости оформления лицензии, разрешается только для юридических лиц или индивидуальных предпринимателей, имеющих лицензию на деятельность в области использования ИИИ, с обязательным информированием органов, осуществляющих федеральный государственный санитарно-эпидемиологический надзор по месту нахождения как передающего, так и принимающего ИИИ юридического лица или индивидуального предпринимателя.
3.3. Лаборатория, выполняющая работы по НК вне мест ее постоянного размещения, на временных или передвижных площадях и на объектах заказчика (в полевых условиях), должна подтвердить возможность надежной доставки средств НК к объекту с соблюдением требований радиационной безопасности и обеспечить проверку средств НК перед использованием после транспортировки.
V. Средства НК
5.1. ЛНК оснащается собственными средствами НК, обеспечивающими возможность выполнения работ по НК в рамках ее области аттестации.
Для проведения отдельных видов работ допускается использование оборудования, материалов, принадлежностей, принадлежащих другим юридическим или физическим лицам с условием (для средств измерений) их поверки(калибровки)и наличия документов, подтверждающих право владения и пользования.
5.2. Номенклатура средств НК определяется действующей нормативной технической и методической документацией по НК, распространяющейся на объекты контроля, виды (методы) НК и виды деятельности, при осуществлении которых проводится НК.
5.3. Каждое средство НК, которое имеется в лаборатории, включая и настроечные (контрольные) образцы, регистрируется в ЛНК. Сведения о средствах НК вносятся в Паспорт лаборатории и в регистрационные документы (учетный лист, карточка).
Сведения о средствах НК включают данные о:
- наименовании, типе средства НК;
- стране, заводе-изготовителе (фирме),заводском и инвентарном номере, годе выпуска, дате ввода в эксплуатацию;
- техническом обслуживании, ремонтах;
- поверке, калибровке, аттестации;
- местонахождении паспорта и (или) руководства по эксплуатации, методических указаний по поверке (если они входят вкомплект поставки прибора);
- свидетельствах (протоколах, сертификатах) поверки, калибровки, аттестации;
- перечне комплекта поставки прибора, если он не входит в состав других документов.
5.4. Сведения о средствах НК других организаций, индивидуальных предпринимателей и физических лиц, применяемых в лаборатории, вносятся в Паспорт лаборатории. При этом указывается срок, в течение которого лаборатория имеет право использовать не принадлежащее ей средство НК.
5.5. Средства НК, относящиеся к средствам измерения (дефектоскопы, преобразователи, меры и т.п.), поверяются или калибруются в установленном порядке.
5.6. В ЛНК имеются документированные процедуры технического обслуживания и проверки технического состояния используемых средств НК, а также графики поверки, калибровки, аттестации, технического обслуживания и проверки технического состояния собственных и временно привлеченных средств НК.
5.7.Каждая партия материалов для НК (порошки, суспензии, пенетранты, радиографические пленки, химические реактивы) до начала применения подвергаются входному контролю с оформлением отчетного документа, при котором проверяются: наличие на каждом упаковочном месте (пачке, коробке, емкости) этикеток (сертификатов), полнота приведенных в них данных и соответствие этих данных требованиям стандартов или технических условий на контролируемые материалы (при изготовлении реактивов и пенетрантов для собственных нужд проверяются только наличие этикетки и наименование реактива или пенетранта; отсутствие повреждений упаковки и материалов; срок годности; соответствие материалов применяемому методу (виду) НК.
VI. Персонал ЛНК
6.1. ЛНК имеет:
- руководителя лаборатории (при необходимости, технического руководителя, заместителей руководителя, заместителей технического руководителя), отвечающих в полном объеме за организацию, выбор видов (методов)и проведение работ по НК;
- аттестованный в независимых органах по аттестации системы НК персонал, имеющий соответствующую профессиональную подготовку, теоретические знания и практический опыт, необходимые для выполнения работ по НК (аттестация персонала в совокупности включает все виды (методы) и объекты НК, которые закреплены за лабораторией и входят в область ее аттестации).
Руководители юридических лиц и индивидуальные предприниматели, в состав которых входят лаборатории НК, руководители (технические руководители, их заместители) лабораторий (подразделений, осуществляющих НК) проходят подготовку и аттестацию в области промышленной безопасности в объеме вопросов и требований, необходимых для исполнения ими трудовых обязанностей в соответствии с требованиями пунктов 1 и 2 статьи 14.1 Федерального закона от 21 июля 1997г. № 116-ФЗ «О промышленной безопасности опасных производственных объектов». Иные работники лабораторий (дефектоскописты) проходят проверку знаний утвержденной в лаборатории документации, устанавливающей порядок и технологию производства работ по НК в соответствии с областью деятельности, характером и объемом выполняемых лабораторией НК работ.
Работниками лаборатории, непосредственно выполняющими работы по НК в области аттестации, состоящими в штате по основному месту работы, должно обеспечиваться проведение НК по не менее чем половине включенных в область аттестации объектов и видов (методов) НК.
Весь персонал лаборатории, как постоянный, так и привлекаемый, который может повлиять на деятельность лаборатории, действует беспристрастно, компетентен и работает в соответствии с системой менеджмента лаборатории.
6.2. Руководитель и технический руководитель лаборатории (заместители руководителя, технического руководителя), лица, ответственные за радиационную безопасность, систему менеджмента назначаются из числа сотрудников организации, работа для которых в данной организации является основной. В соответствии со статьей 66 Трудового кодекса Российской Федерации.
6.3. К работе с источниками излучения (в т.ч. гамма-дефектоскопическими и рентгеновскими дефектоскопами) допускаются лица не моложе 18 лет, не имеющие медицинских противопоказаний, отнесенные приказом руководителя к категории персонала группы А, прошедшие обучение по правилам работы с источником излучения (гамма-дефектоскопическими и/или рентгеновскими дефектоскопами) и по радиационной безопасности, и соответствующий инструктаж в соответствии с установленными требованиями.
6.4.В лаборатории обеспечиваются обучение, профессиональная подготовка, повышение квалификации, мероприятия по оценке опытности, ведется постоянный учет сведений об обучении, аттестации, повышении квалификации и профессиональном опыте каждого сотрудника, выполняющего НК.
Лаборатория устанавливает необходимые этапы подготовки каждого сотрудника, включающие:
- период официального введения в должность;
- период работы под наблюдением опытных сотрудников;
- постоянную подготовку на протяжении служебной деятельности.
6.5. Все сотрудники лаборатории имеют должностные инструкции, утвержденные руководителем юридического лица или индивидуальным предпринимателем (или назначенным ими лицом) и определяющие их служебные обязанности и связанную с ними ответственность. В случае применения новой техники и технологий, изменений в организации труда, изменения правовых актов и нормативных документов должностные инструкции пересматриваются в установленном в лаборатории порядке. В лаборатории ведутся записи, подтверждающие ознакомление персонала с должностными инструкциями.
6.6. В лаборатории назначаются лица, отвечающие за определенные участки работ, в частности за:
- хранение, проверку технического состояния, техническое обслуживание, эксплуатацию и метрологическое обеспечение средств НК;
- ведение фонда нормативных технических и методических документов;
- подготовку заключений (отчетов, протоколов, актов) о результатах НК, их проверку и утверждение;
- функционирование системы менеджмента;
- ведение и хранение документации по результатам НК;
- радиационную безопасность, учет и хранение источников ионизирующих излучений.
VII. Документация ЛНК
Перечень необходимых документов смотрите в разделе Перечень документов необходимых для аттестации лаборатории НК
Смотрите так же разделы:
Аттестация лабораторий неразрушающего контроля
Аттестация специалистов неразрушающего контроля
Перечень оборудования необходимого для аттестации лаборатории НК
Перечень документов необходимых для аттестации лаборатории НК
Частые вопросы по аттестации лабораторий НК
Цена услуг по аттестации лабораторий (калькулятор)
На сегодняшний день тепловизоры являются оптимальным инструментом неразрушающего теплового контроля в самых разных отраслях промышленности. Основные сферы применения промышленных тепловизоров это тепловой аудит объектов строительства, поиск неисправности электросетей, мониторинг производственных процессов и другие случаи, когда по неоднородности теплового поля можно судить о техническом состоянии контролируемых объектов.
Использование тепловизоров дает возможность выявить потенциально проблемные участки для проведения превентивного обслуживания, значительно сокращая дальнейшие затраты по эксплуатации. Ниже описаны наиболее востребованные направления современной строительной и промышленной термографии.
В строительстве одним из основных направлений теплового контроля является общий энергоаудит зданий и сооружений с целью оптимизации расходов на энергию. Проведение инспекции здания с последующим анализом его особенностей и данных о расходе энергии позволяет определять оптимальные способы снижения энергопотерь. Использование тепловизора для контроля строительных объектов имеет ряд преимуществ, одним из которых является возможность распознать причины потерь тепла, оценить их масштабы, и предпринять меры по их сокращению.
На объектах строительства тепловизор позволяет обнаружить различные дефекты кирпичной кладки и ограждающих конструкций, являющихся причиной утечки тепла. Термически слабые участки конструкций. проявляют себя через так называемые тепловые мостики которые тепловизор четко регистрирует. Полученная в результате контроля термограмма может служить доказательством производственного брака или некачественного проектирования.
Среди дефектов ограждающих конструкций, увеличивающих теплопотери, одними из самых распространенных является проблема с окнами. Дефекты оконных конструкций могут стать причиной повышенного шума, сквозняков, запотевания и сырости. Высокая чувствительность современных тепловизоров позволяет выявить даже минимальные перепады температуры, определяя места имеющихся дефектов для их последующего ремонта.
Еще одним направлением строительной термографии является тепловизионный контроль систем отопления, вентиляции и кондиционирования. Здесь частыми причинами энергопотерь могут быть ошибки проекта, нарушение правил эксплуатации, складирования и перевозки. Давая возможность в выявить участки с аномальным распределением температуры, результаты теплового контроля позволяют судить о правильности монтажа и наладке инженерных коммуникаций.
Среди других направлений тепловизионного контроля в строительстве, можно выделить, поиск мест проникновения влаги, поиск трубопроводов горячей и холодной воды и мест их разрывов.
Дополнительная информация
Статья - диагностика строительных конструкция методом инфракрасной термографии
Статья - комплексный тепловой контроль зданий и строительных сооружений
Статья - Оценка фактической теплозащиты зданий методом теплового контроля
Каталог Строительная термография Testo
ГОСТ Р 54852-2011 "Здания и сооружения. Метод тепловизионного контроля качества теплоизоляции ограждающих конструкций"
СНИП 2302-2003 "Тепловая защита зданий"
СНИП 2301-99 "Строительная климатология"
![]() |
![]() |
![]() |
В промышленном производстве основной целью теплового неразрушающего контроля является обнаружение дефектов оборудования на их ранней стадии. Аномальный нагрев, механических компонентов, часто может указывать на чрезмерную нагрузку, и риск выхода системы из строя. Использование промышленных тепловизоров дает возможность выявить проблемные участки для их превентивного обслуживания, значительно сокращая дальнейшие затраты по эксплуатации.
Современные тепловизоры применяются в самых разных отраслях промышленного производства. Среди наиболее распространенных направлений теплового контроля можно выделить превентивную диагностику промышленного оборудования, контроль заполнения резервуаров, поиск неисправности электросетей, мониторинг солнечных батарей, анализ критических температур на печатных платах и другие случаи, когда полученная термограмма дает возможность судить о техническом состоянии контролируемых объектов.
К типовым объектам тепловизионного контроля в промышленном производстве можно отнести станки, конвейеры, турбины, компрессоры, насосы, генераторы, ДВС, системы нагрева и охлаждения, различное гидравлическое оборудование.
Дополнительная информация
Статья - Тепловизионное обследование металлургических печей
Статья - Тепловизионное обследование дымовых труб
Практическое руководство по промышленной термографии
Каталог промышленная термография
![]() |
![]() |
![]() |
В работе предприятий энергетического сектора, основными направлениями теплового контроля является поиск перегретых участков электросетей, дымовых труб, паровых и водогрейных котлов. Тепловизоры также часто применяются для поиска неисправностей в теплоизоляции трубопроводов и турбин, определения мест подсоса холодного воздуха, для проверки эффективности работы систем охлаждения трансформаторов, двигателей, линий электропередач и другого оборудования.
К типовым объектам тепловизионного контроля в сфере энергетики можно отнести всевозможные конденсаторы, рубильники, распределительные щиты, места контактных соединений электропроводки, трансформаторы, генераторы, батареи, бойлеры, паровые системы и другое оборудование.
Отдельным направлением тепловизионного контроля в энергетике, является мониторинг солнечных энергосистем, который проводится для обеспечения безопасности и анализа эксплуатационных показателей. В современных тепловизорах предусмотрена возможность ввода показателя интенсивности солнечного излучения, которое сохраняется вместе с тепловыми снимками в в дальнейшем может быть использовано для анализа результатов контроля.
Практическое примениние тепловизоров для теплового контроля объектов энергетики
Статья - Тепловизионное обследование дымовых труб
Подробнее о применении тепловизоров в энергетике
РД 153-34.0-20.363-99 «Основные положения метода инфракрасной диагностики электрооборудования и высоковольтных линий
![]() |
![]() |
![]() |
В нефтегазовом комплексе тепловизоры нашли свое применение при контроле наполняемости резервуаров, позволяя дистанционно определять температуру и уровень жидкости, делая этот процесс максимально быстрым и безопасным (при отказе систем автоматического оповещения). Тепловизоры также применяются для контроля систем противопожарной защиты, систем резервуарного парка, таких как трубопроводы и электрооборудование, позволяя дистанционно выявлять места критического изменения температур. При использовании тепловизоров, контроль магистральных трубопроводов возможен с высоты до 500 метров и скоростью полета до 300 км/ч
В химической промышленности тепловизор решает похожие задачи, что и в нефтегазовом секторе, а именно проверка уровня жидкости резервуаров, диагностика герметичности и изоляции емкостей, общий мониторинг температуры веществ. Важным преимуществом тепловизионного контроля в химической отрасли является очень низкий уровень теплового воздействия, кроме того, использование тепловизора возможно как в стационарном режиме, так и в процессе работы установок. Быстрота и достоверность результатов теплового контроля позволяют оперативно реагировать на протекание химических процессов.
Дополнительная информация
Статья - Опыт применения теплового контроля в нефтепереработке
Практическое руководство по промышленной термографии
![]() |
![]() |
![]() |
В сфере электроники и электротехники тепловизоры позволяют оценить уровень нагрева в системах низкого, среднего и высокого напряжения. Полученные термограммы дают возможность своевременно обнаружить неисправные компоненты и предпринять меры по их ремонту.
В процессе контроля электротехнического оборудования, важным плюсом тепловизоров является бесконтактный характер их применения. Кроме того, контроль с использованием тепловизора не требует прекращения рабочих процессов на время его проведения. Полученная термограмма дает информацию о состоянии объектов, тепловой контроль которых без применения тепловизоров невозможен или сильно затруднен, например, в случае с кабелями, проложенными в технических рукавах и потолочных нишах.
Среди основных направлений теплового контроля в сфере электротехники можно выделить контроль систем распределения электроэнергии (трехфазные системы, распределительные щиты, предохранители, электропроводка, подстанции, измерительные лаборатории), контроль электромеханического оборудования (электродвигатели, насосы, вентиляторы, подшипники, коробки передач и конвейеры), контроль промышленных контрольно-измерительных приборов (контроллеры, трубы, клапаны, конденсационные баки и резервуары и прочее).
Дополнительная информация
Подробнее о применении тепловизоров в электронике
РД 153-34.0-20.363-99 «Основные положения метода инфракрасной диагностики электрооборудования и высоковольтных линий
![]() |
![]() |
![]() |
Технология SuperResolution
Специалисты во многих отраслях промышленности часто сталкиваются с необходимостью теплового контроля мелких и удаленных объектов. Контроль таких объектов требует высокого разрешения, недоступного в тепловизорах начального и среднего уровня. Применение же моделей с высоким разрешением (640x480) часто бывает ограничено бюджетом организации.
Данная проблема особенно актуальна в области микроэлектроники, где требуются термограммы с максимально высоким разрешением. С аналогичными трудностями также можно столкнуться в области энергетики и строительства, где объекты контроля могут находиться на расстоянии нескольких метров, например крыши зданий и линии электропередач.
Разработанная компанией Testo технология SuperResolution дает возможность улучшить пространственное разрешение тепловых снимков в 1,6 раза а количество температурных точек в 4 раза позволяя получить термограмму сравнимую по качеству с детектором более высокого класса.
При создании термограмм SuperResolution, используется комбинация двух технологий – метод супервыборки и метод обратной свёртки или деконволюции. Благодаря синтезу этих методов, использование естественного движения руки в процессе контроля, является основой для создания серии снимков, из которых комбинируется термограмма с улучшением пространственного разрешения в 1,6 раза. Обработка термограммы происходит в режиме реального времени и занимает примерно 0,5 секунды.
Говоря более простым языком, при использовании технологии SuperResolution, тепловизор делает не один а сразу четыре снимка. Из-за естественных колебаний руки все четыре изображения получаются уникальными. Далее программы IRSoft проводит анализ и выдает итоговое изображение с разрешением, в два раза выше, чем у исходников.
Необходимо отметить, что для создания снимков технология SuperResolution использует реальные температурные значения без использования процесса интерполяции, при котором создаются искусственные промежуточные значения температур без дополнительных сведений. Такие искусственно сгенерированные значения не могут превышать «соседние» значения, что недопустимо при контроле температур малых объектов, в частности – при поиске горячих точек. В отличие от интерполяции технология SuperResolution направлена на повышение разрешения и степени детализации с возможностью воссоздания изначальных характеристик сигнала, выполняя программный расчёт показаний исходя из массива данных, поэтому результат максимально сходен с изображением, получаемым от матрицы с более высоким разрешением.
![]() |
На приведенном графике, чёрная кривая – это исходный сигнал, белые столбики это исходные значения пикселей. Серые столбики это искусственно сгенерированные значения интерполяции, с помощью которых воссоздать исходный сигнал невозможно. Оранжевые столбики это значения, полученные посредством технологии Super Resolution которые могут быть использованы для воссоздания исходного сигнала. Как видно из приведенных графиков, при помощи технологии SuperResolution выполняется расчёт реальных значений, результат которого можно сравнить с изображением, созданным тепловизором с детектором более высокого класса. На практике это означает, что при неизменном расстоянии теплового контроля, полученная термограмма будет более детальной. Как результат, изображение с разрешением 160х120 по качеству будет соответствовать изображению 320х240 пикселей, термограмма 320х240 пикселей, станет термограммой 640х480 пикселей, а снимок 640х480 пикселей – снимком с разрешением 1280х960 пикселей. При этом каждый полученный в результате пиксель будет содержать реальные температурные значения контролируемых объектов. Пример изображен следующих рисунках.
![]() |
![]() |
Снимок, сделанный тепловизором testo 881 с разрешением 160 х 120 пикселей и снимок того же прибора, но с использованием технологии SuperResolution с качеством изображения аналогичным детектору 320 х 240 пикселей.
![]() |
![]() |
Термограмма тепловизора testo 885 с разрешением 320 х 240 пикселей и термограмма, полученная при обработке SuperResolution, с качеством изображения аналогичным детектору 640 X 480 пикселей.
Технология Testo SuperResolution доступна для всех моделей тепловизоров серий тесто 875, тесто 876, тесто 881, тесто 882, тесто 885 и тесто 890. С помощью специального обновления встроенного ПО возможно дооснащение поставленных ранее моделей технологией SuperResolution.
В строительной термографии технология SuperResolution идеально подходит для быстрого и эффективного обнаружения дефектов строительства, а также для анализа потерь энергии в системах отопления и кондиционирования зданий, особенно при контроле удаленных объектов.
В сфере энергоснабжения технология значительно упрощает процесс теплового контроля систем низкого, среднего и высокого напряжения где предъявляются особые требования к разрешению полученных термограмм.
В области научно-исследовательских работ и электроники высокое разрешение SuperResolution может быть полезна для анализа распределения тепла на печатных платах и любых мельчайших деталей.
Подводя итог вышесказанному, можно сделать вывод - технология SuperResolution это возможность точного измерения температур мелких и удаленных объектов без необходимости в использовании детектора более высокого класса.
Видео презентация технологии Testo SuperResolution
Подпишитесь на наш канал RuTubeПрограммное обеспечение Testo IRSoft для анализа термограмм
IRSoft программное обеспечение для профессионального анализа термограмм на ПК, разработанное компанией Testo.
Аналитические функции программы IRSoft дают возможность корректировки коэффициента излучения различных материалов для отдельных областей снимка, вплоть до каждого пикселя. Функция гистограммы отображает распределение температур на контролируемой поверхности с возможностью анализа температурных кривых, определения границ предельных значений, самой холодной/горячей точки. Программа имеет возможность параллельного анализа нескольких термограмм с функцией переноса правок с текущего изображения на все открытые снимки одним нажатием клавиши. Также предусмотрена возможность добавления голосовых и текстовых комментариев.
Помимо своего функционала программа IRSoft отличается понятной структурой и удобством в использовании. Все функции программы сопровождаются интуитивно понятными символами и подсказками. Помощник создания отчетов имеет пошаговую инструкцию и типовые шаблоны облегчающие процесс работы неопытным пользователям. Шаблоны содержат информацию о местах проведения контроля, поставленных задачах и полученных результатах, в том числе по стандарту DIN EN 13187. Также предусмотрена возможность создания индивидуальных шаблонов с учетом требований заказчика.
Полная версия программы IRSoft поставляется в комплекте со всеми моделями тепловизоров Testo. Скачать программу бесплатно, можно перейдя по ссылке. Презентация программного обеспечения IRSoft для тепловизоров Testo
Программа обработки термограмм тепловизоров Тесто
Программа для анализа термограмм тепловизоров Testo
IRSoft – программное обеспечение тепловизоров Testo
Среди других технологий и потребительских свойств тепловизоров Testo можно выделить:
Температурная чувствительность. При регистрации самых незначительных перепадов температур особенно важным фактором является оптимальная температурная чувствительность (NETD). Тепловизоры Testo обеспечивают высокую температурную чувствительность до < 30 мК, которая в комбинации с высокой разрешающей способностью позволяет визуализировать малейшие перепады температур независимо от размеров обследуемого объекта.
Возможность измерения высоких температур. В некоторых секторах промышленности необходимо измерение очень высоких температур. У тепловизоров Testo есть возможность расширения температурного диапазона до 1200°C. Данный максимум делает тепловизоры Testo применимыми практически в всех отраслях промышленности. Высококонтрастное отображение высоких и низких температур возможно благодаря высокотемпературной цветовой палитре Iron HT или специальной компенсации на гистограмме.
Анализ тепловых процессов в режиме реального времени. С помощью функции создания полностью радиометрических видеозаписей пользователи тепловизоров Testo имеют возможность регистрировать тепловые процессы в режиме реального времени. В дальнейшем термографические видеозаписи могут передаваться на ПК для детального анализа любого момента видеозаписи содержащей данные температуры по каждому пикселю. Данная функция полезна при контроля всех стадий нагрева в течении определенного промежутка времени. Кроме того, функция регистрации данных обеспечивает возможность создания серии отдельных изображений в заданные временные интервалы или после определенных событий, например после превышения допустимых температур. В качестве опции, функция доступна для тепловизоров Тесто 885-2 и Тесто 890-2
Технология TwinPix (двойное изображение). Тепловизоры Testo с встроенной цифровой камерой выполняют одновременное сохранение инфракрасного и реального изображений. Новая функция наложения снимков Testo TwinPix накладывает эти изображения друг на друга делая термограмму намного проще для восприятия. Настройка уровней прозрачности и диапазона критических температур регулируют соотношения реального и инфракрасного изображения, после чего проблемные участки выделяются характерным цветом делая термограмму гораздо более наглядной чем инфракрасная. Данная функция применима даже если объекты контроля находятся на разных расстояниях.
Тепловизоры Тесто – технология твинпикс
Режим измерения “Солнечная энергия”. Интенсивность солнечного излучения играет важную роль в диагностике фотоэлектрических систем. При недостаточно интенсивном солнечном свете получение качественной термограммы невозможно. При выполнении измерений в режиме “Солнечная энергия” возможен ввод параметров интенсивности солнечного излучения, которое сохраняется в памяти тепловизора для дальнейшего анализа термограмм с помощью программы IRSoft.
Беспараллаксный лазерный целеуказатель, выводимый на дисплей тепловизоров Testo, облегчает решение задач теплового мониторинга, помогая не упускать из вида контролируемые объекты.Точка-ориентир зеркально отображает область замера, на которую наведен лазерный указатель. Помимо этого на дисплее отображается точная температура точки, находящейся под прицелом лазера.
Интуитивное управление. При разработке тепловизоров Testo большое внимание было уделено возможности интуитивного управления приборами. В результате, управление любой моделью осуществляется пользователем с максимальной легкостью.Новое гибридное управление дает возможность навигации через сенсорный дисплей. с помощью одной руки, это позволяет пользователю держать вторую руку свободной (например, в целях безопасности).
Оптимальная эргономичность тепловизоров Testo позволяет эффективней справляться с задачами строительной термографии. Помимо широко известных моделей тепловизионных камер с дизайном рукоятки-пистолета тесто предлагает модели в форме видеокамеры, оснащенные откидным поворотным дисплеем, позволяющим располагать тепловизор наиболее удобным способом для создания термограмм любых участков. Эргономичная вращающаяся рукоятка обеспечивает дополнительную надежность и удобство при проведении съемки труднодоступных участков.
Технология SiteRecognition дает возможность точной идентификации местоположения контролируемых объектов. Данная функция особенно актуальна при тепловом контроле большого количества сходных предметов, когда могут возникнуть сложности при идентификации сделанных термограмм. Технологии SiteRecognition автоматически распознает объекты по специальным отметкам обрабатываемых программой. Для удобства пользователей возможен поиск по названию объекта, дате или температурным параметрам. Технология SiteRecognition так же дает возможность просмотреть и сравнить снимки за прошедшие периоды. Подробное описание технологии SiteRecognition
Частые вопросы по тепловому контролю
Как выбрать тепловизор?
Выбирая тепловизор прежде всего надо определиться для каких задач он будет использоваться и исходя из этого подобрать прибор с соответствующими техническими характеристиками не переплачивая за функции которые в дальнейшем не пригодятся. Описание основных ценообразующих характеристик, которые помогут ответить на вопрос – как выбрать тепловизор, приведено здесь.
Чем тепловизоры Testo лучше аналогичных моделей других производителей?
Смотрите сравнение тепловизоров Testo с конкурентами Flir, Fluke, SAT, NEC
Как рассчитать поле зрения тепловизора и минимальный контролируемый объект?
Для того чтобы определить поле зрения тепловизора и минимальный объект точную температуру которого он способен измерить. Можно воспользоваться конвертером поля зрения тепловизоров Тесто.
В каких случаях необходим дополнительный узкоугольный объектив?
Объектив определяет поле зрения тепловизора. Стандартный широкоугольный объектив позволяет сделать снимок большого участка с близкого расстояния. Дополнительные узкоугольные объективы дают возможность контролировать мелкие, удаленные объекты. По общему правилу - чем меньше угол поля зрения, тем дальше можно отойти от объекта, без потери качества термограммы
Чтобы определиться с необходимостью покупки дополнительного узкоугольного объектива надо знать примерное максимальное расстояние до объекта контроля, его размер и требования к качеству получаемых термограмм. Дальнейший расчет можно произвести при помощи конвертера поля зрения тепловизоров Тесто
Какой тепловизор необходим для аттестации лаборатории неразрушающего контроля?
Для аттестации лаборатории НК по тепловому методу контроля, достаточно самого бюджетного тепловизора представленного в линейке приборов Testo. Стоимость аттестации можно рассчитать здесь.
Что такое – технология SuperResolution?
Технология SuperResolution (супер разрешение) дает возможность без использования процесса интерполяции, улучшить пространственное разрешение тепловых снимков в 1,6 раза а количество температурных точек в 4 раза, позволяя получить термограмму сравнимую по качеству с детектором более высокого класса. С подробным описанием технологии, можно ознакомиться здесь.
Возможно ли наблюдать процессы нагрева и охлаждения в динамике?
Динамику тепловых процессов можно отобразить, используя серию термограмм сделанных через заданные промежутки времени или при помощи функции создания полностью радиометрических видеозаписей, которая позволяет регистрировать тепловые процессы в режиме реального времени. Данной функцией в качестве опции могут оснащаться модели testo 885-2 и 890-2.
На до ли поверять тепловизор?
Тепловизор это измерительный инструмент подлежащий поверке с периодичностью один раз в год. Тепловизоры не внесенные в Госреестр средств измерений РФ подлежат калибровке с той же периодичностью. Если тепловизор не поверен (не откалиброван) то работы, выполненные с его помощью могут быть признаны не действительными, т.к. к отчету с результатами теплового контроля должно прикладываться действующее метрологическое свидетельство.
Стоимость поверки тепловизора зависит от срока и диапазона поверяемых температур. На октябрь 2013 стоимость поверки составляет:
- поверка тепловизора в диапазоне от -20 до 400 ˚С (срок - 21 день) - 16 500р.
- поверка тепловизора в диапазоне от -20 до 400 ˚С (срок – 7 дней) - 26 500р.
- поверка тепловизора в диапазоне от 0 до 1200 ˚С (срок - 21 день) - 19 000
- поверка тепловизора в диапазоне от -20 до 1200 ˚С (срок - 21 день) - 23 000р.
Когда лучше покупать тепловизор?
Поскольку тепловизоры часто используются для контроля систем отопления и отапливаемых объектов, пик использования приборов приходится именно на отопительный сезон, поэтому оптимальное время покупки тепловизора в многом связано со сроками отопительного сезона в регионе где планируется его использование. Оптимальным временем для покупки тепловизора (в центральном регионе) можно считать период с июля по сентябрь. Причины следующие:
- цена на тепловизоры до начала сезона часто бывает ниже чем после;
- поверка купленного летом тепловизора закончится через 12 месяцев, следовательно, у владельца прибора будет время оформить новое свидетельство до начала следующей сезонной эксплуатации. Для справки – не срочная поверка тепловизора в ФБУ "Ростест-Москва" выполняется в срок 21 день.
Оказываете ли вы услуги по тепловизионному контролю?
Лаборатория НТЦ «Эксперт» оказывает услуги по тепловому контролю промышленных и жилых объектов. Тепловой контроль проводится с применением современных промышленных тепловизоров и других приборов. По результатам контроля составляется подробный отчет, включающий наглядную тепловую карту (термограмму), заключение о качестве объекта и рекомендации по устранению выявленных дефектов.
Каков порядок аттестации специалистов проводящих тепловой контроль?
Тепловой контроль опасных производственных объектов перечисленных в приложении 1. СДАНК-01-2020, выполняется лабораторими НК располагающими аттестованным в установленном порядке персоналом. Подробная информация по аттестации специалистов содержится здесь. Информация по аттестации лабораторий здесь.
Порядок лицензирования специалистов проводящих тепловой контроль на объектах, не относящихся к опасным производственным объектам, регулируется соответствующими отраслевыми ведомствами и саморегулируемыми организациями.
Для начинающих пользователей полезно будет ознакомиться с практическим руководством по промышленной термографии. В руководстве рассмотрены вопросы связанные с теорией тепловизионного контроля, условиями его проведения, распространенными ошибками и другая полезная информация.
Источник - статья Е. А. Иванова опубликованная в журнале «В мире НК» № 3(17). сентябрь 2002.
Другие статьи на тему аттестации специалистов и лабораторий неразрушающего контроля можно посмотреть в разделе Статьи.
Задача обеспечения промышленной безопасности в условиях продолжающегося физического износа оборудования на опасных производственных объектах и отсутствия средств на его замену и реконструкцию обуславливает повышение роли созданной Госгортехнадзором России Системы НК как одного из основных факторов, определяющих техническое состояние указанных объектов, возможность и сроки их дальнейшей эксплуатации [1].
В 2000 г. износ действующих в России фондов достиг 42,4 % при коэффициенте обновления 1,2 % по сравнению с 5,8 % в 1990 г. и 8,2 % в 1980 . В настоящее время на опасных производственных объектах до 60–80 % технических устройств и сооружений выработали проектные сроки эксплуатации [2]. Даже при условии реализации мероприятий, предусмотренных постановлением Правительства РФ [3], к 2010 г. планируется обновить только около 30 % оборудования на опасных производственных объектах. Таким образом, значительная часть оборудования опасных производственных объектов будет эксплуатироваться после выработки проектных сроков эксплуатации. Дальнейшая эксплуатация такого оборудования без проведения специальных мер по обеспечению промышленной безопасности не только нецелесообразна экономически, но и представляет природную и техногенную опасность и обуславливает необходимость проведения комплексных мероприятий по оценке возможности эксплуатации оборудования с истекшим нормативным сроком эксплуатации.
Решение задач по поддержанию высокой эксплуатационной надежности опасных производственных объектов требует совершенствования и более широкого использования мониторинга технического состояния оборудования и сооружений на опасных производственных объектах, что целесообразно осуществлять путем проведения НК и ТД с последующей оценкой ресурса эксплуатации до наступления предельного состояния.
Признавая, что только комплексный подход обеспечит повышение достоверности, воспроизводимости и сопоставимости результатов НК, а также принятие своевременных и адекватных решений по обеспечению промышленной безопасности и станет основой обеспечения необходимого уровня эксплуатационной безопасности технических устройств, зданий и сооружений на опасных производственных объектах, Госгортехнад-зор России создал Систему НК. Актуальность развития и совершенствования НК в отраслях промышленности определяется тем, что постановлением Правительства [4] Госгортехнадзору России поручено организовать работы по развитию и внедрению системы контроля, позволяющего осуществлять экспертизу промышленной безопасности и проводить техническое диагностирование для принятия решения о продлении срока безопасной эксплуатации на опасных производственных объектах на территории России. Данным постановлением установлено, что продление срока безопасной эксплуатации технических устройств, оборудования и сооружений, эксплуатируемых на опасных производственных объектах на территории РФ, осуществляется в порядке, определяемом Госгортех-надзором России.
В соответствии с принятой «Концепцией...» [1] вводится аттестация персонала, лабораторий, методических документов и средств НК.
Первой подсистемой Системы НК, реализованной в практической деятельности организаций, осуществляющих НК на опасных производственных объектах, стала аттестация лабораторий НК. Аттестация лабораторий, выполняющих НК на объектах котлонадзора и подъемных сооружениях, проводилась с1996 г. Ввиду общности целей и близости задач работы по аттестации лабораторий НК было решено проводить в рамках Системы экспертизы промышленной безопасности [1].
Для аттестации лабораторий НК создана организационно-методическая база. Прошли регистрацию в Минюсте России (25.07.2000 N 2324) и постановлением Госгортехнадзора России от 25.09.2000 N 54 введены в действие «Правила аттестации и основные требования к лабораториям неразрушающего контроля» ПБ 0337200. К 1 января 2002 г. в организациях, подконтрольных 20 территориальным управлениям ГосгортехнадзораРоссии, аккредитовано 32 Независимых органа по аттестации лабораторий НК (НОАЛ): в Управлении Московского округа – 9; в Управлении Северо-Западного округа – 3; в Управлении Западно-Уральского округа и Самарском управлении – по 2; в 18 управлениях – по одному НОАЛ. С момента введения в действие ПБ 03-372-00 до 1 января 2002 г. в организациях, подконтрольных 36 территориальным органам Госгортехнадзора России, аттестовано 850 лабораторий НК.
Функционирование подсистемы аттестации лабораторий позволило определить некоторые статистические характеристики подразделений НК, выполняющих НК на опасных производственных объектах. Распределение областей аккредитации НОАЛ и аттестации лабораторий НК по промышленным секторам * и видам (методам) НК приведены в табл. 1 и 2.
* Промышленный сектор определяется конкретными типами технических устройств и сооружений, надзор за эксплуатацией которых на опасных производственных объектах осуществляют отраслевые управления и отделы Госгор-технадзора России.
Таблица 1. Распределение аккредитованных НОАЛ и аттестованных лабораторий НК по промышленным секторам
Области аккредитации НОАЛ и области аттестации лабораторий НК по промышленным секторам | % от общего количества: | |
аккредитованных НОАЛ | аттестованных лабораторий НК | |
Оборудование, работающее под избыточным давлением | 97 | 63 |
Системы газоснабжения (газораспред.) | 94 | 52,8 |
Подъемные сооружения | 84 | 43 |
Оборудование нефтяной и газовой промышленности | 72 | 32 |
Оборудование взрывоопасных и химически опасных производств | 63 | 28 |
Оборудование металлургической промышленности | 47 | 5,4 |
Объекты горнорудной промышленности | 19 | 1,5 |
Объекты угольной промышленности | 19 | 0,7 |
Объекты железнодорожного транспорта | 0 | 0,4 |
Объекты хранения и переработки зерна | 6 | 0 |
Таблица 2. Распределение аккредитованных НОАЛ и аттестованных лабораторий НК по видам (методам) НК
Виды (методы) НК в области аккредитации НОАЛ и области аттестации лабораторий НК | % от общего количества: | |
аккредитованных НОАЛ | аттестованных лабораторий НК | |
1. Ультразвуковой | 100 | 84,3 |
2. Визуальный и измерительный | 100 | 79,7 |
3. Радиационный | 96,9 | 68,8 |
4. Проникающими веществами | 93,8 | 46,3 |
5. Магнитный | 90,6 | 39 |
6. Акустико-эмиссионный | 81,3 | 8,7 |
7. Вихретоковый | 56,3 | 7 |
8. Вибродиагностический | 34,4 | 2,1 |
В области аккредитации НОАЛ входит от 2 до 8 промышленных секторов и от 3 до 8 видов (методов) контроля. Сведения о количестве промышленных секторов и количестве видов (методов) НК в области аккредитации НОАЛ и области аттестации лаборатории НК приведены в табл. 3.
Таблица 3. Распределение НОАЛ и лабораторий НК по количеству промышленных секторов и видов (методов) НК в области аккредитации (аттестации)
Области аккредитации НОАЛ и области аттестации ЛНК | % от общего количества НОАЛ (лабораторий НК), имеющих в области аккредитации (аттестации) следующее количество промышленных секторов, видов (методов) контроля | ||||||||
1 | 2 | 3 | 4 | 5 | 6 | 7 | 8 | ||
НОАЛ | Промышленных секторов | 3,1 | 6,3 | 9,4 | 15,6 | 37,5 | 6,3 | 6,3 | 15,6 |
Видов (методов) НК | 0 | 0 | 3,1 | 6,3 | 6,3 | 18,8 | 50,0 | 15,6 | |
ЛНК | Промышленных секторов | 34,2 | 30,9 | 17,6 | 10,9 | 5,9 | 0,2 | 0,2 | 0,1 |
Видов (методов) НК | 10,0 | 16,1 | 25,9 | 27,6 | 13,5 | 4,0 | 2,7 | 0,2 |
Более 65 % лабораторий НК выполняют работы по НК в 1–2 промышленных секторах, почти 30 % — в 3–4 секторах. Более половины лабораторий выполняют НК 3–4 видами (методами) контроля. Как правило, это ультразвуковой и/или радиационный, капиллярный и/или магнитный и визуально-измерительный виды (методы).
Наименьшее количество видов (методов) контроля применяют лаборатории, выполняющие НК только на объектах газоснабжения (часто только рентгенографический метод). Наибольшее количество видов (методов) применяется при НК на объектах котлонадзора и при контроле оборудования взрывопожароопасных и химически опасных производств. При контроле оборудования этих объектов кроме вышеперечисленных часто используется вихретоковый и акустико-эмисси-онный методы НК, реже вибродиагностический.
Аттестация лабораторий позволила упорядочить, во-первых, организационные формы подразделений НК, их структуру, подчиненность, взаимоотношения с другими подразделениями и сторонними организациями, обеспечение принципов независимости при НК как структурных подразделений, так и персонала лаборатории. Во-вторых, упорядочить документированные процедуры, которыми руководствуется лаборатория, включая:
- правовые и организационно-методические документы – учредительные документы юридических лиц и положения подразделений НК рганизации, документированные процедуры обеспечения качества при НК;
- методические документы по НК и технологические документы по объектам контроля, позволяющие осуществлять контроль и производить оценку качества технических устройств и сооружений видами (методами) НК, включенными в область аттестации лаборатории;
- документацию по персоналу лаборатории – должностные инструкции и документы, подтверждающие квалификацию и аттестацию по типам технических устройств и сооружений видами (методами) НК, включенными в область аттестации лаборатории, аттестацию на знание правил безопасности;
- ведение документооборота лаборатории и архива, наличие процедур проведения работ по НК, включая оформление результатов контроля, выдачу заключений и их хранение, обеспечение конфиденциальности и охраны прав собственности.
В-третьих, аттестация лабораторий позволила упорядочить оснащенность техническими средствами НК и их состояние – организацию учета, технического обслуживания, ремонта и метрологической аттестации (поверки), достаточность для организации контроля технических устройств и оборудования видами (методами) НК, включенными в область аттестации лаборатории.
Аттестация лабораторий НК является комплексной оценкой функционирования всех элементов аттестации в Системе НК, при аттестации лабораторий проверяются правильность и обоснованность аттестации технических средств, методических документов и персонала НК.
Таким образом, аттестация лабораторий НК является критерием организационной и технической готовности к выполнению эффективного и достоверного НК технических устройств, зданий и сооружений, основанного на реализации возможностей современных технических средств и методик контроля, единых требований к подготовке и аттестации персонала, а также к управлению структурными подразделениями, осуществляющими НК на опасных производственных объектах. Выполнение работ по НК аттестованной лабораторией является гарантией соблюдения технологической дисциплины НК и обеспечения промышленной безопасности на опасных производственных объектах.
Дальнейшее развитие получила подсистема аттестации персонала НК. Постановлением Госгортехнадзора России от 23.01.2002 N 3 утверждены и прошли регистрацию в Минюсте России от 17.04.2002 N 3378 «Правила аттестации персонала в области неразрушающего контроля» СДАНК-02-2020. Они охватывают все виды (методы) НК и всю номенклатуру технических устройств, зданий и сооружений, применяемых на опасных производственных объектах, гармонизированы с требованиями и процедурами Системы НК и международных стандартов в области аттестации персонала НК, что позволит полнее реализовать положения Федерального закона [5] в части аттестации работников в области промышленной безопасности.
Задержка с организацией работы подсистем аттестации методических документов и средств НК приводит к тому, что не по всей номенклатуре технических устройств и сооружений на опасных производственных объектах имеются документы по НК. Действующие документы имеют разный уровень утверждения, согласования и сроки разработки. В лабораториях НК не исключены случаи применения технических средств, не обеспечивающих необходимое качество НК, недостаточно метрологическое обеспечение НК.
Таким образом, подтверждается необходимость функционирования всех элементов Системы НК – подготовки и аттестации специалистов НК и применяемых методических документов, организации процесса контроля, а также состояния и технического уровня используемых средств контроля.
Ближайшими задачами развития Системы НК являются:
- принятие и введение в действие документированных процедур аттестации методических документов и технических средств НК;
- реализация принципа безопасной эксплуатации оборудования на опасных производственных объектах по его техническому состоянию с оценкой остаточного ресурса по определяющим критериям, установленными методами НК и ТД.
Решение этих задач внесет существенный вклад в обеспечение промышленной безопасности опасных производственных объектов.
Литература
1. Концепция управления Системой неразру-шающего контроля и основные направления ее развития, Система неразрушающего контроля. Аттестация лабораторий (сборник документов). Сер. 28. Вып. 1. – М.: ГУП «НТЦ «Промышленная безопасность», 2000. С. 5–16.
2. Государственный доклад «О состоянии промышленной безопасности опасных производственных объектов, рационального использования и охраны недр Российской Федерации в 2000 году» /Под ред. В.М. Кульечева. – М.: ГУП «НТЦ «Промышленная безопасность», 2001. – 196 с.
3. Федеральная целевая программа «Энергоэффективная экономика» на 2002–2005 гг. и на перспективу до 2010 г. (утверждена постановлением Правительства РФ от 17.11.2001 N 796). – Собрание законодательства РФ. 2001. N 49. С. 10242–10298.
4. Постановление Правительства РФ от 28.03.2001 N 241 «О мерах по обеспечению промышленной безопасности опасных производственных объектов на территории Российской Федерации». – Там же. 2001. N 15. С. 3367.
5. Федеральный закон «О промышленной безопасности опасных производственных объектов» – М.: НТЦ «Промышленная безопасность», 1999. – 36 с.
Источник - статья Г. Я. Дымкина опубликованная в журнале «В мире НК» № 4(10). декабрь 2000.
Другие статьи на тему аттестации специалистов и лабораторий неразрушающего контроля можно посмотреть в разделе Статьи.
Требования по обеспечению эксплуатационной надежности пути и подвижного состава обуславливают необходимость повышения эффективности систем НК транспортных конструкций как при их изготовлении, так и при эксплуатации и ремонте. Техническая эффективность систем НК в значительной мере зависит от надежности комплекса "дефектоскоп-оператор-среда", которая, в свою очередь, определяется квалификацией дефектоскопистов и правильной организацией процесса НК.
В путевом, вагонном, пассажирском и локомотивном хозяйствах ж.-д. транспорта России в области НК по 25 специализациям и должностям работает более 14 тыс. специалистов, функционирует около 900 лабораторий (подразделений ) НК[1].
Для повышения эффективности действующих систем НК МПС России введены отраслевые Система сертификации персонала по НК (ССПНК ЖТ) и Система аккредитации лабораторий НК (САЛНК ЖТ), функционирующие как подсистемы в рамках соответствующих национальных систем, введенных Госстандартом России.
ССПНК ЖТ регламентируется "Правилами сертификации персонала по НК технических объектов железнодорожного транспорта. ПР 32.113-98".
Сертификации подлежат специалисты по магнитному, вихретоковому и акустическому (ультразвуковому) видам (методам) НК элементов, деталей и узлов следующих технических объектов:
- вагоны грузовые и пассажирские;
- локомотивы;
- рельсы железнодорожные;
- мостовые конструкции железнодорожные, металлические.
Сертификацию проводят Дорожные (региональные) Уполномоченные органы и экзаменационные центры, аккредитованные в российской системе после прохождения экспертизы и признания их в соответствии с "Положением об экспертизе уполномоченных органов и экзаменационных центров П ССПНК ЖТ.01-98". В настоящее время действуют:
Уполномоченные органы
- Аттестационный центр "Путь" при НК-Центре (Санкт-Петербург);
- Уральский центр аттестации (Екатеринбург).
Экзаменационные центры
- На Западно-Сибирской ж. д. (при СибГУПС, г. Новосибирск);
- На Восточно-Сибирской ж. д. (при Дорожном центре обучения, ст. Суховская).
Документами ССПНК ЖТ конкретизированы требования к специальной подготовке персонала по НК. Подготовка к сертификации должна проводиться в Учебных центрах, получивших свидетельство о признании согласно "Положению об экспертизе учебных центров... П ССПНК ЖТ.02-98" и по программам, согласованным Экспертной организацией МПС России по НК. Функции экспертной организации МПС РФ по НК возложены на "Отраслевой учебно-методический и аттестационный центр по НК и диагностике технических объектов" (НК-Центр) при НИИ мостов и дефектоскопии МПС России. Первыми на сети ж. д. России прошли экспертизу и признаны Учебные центры по НК при Дорожном центре обучения Восточно-Сибирской ж. д., Дорожной технической школе № 1 Свердловской ж. д., СибГУПС и Западно-Сибирской ж. д., Дорожном центре обучения Забайкальской ж. д. В них осуществляется подготовка специалистов к сертификационным экзаменам на I и II уровни квалификации по НК рельсов, а также деталей и узлов вагонов и локомотивов. Подготовка к экспертизе Учебных центров ведется на Северо-Кавказской, Дальневосточной, Северной и Горьковской ж. д.
В первую очередь проходят сертификацию руководители подразделений НК предприятий ж. д. С момента введения ССПНК ЖТ сертифицировано 176 специалистов с 15-ти железных дорог, среди которых наиболее активны Октябрьская, Северная и Свердловская. Около 33% из числа сертифицированных - дефектоскописты рель-сосварочных предприятий и начальники участков дефектоскопии дистанций пути, 35 % - специалисты по НК вагонного и пассажирского хозяйств.
Сертификация не заменяет, а дополняет и предваряет действующую систему аттестации персонала в области НК.
Организационная структура САЛНК ЖТ, порядок аккредитации и специальные требования к лабораториям НК определены документами системы (ПР 32.151-2000, П САЛНК 01, П САЛНК 04). Под лабораторией НК понимается как самостоятельное юридическое лицо или структурное подразделение предприятия (участок, бригада в депо, цех дефектоскопии дистанции пути, вагон-дефектоскоп и т. п.), так и рабочие места НК с персоналом (контрольный пост на РСП, рабочее место дефектоскописта в депо и т. п.).
Аккредитацию проводят Орган по аккредитации лабораторий НК на ж.-д. транспорте (Аттестат № РОСС RU.0001.550001), входящий в состав НК-Цент-ра, и уполномоченные им территориальные (дорожные) аудиторские организации. В качестве аудиторской организации зарегистрирована, в частности, Дорожная лаборатория дефектоскопии Службы пути Московской ж. д.
В соответствии с требованиями МПС России большое внимание уделяется аккредитации лабораторий НК предприятий, поставляющих продукцию для ж.-д. транспорта. Аккредитованы Служба НК Нижнетагильского металлургического комбината, производящего рельсовый прокат, бандажи и цельнокатаные колеса, и Отдел НК Уралвагонзавода, выпускающего оси колесных пар и вагоны различных типов.
Введение ССПНК ЖТ и САЛНК ЖТ - эффективное средство повышения надежности НК и установления таким образом действенного контроля за качеством технологических процессов эксплуатации и ремонта подвижного состава и рельсового пути, определяющих в целом безопасность движения поездов.
Литература
1. Герасимов ЮМ. Неразрушающий контроль и безопасность перевозочного процесса на железных дорогах России. - В мире НК. 1999. № 5. С. 14-15.
Источник - статья Г. Я. Дымкина опубликованная в журнале «В мире НК» № 2(48). 2010.
Другие статьи на тему аттестации специалистов и лабораторий неразрушающего контроля можно посмотреть в разделе Статьи.
Сертификация персонала НК в отрасли железнодорожного транспорта проводится с 1998 г. в рамках Системы добровольной сертификации персонала в области НК – ССПНК (зарегистрирована в системе Ростехрегулирования под ¹ РОСС RU.0001.04ЮА00 и перерегистрирована под ¹ РОСС RU.0001.03Н300) и в соответствии с отраслевым нормативным документом ПР 32.113-98 [1], введение которого отразило понимание в МПС России важной роли независимой проверки знаний и навыков работников, выполняющих НК, в обеспечении безопасности движения на железнодорожном транспорте.
Методическое руководство Системой сертификации персонала по НК объектов железнодорожного транспорта (ССПНК ЖТ) осуществляет «Отраслевой учебно-методический и аттестационный центр по неразрушающему контролю и диагностике технических объектов» (НК-Центр) – филиал ФГУП «Научно-исследовательский институт мостов и дефектоскопии Федерального агентства железнодорожного транспорта», который выполняет функции экспертной организации в области НК и ведет Реестр ССПНК ЖТ, включающий реестры уполномоченных органов, экзаменационных и учебных центров, признанных в ССПНК ЖТ, а также реестр сертифицированного персонала по НК.
Сертификацию по акустическому (А), магнитному (М), вихретоковому (Вт) видам и акустико-эмиссионному (АЭ) методу НК объектов железнодорожного пути и подвижного состава при их производстве, эксплуатации и ремонте проводят 11 уполномоченных органов и экзаменационных центров (табл. 1). За истекшие годы сертифицировано более 2640 специалистов по НК – работников ОАО «РЖД» и других предприятий всех форм собственности, выполняющих производство и ремонт технических средств железнодорожного транспорта: деталей и узлов вагонов (58,2 %), локомотивов (17,7 %), рельсов (22,4 %), сварных конструкций искусственных сооружений (1,7 %). Распределение сертифицированных специалистов по уровням квалификации и видам НК (рис. 1) подтверждают как общие для всех отраслей промышленности потребности в специалистах различного уровня, так и особенности железнодорожного транспорта и транспортного машиностроения.
Введение дополнительных «отраслевых» требований к процедурам сертификации, а также к органам по сертификации и учебным центрам по подготовке специалистов к сертификации способствовало обеспечению единого методического уровня и объективности оценки квалификации специалистов по НК ответственных объектов железнодорожного транспорта.
Как известно, ССПНК является лишь одной из нескольких систем добровольной сертификации персонала по НК (или «аттестации», что в отечественной практике, по существу, одно и то же), зарегистрированных и более или менее активно действующих в настоящее время в России.
Анализ международных норм, регулирующих сертификацию персонала по НК, зарубежного и отечественного опыта сертификации, а также более чем 10-летний опыт проведения сертификации на железнодорожном транспорте подтверждает многократно декларируемую всеми участниками процесса необходимость восстановления единой национальной системы сертификации персонала по НК.

Рис. 1. Распределение персонала по НК, сертифицированного в соответствии с ПР 32.113-98, по уровням квалификации (а): зеленый, оранжевый и синий цвета – I, II и III уровни соответственно; и по видам (методам) НК (б): синий, желтый, красный и фиолетовый цвета – акустический, вихрето-ковый, магнитный и акустико-эмиссионный контроль соответственно
Основой для объединения (взаимного признания) действующих систем могут, по нашему мнению, стать новые нормативные документы, гармонизированные с международными стандартами и устанавливающие единые процедуры сертификации, формы удостоверений, требования к кандидатам и методические основы проведения базовых и общих экзаменов по видам (методам) НК. Перечень производственных секторов должен отражать отраслевое деление объектов контроля, а содержание и процедуры проведения специальных и практических экзаменов должны соответствовать отраслевым требованиям. При этом удельный вес проверки знаний кандидата должен быть перенесен с общего на специальный экзамен, а основной упор при сертификации на I и II уровни сделан на практическом экзамене, проводящем-ся в экзаменационных центрах, осна-щенных большим количеством образцов объектов контроля.
Для реализации та-кого подхода должны быть решены соот-ветствующие научно-методические зада-чи – пересмотр программ сертификации по всем видам НК и производственным секторам и перечней экзаменационных вопросов с существенным увеличением их количества. Наконец, следует устано-вить и ввести в практику правила и про-цедуры экспертизы и признания органов сертификации персонала по НК отрасле-выми органами государственной власти, в необходимых случаях органами надзо-ра и работодателями – саморегулируе-мыми организациями, некоммерчески-ми партнерствами предприятий и т. п. Представляется, что модернизация системы сертификации персонала мо-жет проводиться одновременно с об-суждением и введением в России ново-го унифицированного государственного стандарта, касающегося квалификации и сертификации персонала по НК.
Табл. 1. Выписка из реестра Уполномоченных органов и Экзаменационных центров, признанных в ССПНК ЖТ
Наименование Уполномоченного органа (Экзаменационного центра) по сертификации | Вид НК |
Уполномоченные органы (УО) | |
УО НК-Центр (филиал НИИ мостов), Санкт-Петербург | А, М |
УО «Уральский центр аттестации», Екатеринбург | А, М, Вт, АЭ |
УО «Транссиб» при Сибирском государственном университете путей сообщения, г. Новосибирск | А, М, АЭ |
Дорожный УО при Омском государственном университете путей сообщения | А, Вт, М |
УО при Ижевском государственном техническом университете | А, М, АЭ |
Экзаменационные центры (ЭЦ) | |
ЭЦ по НК при Петербургском государственном университете путей сообщения | А, М |
ЭЦ по НК «Импульс» Дорожного центра обучения Восточно-Сибирской ж. д., г. Иркутск | А |
ЭЦ по НК «Сигнал» Красноярской ж. д., г. Красноярск | А, М |
ЭЦ «Технология» Дорожного центра обучения Забайкальской ж. д., г. Чита | А, М |
Дорожный ЭЦ «Юго-Восток НК» при Воронежском филиале РГОТУПС | А |
ЭЦ по НК на базе Челябинского института путей сообщения | А, Вт, М |
Обозначения. Виды (методы) НК: А – акустический, М – магнитный, Вт – вихретоковый, АЭ – акустико-эмиссионный
Литература
1. ПР 32.113-98. Правила сертификации спе-циалистов по неразрушающему контролю техни-ческих объектов железнодорожного транспорта
Источник - статья Н. П. Бирюковой опубликованная в журнале «В мире НК» № 2(48). 2010.
Другие статьи на тему аттестации специалистов и лабораторий неразрушающего контроля можно посмотреть в разделе Статьи.
Сертификация персонала в области НК и технического диагностирования, т. е. подтверждение соответствия знаний и профессионального опыта специалиста документально установленным требованиям, является общепризнанной как в России, так и за рубежом.
Процедура проведения сертификации (аттестации), требования к органам, ее организующим и проводящим, регламентированы международными стандартами ISO 17024, ISO 17021, EN-473, ISO-9712 и др., а также документами российских систем СДСПНК РОНКТД, ЕС ОС-CДА-13-2009, СДАНК-02-2020, которые разработаны с учетом основных положений перечисленных зарубежных стандартов.
Эти документы хорошо изучены и освоены российскими органами по аттестации персонала, и их работа осуществляется согласно их требованиям.
В последние годы освоены и реализованы требования по системе менеджмента качества в соответствии с требованиями ISO 9001 и др. Проверяющие и аккредитующие организации выполнению этих требований уделяют большое внимание.
Упомянутые документы в основном определяют организационные и процедурные требования. Проблем у органов по сертификации в этом направлении нет, все процедуры идентифицированы.
Научно-учебный центр «Качество» аккредитован по российским и международным стандартам практически по всем методам и промышленным секторам. Центр – единственный в России и странах СНГ – аккредитован на тепловой метод и метод течеискания по стандартам ЕN-473 и ISO-9712, на сектор «Авиация и космонавтика» по стандарту EN 4179 и директиве EASA AMC 145.A.30; единственный в стране и Европе аккредитован на право сертификации персонала оценки напряженно-деформированного состояния материалов и конструкций.
Одной из основных задач настоящего времени является обеспечение объективности, беспристрастности и достоверности в оценке соответствия установленным требованиям уровня компетентности специалиста по объему теоретических знаний и профессионального опыта. Основные критерии, которым надлежит соответствовать специалистам, определяются содержанием общего, специального и практического экзаменов.
Различные сборники вопросов и по количеству, и по содержанию, процедура приема экзамена, оснащенность лабораторных баз и подходов к проведению практических экзаменов, состав экзаменационных личных дел, состав и требования к экзаменационным образцам, – все это не регламентировано документами, и, следовательно, идентичность оценки компетентности и квалификационного уровня специалистов, проходящих аттестацию в различных органах по сертификации, не обеспечивается.
Ниже приводятся подходы к решению этих задач в Научно-учебном центре «Качество», опыт которого в области подготовки и сертификации специалистов более 15 лет.
Остановлюсь последовательно на каждой части квалификационного экзамена.
Общая ответственность за содержание, актуализацию, соответствие курса современному уровню технологии и техники в НУЦ «Качество» возложена на специально созданную «Комиссию по разработке и актуализации экзаменационных вопросов и образцов». Комиссия состоит из подкомиссий, которые по каждому методу НК включают 4 – 5 специалистов III уровня квалификации и преподавателей по соответствующему методу. Заседания комиссии проводятся не реже 1 раза в полугодие.
Общий экзамен
Сборник вопросов общего экзамена для каждого метода состоит из трех блоков вопросов на соответствие требованиям к знаниям для специалистов I, II и III уровней.
Каждый из сборников имеет 4 раздела:
I. Физические основы и параметры метода.
II. Приборы и средства контроля.
III. Основы технологии, схемы контроля.
IV. Несоответствия при изготовлении и эксплуатации. Выявляемость данным методом.
Каждый раздел сборника содержит одинаковое количество вопросов, расположенных в порядке возрастания сложности. На каждый вопрос предлагается четыре варианта ответа, один из которых верный.
Экзаменационные вопросы отражают современное состояние науки, методов, средств, технологии НК и нормативной документации. Уровень сложности разрабатываемых экзаменационных вопросов определен достаточным для проверки соответствия квалификации кандидата требованиям российских, европейских и международных стандартов по методу НК, уровню квалификации.
Содержание вопросов, определение по разделам, подтверждение степени сложности рассматриваются и утверждаются Комиссией по актуализации сборников вопросов. Количество вопросов в сборниках по общему экзамену не менее чем в два раза превышает минимально требуемое количество вопросов, регламентируемых документами СДАНК-02-2020, EN 473, ISO 9712 и EN 4179.
Специальный экзамен
Специальный экзамен отражает особенности условий контроля, характерные дефекты, требования к качеству, оптимальные схемы и параметры контроля, основные положения соответствующих данному виду объектов нормативных документов и т. п.
Сборники вопросов специального экзамена составляются по каждому производственному сектору (объекту).
Так, например, по УЗК разработано и используется 15 сборников вопросов специальных экзаменов плюс один сборник, обобщающий одинаковые требования ко всем объектам, контролируемым ультразвуковым методом. Аналогичное положение и по остальным методам.
Таким образом, мы имеем более 100 сборников вопросов специального экзамена по всем методам и производственным секторам, причем каждый из них на I, II, III уровни.
Такой банк экзаменационных вопросов специального экзамена позволяет убедиться, что специалист владеет не только физическими основами метода и технологией контроля по нему, но и знает особенности подлежащих контролю объектов, характерные дефекты и эффективные схемы их выявления.
Процесс сдачи экзаменов
Сдача кандидатами письменных экзаменов (общего и специального) проводится на компьютере, для объективности и непредвзятости процесса номера вопросов выбираются с использованием генератора случайных чисел. Компьютерная программа составлена таким образом, что:
– на экране отсутствуют номера вопросов, что исключает возможность использования формализации в ответах; – обеспечивается обязательный выбор вопросов из каждого раздела и каждого уровня сложности;
– обеспечивается возможность возврата к вопросу, ответ на который вызвал затруднения – по аналогии со сдачей экзамена без использования компьютера; – по окончании экзамена производится распечатка протокола результатов с фиксированием продолжительности экзамена; – на отдельном листке распечатывается текст вопросов, на которые были даны неверные ответы.
Такая система позволяет объективно и достоверно, в полном объеме оценить знание кандидатом физических основ и параметров метода по различным разделам и степени сложности, а также предоставляет возможность кандидату в дальнейшем обдумать вопросы, по которым у него не было достаточных знаний.
Актуализация сборников вопросов
Сборники вопросов не реже одного раза в полугодие подлежат актуализации.
Так как прием общих и специальных экзаменов в НУЦ «Качество» проводится с использованием компьютерной программы, все результаты экзаменов автоматически заносятся в электронную базу данных, что позволяет проводить статистический анализ результатов экзаменов в автоматическом режиме и упрощает процедуру актуализации. Результаты ответов на экзамене обрабатываются дополнительно за любой промежуток времени, при этом на протоколе отражаются:
– номера вопросов (общий перечень);
– число раз, когда выпадал данный вопрос;
– число правильных и неправильных ответов на конкретный вопрос.
По протоколу корректировке подлежат вопросы, 100 % ответов на которые были правильными, что свидетельствует о простоте вопроса или явной однозначности ответа, а также те вопросы, на которые дано менее 50 % правильных ответов, т. е. они либо некорректно сформулированы, либо не соответствуют требованиям программы данного квалификационного уровня.
– некорректность вопросов, выявленная по результатам ответов экзаменуемых;
– сложность, выявляемая по постоянным неправильным ответам; – однозначность ответов на вопрос;
– замечания и предложения экзаменаторов по содержанию вопросов; – необходимость включения новых вопросов в связи с введением новой нормативной документации;
– необходимость исключения вопросов, соответствующих нормативной документации, срок действия которой истек.
Решение по изменению принимает подкомиссия по актуализации по соответствующему методу, каждый раз оформляя это соответствующим протоколом, после чего соответствующие изменения вносятся в сборник экзаменационных вопросов.
Кроме экзаменационных вопросов в центре разработаны соответствующие сборники вопросов для стажировки, которые по содержанию близки к экзаменационным вопросам, однако вместо ответов в них содержатся ссылки на источник и номера страниц, где можно найти ответ. Таким образом обеспечиваются условия закрепления материалов перед экзаменом.
Практический экзамен
Этот экзамен состоит из трех частей: технологическая карта, контроль трех образцов, собеседование.
Технологическая карта
В нормативно-методические документы на НК конкретных объектов включены формы технологических карт, несколько отличающиеся друг от друга. Форма технологической карты, разработанная в нашем центре и предлагаемая кандидатам, включает все последовательные технологические операции контроля заданного объекта. Оформленная правильно, в соответствии с требованиями, технологическая карта подтверждает четкое знание всех этапов технологии контроля.
Кандидат заполняет две карты: одну – для стажировки, другую – экзаменационную на один из подлежащих контролю экзаменационных образцов.
Контроль экзаменационных образцов
В системе СДСПНК РОНКТД разработан документ 003.03.10 «Технические правила для органов по сертификации персонала в области НК», где представлены минимальные требования по типу и количеству приборов, средств, контрольных образцов для оснащения лабораторных баз практического экзамена по каждому методу. Лаборатория НК НУЦ «Качество» полностью соответствует требованиям указанного документа и насчитывает около 230 единиц оборудования. В этой части экзамена очень важно соблюдение технологии контроля, соблюдение условий контроля. С целью объективной независимой беспристрастной оценки практического экзамена разработана форма протокола оценки практического экзамена. Протокол состоит из 4-х частей:
– оценка знания приборов и средств;
– параметры и настройка режимов контроля;
– обнаружение и протоколирование не-сплошностей; – письменная инструкция (технологическая карта).
Каждая из частей включает несколько подпунктов, детализирующих данную часть процедуры.
Каждый пункт оценен в баллах, а также определены баллы снижения за каждую ошибку, допущенную кандидатом.
Экзаменаторы оценивают практическую работу независимо друг от друга; результаты представляются как среднее значение.
Собеседование
В заключение практического экзамена по российским нормам проходит собеседование, которое мы считаем очень эффективным мероприятием, т. к. это не только позволяет подтвердить письменные оценки квалификации специалиста, но создает условия его беседы с двумя специалистами III уровня и уточнения неясных для него вопросов.
Изложенная выше система по утверждению уровня квалификации специалиста документирована и способствует достоверности, объективности оценки знаний и практического опыта специалистов, а также обеспечивает меньшую степень зависимости результатов от того центра, в котором кандидат проходит сертификацию.
В этом случае, т. е. при соблюдении органами по сертификации одинаковых по содержанию и объемам экзаменационных материалов, идентичных по форме и содержанию процедур и протоколов организации и оценки уровня компетенции специалистов, отпадет необходимость в недоверии ряда ведомств к результатам сертификации и их предложении пройти повторную аттестацию в специально уполномоченных единичных центрах.
Эффективность описанного процесса подтверждается результатами обратной связи с заявителями, т. е. позитивными отзывами кандидатов и организаций.
Источник - статья Н. А. Быстровой, Д. И. Галкина, И. С. Хретинина опубликованная в журнале «В мире НК» № 2(48). 2010.
Другие статьи на тему аттестации специалистов и лабораторий неразрушающего контроля можно посмотреть в разделе Статьи.
Под сертификацией (аттестацией) специалистов НК подразумевается процедура подтверждения достаточности теоретической и практической подготовки, опыта, компетентности специалиста, т. е. его профессиональных знаний, навыков, мастерства, и предоставления права на выполнение работ по одному или нескольким видам (методам) НК [1]. Для осуществления сертификации применяются схемы сертификации – своеобразные фильтры, которые должны исключать возможность допуска к контролю потенциально опасных технических объектов специалистов, не обладающих достаточной квалификацией.
В настоящее время на территории РФ действуют несколько схем сертификации специалистов:
- на объектах, подведомственных Рос-технадзору, в соответствии с требованиями [1];
- объектах, подведомственных ОАО «Концерн Росэнергоатом», в соответствии с требованиями [2];
- на железнодорожном транспорте в соответствии с требованиями [3];
- на объектах ПАО «Транснефть» в соответствии с требованиями [4];
- в области авиации и космонавтики по российским и европейским нормам ([5, 6]);
- в области объектов Российского морского регистра судоходства (EN 473:2000, [5]);
- в соответствии с требованиями системы добровольной сертификации персонала НК [5];
- в соответствии с требованиями европейского стандарта [7].
Необходимость сертификации по той или иной схеме определяется видами объектов, на которых проводятся работы по НК. Необходимость проведения дополнительной аттестации в соответствии с требованиями [4] обусловлена наличием отраслевых требований к квалификации специалистов НК, допускаемых к выполнению работ на объектах ПАО «Транснефть» в части проведения, оценки и оформления результатов контроля. Процедуру дополнительной аттестации должны пройти специалисты НК для получения допуска к работе на объектах ПАО «Транснефть».
Последние две схемы сертификации являются полностью добровольными, и необходимость сертификации (аттестации) по этим системам диктуется заказчиком, т. е. относится к области договорных взаимоотношений. Так, например, трубы, изделия проката и другая продукция, изготавливаемая в РФ и поставляемая на территорию EC, должна быть проконтролирована в соответствии с требованиями европейских стандартов качества специалистами, сертифицированными согласно EN 473:2008
Параллельное развитие схем сертификации привело к отсутствию:
- единой терминологии по сертификации персонала;
- единых требований, предъявляемых к кандидату, для допуска к сертификации;
- единых требований к процедуре и порядку оценки квалификационного экзамена.
Табл. 1. Сравнение требований различных систем сертификации (аттестации)*
Критерий сравнения | Требования согласно | |||
[1] | [3] | [2] | [7] | |
Минимальные требования к стажу работы по данному методу НК | 18 мес. | 12 мес. | 36 мес. | 12 мес. |
Требования к состоянию здоровья и зрению | Медицинское заключение (справка) в соответствии с «Временным перечнем вредных, опасных веществ и производственных факторов, при работе с которыми обязательны предварительные и периодические осмотры работников …» | Отсутствие противопоказаний по состоянию здоровья и зрению. При сертификации по контролю маг-нитопорошковым методом – отсутствие дальтонизма | Медицинское заключение (справка) в соответствии с «Временным перечнем вредных, опасных веществ и производственных факторов, при работе с которыми обязательны предварительные и периодические осмотры работников …» | Чтение минимум таблицы Егера ¹ 1 или шрифта Times Rоmаn 4,5 одним или обоими глазами; возможность различать контраст между цветами или оттенками серого, используемыми в методе НК |
Минимальные сроки специальной подготовки | 120 ч | Требования отсутствуют. Подготовка должна проводиться в соответствии с программами, согласованными экспертной организацией по сертификации персонала НК | 120 ч | 144 ч |
Наличие собеседования | Да, по результатам практического экзамена | Да, по результатам общего экзамена | Да, по результатам теоретического экзамена | Нет |
Кандидат считается выдержавшим квалификационный экзамен, если: | суммарная оценка за экзамен не менее 80 %, но не менее 70 % по каждой части экзамена | оценка по каждой части экзамена не менее 80 % | суммарная оценка за экзамен не менее 80 %, но не менее 70 % по каждой части экзамена | оценка по каждой части экзамена не менее 70 % |
Срок действия квалификационного удостоверения | 3 года | 3 года | 3 года | 5 лет |
*на примере прямой (при отсутствии I уровня квалификации) сертификации на II квалификационный уровень по УЗК
Ошибка специалиста НК (дефекто-скописта, контролера), связанная с недостатком его квалификации, в равной степени недопустима на объектах, подведомственных Ростехнадзору, на железнодорожном транспорте, на объектах ОАО «Концерн Росэнергоатом». Очевидно, что пропуск дефекта на любом из этих объектов может привести к катастрофическим последствиям. Тогда непонятно: почему требования к квалификации специалистов НК, проводящих контроль этих объектов, различаются?
Для разрешения данного противоречия, на наш взгляд, необходимо привести существующие схемы сертификации к единой основе использования нормативных документов. В качестве базиса можно рассматривать СДАНК-02-2020. Данная схема сертификации также является наиболее апробированной, т. к. процедуру сертификации по СДАНК-02-2020 прошли по состоянию на начало 2010 г. более сорока тысяч специалистов НК.
Таким образом, опираясь на основные положения СДАНК-02-2020 и дорабатывая их в части вопросов, относящихся к отраслевой специфике, можно прийти к единообразию схем сертификации. Это позволит сделать всю систему сертификации в области НК более понятной, доступной и ориентированной, прежде всего, на потребителя услуг данного вида.
Кроме того, для обеспечения единообразия подходов при оценке результатов квалификационного экзамена должны быть разработаны и приняты во всех системах сертификации: – банк экзаменационных вопросов пофизическим основам методов НК; – требования к экзаменационным образцам (геометрическая форма, размеры, тип и максимальное количество дефектов) по различным методам НК в зависимости от отраслевой специфики; – методики оценки практического экзамена по различным методам НК; – порядок инспекционного контроля деятельности сертифицированного (аттестованного) специалиста.
Литература
1. СДАНК-02-2020. Правила аттестации персонала в области неразрушающего контроля. Утверждены постановлением Госгортехнадзо-ра России от 23 января 2002 г. ¹ 3. Зарегистрировано в Минюсте РФ 17 апреля 2002 г. Рег. ¹ 3378.
2. Порядок аттестации контролеров, выполняющих контроль металла на предприятиях ОАО «Концерн Росэнергоатом». Утв. 01.03.2010 г. Зам. Ген. директора ОАО «Концерн Росэнергоатом» – директором по производству и эксплуатации АЭС.
3. ПР 32.113 – 98. Правила сертификации персонала по неразрушающему контролю технических объектов железнодорожного транспорта. – М.: МПС России, 1998.
4. ОР-03.120.00-КТН-071-09. Требования к аттестации специалистов неразрушающе-го контроля, выполняющих работы на объектах ПАО «Транснефть».
5. СДСПНК РОНКТД (Система добровольной сертификации персонала неразрушающего контроля Российского общества по неразрушающе-му контролю и технической диагностике).
6. EN 4179. Авиация и космонавтика. Квалификация и допуск персонала неразрушающего контроля.
7. EN 473:2008. Квалификация и сертификация персонала неразрушающего контроля. Общие принципы.
Источник - статья С. А. Попоудина опубликованная в журнале «В мире НК» № 3(37). 2007.
Другие статьи на тему толщинометрии изделий можно посмотреть в разделе Статьи.
Ультразвуковая толщинометрия (УЗТ) находит широкое применение во многих отраслях народного хозяйства.
УЗТ позволяет оценивать толщину изделий в процессе производства и эксплуатации, а также выявлять расслоения в материале изделий.
В настоящее время, в связи с возросшими требованиями к точности проводимых измерений, на смену аналоговым ультразвуковым толщиномерам приходит аппаратура на основе микропроцессоров [1] с представлением информации на дисплее в виде А-развертки и В-развертки, с дополнительной информацией о фазе отраженного сигнала.
За последние десять лет в Беларуси, благодаря большой информационно-методической работе Белорусской ассоциации НК и технической диагностики (БАНК и ТД) и при ее содействии интенсивно идет замена морально и физически устаревших средств НК, в том числе и ультразвуковых толщиномеров.
Качество выполнения УЗТ зависит прежде всего от наличия и технического уровня технических нормативных правовых актов (ТНПА).
В странах СНГ в области УЗТ на сегодняшний день действуют ТНПА, которые разрабатывались более тридцати лет назад и не потеряли своей актуальности, а также разрабатываются новые документы и вводятся в качестве государственных международные и европейские стандарты. В общем случае, применительно к УЗТ, так же как и ко всем методам НК, стандарты можно разделить на следующие группы.
1. Термины и определения:
– ГОСТ 23829-85. Контроль неразруша-ющий акустический. Термины и определения.
– *СТБ ЕН 1330-4-2004. Контроль нераз-рушающий. Часть 4. Термины, применяемые при ультразвуковом контроле.
-----------------
* СТБ – Государственный стандарт Республики Беларусь.
2. Технические требования к СНК и методам контроля (включая требования к точности измерений):
– ГОСТ 18353-79. Контроль неразрушаю-щий. Классификация видов и методов.
– ГОСТ 20415-82. Контроль неразруша-ющий. Методы акустические. Общие положения.
– ГОСТ 28702-90. Контроль неразруша-ющий. Толщиномеры ультразвуковые. Общие технические требования.
– СТБ ЕН 583-2-2005. Контроль нераз-рушающий. Ультразвуковой метод. Часть 2. Настройка чувствительности и длительности развертки.
– СТБ ИСО/МЭК 17025-2001. Общие требования к компетентности испытательных и калибровочных лабораторий.
– ГОСТ 8.010-99. Государственная система обеспечения единства измерений. Методики выполнения измерений. Основные положения.
– СТБ ИСО 5725. Точность (правильность и прецизионность) методов и результатов измерений, части 1–6.
3. Метрологическое обеспечение СНК:
– ПМГ 06-2001. Порядок признания результатов испытаний и утверждения типа, поверки, метрологической аттестации средств измерений.
– ГОСТ 8.495-83. Толщиномеры ультразвуковые контактные. Методы и средства поверки.
Кроме перечисленных ТНПА в странах СНГ действуют нормативные документы (РД, ОСТ, ВСН, СНиП) по УЗТ различных объектов, например [2] и [3].
Опуская детальный анализ недостатков и взаимной несогласованности перечисленных ТНПА, остановимся на стандарте ЕN 14127 «Неразрушающий контроль. Ультразвуковые измерения толщины» [7], который был введен в действие в августе 2004 г. С февраля 2005 г. в странах Евросоюза он действует как национальный.
Рис. 1. Методы проведения измерений толщины ультразвуковым методом.
Согласно стандарту ЕN 14127:2004 оценка точности измерений выражается в виде неопределенности результатаизмерения. Оценка неопределенности измерений проводится в соответствии с ISO 14253-2 [8] «Спецификации на Геометрические Параметры Изделий (GPS) – Инспекция путем измерения рабочих заготовок и измерительного оборудования. Часть 2. Руководство по оценке неопределенности при измерениях GPS, при калибровке измерительного инструмента, а также верификации продукции», положения которого позволяют определить, когда результат измерения можно считать соответствующим показанию прибора. Стандарт ISO 14253-2 представляет интерес при рассмотрении процедуры по планированию и использованию неопределенности и, конечно же, требует отдельного рассмотрения.
Стандарт ЕN 14127:2004 устанавливает:
– основные требования к ультразвуковому методу измерения толщины;
– методы проведения измерения толщины (рис. 1);
– типы применяемой аппаратуры для проведения измерений;
– требования к квалификации персонала;
– факторы, влияющие на точность измерений (табл. 1);
– выбор аппаратуры, порядок настройки аппаратуры с цифровой индикацией и имеющей экран с А-разверткой;
- порядок и особенности технологии проведения измерений;
- оценку точности;
- составление отчета.
В стандарте ЕN 14127:2004 приводятся информативные приложения в виде таблиц и схем:
- возможные виды коррозии сосудов и трубопроводов;
– особенности настройки аппаратуры;
– учет параметров, влияющих на точность измерений;
– схемы проведения контроля с учетом особенностей при проведении измерений в процессе производства или эксплуатации с рекомендациями по выбору аппаратуры и др.
Исходя из содержания рассматриваемого стандарта, можно сказать о том, что он достаточно полно раскрывает особенности УЗТ и может служить в качестве основы для совершенствования и разработки ТНПА.
В соответствии с ЕN 14127:2004 специалист, выполняющий УЗТ, должен знать физические основы ультразвука, а также иметь теоретические и практические навыки измерения толщины ультразвуковым методом. Кроме этого, оператор должен иметь информацию о конструкции объекта контроля и его материале, особенностях эксплуатации, возможном состоянии его обратной поверхности. В качестве подтверждения своей квалификации специалист должен иметь сертификат в соответствии со стандартом EN 473 или его эквивалентом.
Точность проведения измерений с помощью ультразвука – это тот важный момент, который выделяет УЗТ из области дефектоскопии и должен быть учтен при подготовке специалистов, проводящих ультразвуковые измерения толщины. Специалист должен знать, с какой точностью он должен выполнять измерения и как ее добиться при проведении измерений. Практика показывает, что персонал, имеющий сертификат по ультразвуковой дефектоскопии, в курс обучения которого не входила углубленная подготовка по обеспечению точности проведения измерений ультразвуковым методом, не сможет качественно выполнить задачу, связанную с оценкой остаточной толщины изделия в процессе эксплуатации. Очевидно, что сертификация специалистов для этого направления весьма актуальна [9].
Выводы:
1. Ввести в качестве межгосударственного стандарта европейский стандарт ЕN 14127:2004. Эту работу мог бы взять на себя межгосударственный комитет по НК МТК 515 «Неразрушающий контроль».
2. Ввести сертификацию персонала по ультразвуковой толщинометрии, для чего разработать программы подготовки специалистов для целей сертификации, схемы сертификации, экзаменационные вопросы и т. д.
Литература
1. Гиллер Г. А., Могильнер Л. Ю. Современные ультразвуковые толщиномеры. Новые возможности. – «В мире НК». 1999. № 5. С. 6–9.
2. ПНАЭ Г 7-031-91. Унифицированные методики контроля основных материалов (полуфабрикатов), сварных соединений и наплавки оборудования и трубопроводов атомных энергетических установок. Ультразвуковой контроль. Часть ІІІ. Измерение толщины монометаллов, биметаллов и антикоррозионных покрытий. – М.: ЦНИИ атоминформ, 1992.
3. РД РОСЭК 006-97. Машины грузоподъемные. Толщинометрия ультразвуковая. Основные положения. – М.: Машиностроение, 1998.
4. Руководство по выражению неопределенности измерения. Перевод с англ. Под науч. ред. проф. Слаева В. А. – СПб.: ГП ВНИИМ им. Д. И. Менделеева, 1999.
5. СТБ ИСО 5725-1-2002. Точность (правильность и прецизионность) методов и результатов измерений. Часть 1. Общие принципы и определения. – Минск: БелГИСС, 2002.
6. Руководство ЕВРАХИМ/СИТАК. Количественное описание неопределенности в аналитических измерениях. 2-е издание, 2000, перевод с англ. Р. Л. Кадиса, Г. Р. Нежиховского, В. Б. Силенка под общей редакцией Л. А. Конопелько. – СПб.: ВНИИМ им. Д. И. Менделеева, 2002.
7. ЕN 14127:2004 (Е). Non-Destructive Testing – Ultrasonic Thickness Measurement.
8. ISO/TS 14253-2:1999(E) Geometrical Product Specifications (GPS) – Inspection by Measurement of Workpieces and Measuring Equipment – Part 2: Guide to Estimation of Uncertainty in GPS Measurement, in Calibration of Measuring Equipment and in Product Verification.
9. Попоудина С. А. Развитие системы сертификации персонала в области НК в Республике Беларусь. – В мире НК. 2005. № 4(30). С. 54–55.
Табл. 1. Таблица параметров, влияющих на точность измерений
Основные области | Параметры | Результат | |
Объект контроля | Материал | Химический состав | Ослабление, поглощение, рассеяние и местные вариации скорости |
Структура | |||
Анизотропия | |||
Состояние поверхности |
Отсутствие загрязнений |
Локальные изменения состояния поверхности ведут к местным вариациям скорости | |
Шероховатость | |||
Профиль поверхности | |||
Покрытие | Покрытие | Скорость распространения ультразвука в покрытии отличается от скорости ультразвука в основном материале, что является результатом неточности | |
Лакокрасочное | |||
Обработка поверхности | |||
Геометрические параметры | Непараллельность | Исчезновение отраженного сигнала или его искажение | |
Криволинейность | Снижение эффективности контактной смазки | ||
Измеряемый диапазон | Искажение, искривление отраженного сигнала вследствие ослабления | ||
Настройка для проведения измерений | Метод калибровки | Неопределенность метода калибровки | Неопределенность показаний прибора |
Reference блок или стандартный образец предприятия (СОП) | Неопределенность, связанная с толщиной и скоростью | Точность не может быть выше той, которая связана с неопределенностью Reference блока или СОП | |
Проведение измерений | Оборудование | Точность измерений | Точность выполненных измерений не может быть выше точности аппаратуры |
Длина кабеля | Излишняя длина кабеля причина искажения сигналов | ||
Колебание параметров аппаратуры | Неточность показаний прибора | ||
Временной путь ультразвука |
Точность выполненных измерений не может быть выше точности измерения временного пути ультразвука |
||
Линейность | Неточность показаний прибора | ||
Точка отсчета | Неточность показаний прибора | ||
Операция | V-образный путь | Неверные показания, имеющие связь с путем ультразвука в материале изделия и его толщиной | |
Изменение фазы | Ошибочные показания | ||
Повторяемость | Составные части | Метод | Неправильные действия |
Контактная смазка | Плохая контактная смазка способствует отсутствию стабильности показаний | ||
Подготовка специалиста | Ошибочное толкование | ||
Прочее | Температура | Вариации скорости ультразвука | Ошибочное толкование |
Источник - статья А. К. Гурвича опубликованная в журнале «В мире НК» № 2(40). 2008.
Другие статьи на тему толщинометрии изделий можно посмотреть в разделе Статьи.
Материал подготовили А. К. Гурвич, В. А. Сясько, Б. В. Артемьев, А. Я. Грудский, Ю. К. Федосенко, В. Г. Шевалдыкин с учетом действующих ГОСТ, ряд из которых требует пересмотра.
Авторы полагают, что первая редакция данной таблицы будет развита и дополнена читателями журнала. Файл с таблицей может быть выслан редакцией журнала для корректировки по запросу читателей в июле-августе этого года.
---------------
*ПЭП - пьезоэлектрический преобразователь; ЭМАП - электромагнитно-акустический преобразователь; АР - антенная решетка
Источник - статья Е. Ф. Кретова опубликованная в журнале «В мире НК» № 2(40). 2008.
Другие статьи на тему толщинометрии изделий можно посмотреть в разделе Статьи.
Как правило, ультразвуковой метод измерения толщины применяют в таких местах металлоконструкций, которые недоступны или труднодоступны для измерения механическим измерительным инструментом. Особенно широко этот метод используют для определения толщины стенок труб, котлов, сосудов, то есть объектов замкнутого типа или с односторонним доступом. Обычно измерения производят на эквидистантных (равноудаленных друг от друга) поверхностях или участках поверхности, хотя принципиально возможны измерения и в других случаях.
По физическим принципам, используемым для измерения толщины, акустические толщиномеры делят на эхо-импульсные и резонансные. Принцип ультразвуковой толщинометрии импульсными приборами основан на измерении времени прохождения ультразвукового импульса в изделии или в слое и умножении измеренного времени на коэффициент, учитывающий скорость звука в материале изделия. В резонансных приборах для измерения толщины используется локальный резонансный метод или локальный метод свободных колебаний, а также интерференционные явления, возникающие при распространении акустических волн в изделии.
Резонансный метод позволяет измерять толщину от минимального значения
hmin= 0,5с/fmax
где с - скорость звука в материале изделия; fmax - максимальная частота прибора [1].
При повышении частоты до 30 МГц можно измерять толщины стальных изделий, начиная с 0,1 мм. Измерение таких толщин эхо-методом выполнить не удается. Использование иммерсионного варианта метода обеспечивает непрерывный контроль труб диаметром 3-^4 мм и более, что также трудно обеспечить другими методами; погрешность составляет при этом 1-^2%. Резонансный метод применяют для контроля изделий с гладкими поверхностями. Изменение толщины в зоне измерения не должно превышать 8 %, при этом измеряется средняя толщина, а не наименьшее ее значение. Этими возможностями определена область преимущественного использования резонансных толщиномеров для измерения толщины при автоматическом контроле тонкостенных труб малого диаметра в иммерсионном варианте. В остальной области повсеместно применяют ультразвуковые эхо-импульсные толщиномеры - простые в управлении и компактные приборы, позволяющие с хорошей точностью измерять толщину > 0,5 мм.
Долгое время измерение толщины ультразвуковым эхо-методом воспринималось со стороны такой же простой операцией, как измерение линейкой. Действительно: поставили искатель в указанную точку на изделии и считали результат. При использовании толщиномеров в лучшем случае руководствовались инструкцией по эксплуатации прибора. Первый отраслевой стандарт в этой области [2] (далее - ОСТ), распространяющийся на изделия судовой техники, появился в 1985 г., то есть существенно позже стандартов (инструкций) по ультразвуковому контролю сплошности материалов и сварных соединений. В1992 г. введен в действие отраслевой методический документ по толщинометрии в атомной энергетике [3] (далее - ПНАЭ), а в 1998 г. - методика измерения толщины элементов грузоподъемных машин [4] (далее - РД РОСЭК). Рассмотрим основные положения технологии ультразвуковой толщинометрии на основе этих трех документов.
Общие положения
В стандартах отмечается, что толщинометрия способом однократных измерений применяется в местах, недоступных для измерения механическим измерительным инструментом. Ее выполняют при изготовлении изделий, их эксплуатации, техническом диагностировании и экспертном обследовании. Измерения выполняют дискретно в запланированных точках на ОК. Необходимость проведения измерений толщины ультразвуковым методом, объем измерений, конкретные точки для измерений и критерии оценки результатов должны быть оговорены в производственно-конструкторской документации.
Современные толщиномеры позволяют производить сплошное (непрерывное) измерение толщины с сигнализацией (или регистрацией) выхода измеряемой толщины за указанные пределы. Однако технология такого контроля в рассматриваемых документах не предусмотрена.
ОСТ и ПНАЭ не ограничивают диапазон измеряемых толщин. РД ограничивает измеряемые толщины диапазоном 2,5 - 60,0 мм. Это ограничение связано с толщинами реально существующих элементов грузоподъемных машин.
Рис. 1. Стандартный образец предприятия для настройки дефектоскопа при измерении толщины антикоррозионной наплавки
ОСТ и РД РОСЭК регламентируют измерение толщины монометаллических элементов, область применения ПНАЭ распространяется дополнительно на биметаллические изделия, а также на антикоррозионные покрытия из сталей аустенитного класса на изделиях из сталей перлитного класса.
К работе по измерению толщины допускаются дефектоскописты, аттестованные по правилам, действующим в соответствующей отрасли, и изучившие отраслевой стандарт по толщино-метрии. Руководство работами по измерению толщины, периодическая проверка качества его исполнения и оформление заключений по его результатам возлагается на инженерно-технических работников в соответствии с правилами, действующими в отрасли.
Средства контроля
РД РОСЭК регламентирует для целей толщинометрии применение ультразвуковых толщиномеров с цифровой или стрелочной индикацией результатов. Как известно, в функциональной схеме толщиномера реализуются дополнительные относительно дефектоскопа блоки, позволяющие повысить точность измерений (например, автоматическая регулировка усиления для стабилизации амплитуды первого донного сигнала) или дополнительные требования к блокам (короткий и крутой зондирующий импульс, широкополосность) [5]. Поэтому применение толщиномеров при контроле толщин примерно до 100 мм более оправдано, чем дефектоскопов. Однако при толщинах элементов более 100 мм, которые встречаются в судовых конструкциях и характерны для оборудования атомных электростанций (АЭС), чувствительности толщиномеров не всегда достаточно, а измерение толщины антикоррозионных покрытий вообще возможно только дефектоскопом. Поэтому ультразвуковые дефектоскопы включены в состав средств измерения толщины в методиках ОСТ и ПНАЭ.
При использовании толщиномеров следует применять пьезоэлектрические преобразователи (ПЭП), которые входят в комплект толщиномера. Чаще всего это прямые раздельно-совмещенные (PC) ПЭП, иногда применяют прямые совмещенные ПЭП сзадержкой. Взависимости от измеряемой толщины используют ПЭП с частотой из диапазона 2,0 - 10,0 МГц. При измерении толщины монометаллов и биметаллов дефектоскопами используют прямые совмещенные ПЭП с жестким протектором. Толщину антикоррозионного покрытия измеряют прямыми совмещенными (со стороны основного металла) или PC ПЭП (со стороны покрытия). Используют частоты 2,0 - 5,0 МГц.
Для настройки прибора применяют стандартные образцы предприятия (СОП), изготовленные из материала ОК. Основные требования к СОП: воспроизведение скорости звука, формы и состояния поверхности соответствующим параметрам ОК. Так, например, если ставится задача измерения толщины объекта с лакокрасочным покрытием, образец должен иметь покрытие, выполненное по такой же технологии. В тех случаях, когда ОК имеет малый радиус кривизны (менее 50 мм), сложную криволинейную форму поверхности (гибытруб), необходимо применять СОП в виде фрагментов соответствующих изделий. Обычно рекомендуют иметь СОП со ступенями минимально и максимально допустимой толщины. Пример СОП для измерения толщины антикоррозионной наплавки приведен на рис. 1.
Средства контроля должны быть паспортизованы и проходить поверку в установленном порядке.
Подготовка к контролю
Перед проведением измерений необходимо произвести настройку прибора. Конкретные способы настройки для каждого прибора определены инструкцией по эксплуатации, однако они всегда содержат две операции: настройка нуля (т.е. момента входа ультразвукового импульса в ОК) и настройка на скорость звука в ОК. Настройка нуля в современных толщиномерах может быть выполнена без применения внешних образцов. Настройку на скорость звука в ОК осуществляют по СОП. Точность настройки проверяют по нижней и верхней границам диапазона измерений.
Для измерения толщины монометалла или биметалла подготавливают площадку размером 30x30 мм2 с центром в точке измерения. В случае измерения толщины наплавки готовят площадку размером 50x50 мм2. Больший размер площадки связан с тем, что не в каждой точке ОК можно получить отчетливый эхо-сигнал от зоны сплавления основного металла с наплавкой. Иногда для этого требуется произвести небольшие перемещения ПЭП около намеченной точки измерения. Подготовленная площадка должна быть свободна от загрязнений, отслаивающейся окалины или краски. Шероховатость поверхности со стороны ввода ультразвуковых колебаний должна быть R < 6,3 мкм по ГОСТ 2789-73.
Чем более точно необходимо произвести измерение, тем более жесткие требования предъявляются к состоянию обеих поверхностей ОК. Нетсмысла требовать погрешность измерения 8 < 0,1 мм на объекте с корродированной поверхностью.
При измерении толщины на участках удаления поверхностных дефектов для установки ПЭП должна быть подготовлена площадка диаметром 15 мм, параллельная поверхности изделия. Преобразовательдолжен плотно прилегать к поверхности изделия. В некоторых случаях измерение может быть выполнено со стороны, противоположной выборке. Если выборка имеет крутой профиль, не позволяющий обеспечить плоскую площадку для установки ПЭП, измеряют толщину в точках вокруг выборки. Глубину выборки измеряют микрометрическим или индикаторным глубиномером. Толщину в месте выборки находят как разность между минимальной толщиной в окрестности выборки и глубиной выборки.
В соответствии с ПНАЭ температура окружающего воздуха и ОК должна находиться в пределах 5 - 40 "С. ОСТ и РД РОСЭК позволяют выполнять измерения в диапазоне температур, разрешенном инструкцией по эксплуатации применяемого толщиномера. По данным американской спецификации SE-797 каждое увеличение температуры на 55 °С влечет за собой уменьшение скорости звука в стали на 1% [6].
Проведение измерений
Перед началом измерений необходимо ознакомиться с документацией на измеряемый объект и, если возможно, составить представление об ожидаемом состоянии донной поверхности.
На каждый размеченный участок наносят контактную жидкость, устанавливают ПЭП и тщательно притирают к поверхности ОК, добиваясь минимального устойчивого показания. При измерении толщины трубопроводов экран PC ПЭП должен быть ориентирован перпендикулярно образующей трубы. Причиной отсутствия показаний могут быть плохой акустический контакт (например, из-за плохого качества контактной поверхности), язвенная коррозия донной поверхности, отсутствие эквидистантности поверхностей, наличие элемента, приваренного к донной поверхности, наличие внутреннего дефекта материала в месте измерения и др.
При измерении толщины ультразвуковыми дефектоскопами следует проводить и настройку, и измерение в режиме «по фронту». Для уменьшения погрешности настройку и измерение необходимо выполнять при одинаковой высоте эхо-сигнала.
При измерении толщины в местах язвенной и пятнистой поверхности коррозии внутренней поверхности прибор фиксирует отдельные язвины сферической формы размером более 2,5 ч- 3,0 мм. Для определения участка наименьшей толщины приходится выполнять измерения с малым шагом (до Змм и меньше). О наличии пятнистой или язвенной коррозии говорят скачущие показания прибора на небольшом участке измерений.
Считывание результата измерения проводят после получения устойчивого и достоверного показания. Для цифрового прибора оно характеризуется либо одним значением, либо двумя, изменяющимися в пределах дискретности прибора. В последнем случае записывают значение, ближайшее к границе допуска на размер. Если возникает сомнение в правильности показаний толщиномера, участок измерения целесообразно проверить дефектоскопом.
Возможность измерения толщины антикоррозионной наплавки основана на том, что акустические сопротивления основного металла и антикоррозионной наплавки несколько отличаются (z1 = 4,6 х 107 кг-м~2/с; z2 = 4,2 х 107 кгм~2/с), следовательно, на границе сплавления образуется отраженная ультразвуковая волна, которая регистрируется ультразвуковым дефектоскопом. При измерении со стороны основного металла толщина наплавки рассчитывается как разность показаний полной толщины объекта и толщины основного металла (рис. 2).
Рис. 2. Схема измерения толщины антикоррозионной наплавки со стороны основного металла
Измерение со стороны наплавки усложняется тем, что материал наплавки представляет собой литую аустенитную крупнозернистую структуру. Поскольку коэффициент отражения от границы раздела наплавка-основной металл довольно мал (расчетный коэффициентбез учета диффузного рассеяния Rp = 0,035), требуется установить высокую чувствительность для получения сигнала от границы сплавления. При этом может оказаться, что структурный шум из объема наплавки не позволит выявить сигнал от зоны сплавления. Для оптимизации измерения в этом случае выбирают такой PC ПЭП, у которого фокусное расстояние больше толщины наплавки (рис. 3).
Рис. 3. Схема к выбору PC ПЭП для измерения толщины наплавки со стороны наплавки: А-амплитуда сигнала от отражателя в виде плоскости; r - расстояние от поверхности ввода до отражателя
При этом оказывается, что чувствительность ПЭП в области зоны сплавления всегда выше, чем в материале наплавки, следовательно, можно ожидать, что уровень структурных шумов позволит выделить сигнал от зоны сплавления.
Ошибки измерений
При измерениях могут возникать ошибки трех видов.
Грубыми называют такие ошибки (промахи), при которых получают результат, существенно отличающийся от ожидаемого в данных условиях. Для надежного выявления промаха нужно либо повторить измерение спустя некоторое время, когда контролер уже «забыл» полученный им результат, либо произвести независимое повторное измерение, начиная с настройки прибора, другим контролером. Иногда промах можно легко выявить при беглом просмотре результатов измерений, если какой-то результат явно выпадает из общего ряда.
Систематические - это такие ошибки, величина которых одинакова или закономерно изменяется во всех измерениях, проводимых одним и тем же методом с помощью одних и техже приборов. При ультразвуковой толщинометрии такая ошибка возникает при неправильной настройке задержки нуля или скорости ультразвука.
Указанные два вида ошибок можно минимизировать путем тщательной настройки прибора и внимательном и аккуратном проведении измерений и записи результатов. Наиболее сложно уменьшать величину случайных ошибок, которые изменяются случайным образом при повторных измерениях одной и той же величины. Случайные ошибки возникают из-за:
- колебаний технических параметров в допустимых пределах;
- смещения ПЭП при повторных его установках в точку измерения;
- колебания толщины прослойки контактной жидкости из-за неравномерного прижима ПЭП к изделию;
- срабатывания прибора по разным периодам колебаний в радиоимпульсе;
- других факторов.
Величину случайной ошибки можно уменьшить путем проведения многократных (3-5) измерений в одной точке. Погрешность измерений определяется преимущественно случайными ошибками. Экспериментальное определение погрешности измерений основано на статистической обработке многократных измерений в нескольких точках и сравнении результатов измерений с действительной толщиной [2]. В общем случае погрешность измерений в машиностроении принимают равной +(-) 0,2 мм при измеряемой толщине Н до 20 мм и 0,01Н при толщине более 20 мм. Для дальнейшего уменьшения погрешности измерений следует:
- проводить измерение при отношении максимального к минимальному значению толщин не более 2;
- использовать для настройки две ступени СОП из материала ОК: одну - с максимальной, вторую - с минимальной допустимой толщиной;
- производить настройку прибора по точке ОК, в которой известно точное значение толщины.
При этих условиях можно добиться погрешности измерений, равной дискретности показаний прибора.
Погрешность измерения толщины антикоррозионной наплавки связана не с техническими параметрами прибора или технологическими особенностями процесса измерения, а с колебаниями положения зоны сплавления в пределах падающего на нее пучка ультразвуковых колебаний, другими словами - с технологией выполнения самой наплавки. Установленная погрешность измерений толщины антикоррозионной наплавки, выполненной ленточными электродами, составляет +(-) 1,0 мм [3].
Форма записи результата измерений
Результат измерений должен быть представлен в виде:
x, d от dн до dв; Р, где х, мм - номинальное значение результата измерения; dн, dв - нижний и верхний пределы погрешности измерения; Р - вероятность, с которой погрешность находится в этих границах.
Пример: 22,3 мм +(-) 0,2 мм; Р = 0,972.
Значение доверительной вероятности допускается не указывать, если Р = 0,95.
При оформлении результатов нескольких измерений, выполненных в одинаковых условиях и имеющих одинаковые показатели точности (d и Р), их указывают один раз для всех результатов измерений.
Литература
1. Ермолов И. Н., Ланге Ю. В. Ультразвуковой контроль. - В кн.: Неразрушающий контроль/ Справочник// Под общ. ред. В. В. Клюева. Т. 3.
- М.: Машиностроение, 2004. - 864 с.
2. ОСТ 5Р.5550-85. Отраслевой стандарт. Контроль неразрушающий. Полуфабрикаты и изделия металлические. Ультразвуковой метод измерения толщины. - М.: Изд-во стандартов, 1985.
3. ПНАЭ Г-7-031-91. Унифицированные методики контроля основных материалов (полуфабрикатов), сварных соединений и наплавки оборудования и трубопроводов атомных энергетических установок. Ультразвуковой контроль. Часть III. Измерение толщины монометаллов, биметаллов и антикоррозионных покрытий. - М.: ЦНИИатом-информ, 1992. Не действует - Не подлежит применению.
4. РД РОСЭК-006-97. М. Машины грузоподъемные. Конструкции металлические. Толщино-метрия ультразвуковая. Основные положения.
- М.: Машиностроение, 1998.
5. Алешин Н. П. и др. Методы акустического контроля металлов. - М.: Машиностроение, 1989. - 456 с.
6.ASME Code, секция V, раздел V, статья 23, спецификация SE-797. Типовая методика измерения толщины ручным ультразвуковым эхо-импульсным методом.
Аттестация персонала, выполняющего контроль качества оборудования и трубопроводов на действующих АЭС
Источник - статья В. Н. Ловчева опубликованная в журнале «В мире НК» № 2(48). 2010.
Другие статьи на тему аттестации специалистов и лабораторий неразрушающего контроля можно посмотреть в разделе Статьи.
Вопросам подготовки и аттестации специалистов по неразрушающим и разрушающим (лабораторным) методам контроля оборудования и трубопроводов в атомной энергетике уделяется большое внимание. В первую очередь это связано с пониманием опасности потенциальных последствий, связанных с аварийными ситуациями в атомной энергетике.
В 1970-х гг. Национальный аттестационный комитет (НАК) инициировал разработку первых общесоюзных документов по обучению и аттестации специалистов по НК объектов, подконтрольных Госгортехнадзору России.
В атомной отрасли еще до образования НАК с 1960-х гг. уже действовала система подготовки и аттестации специалистов на базе ведущих отраслевых институтов (ЦНИИ «Прометей», НПО «НИКИМТ», НПО «ЦНИИТМАШ»), работающих по проблематике атомной отрасли.
В этих организациях с учетом отечественного и международного опыта были разработаны типовые и специальные программы по теоретической и практической подготовке и аттестации работников, занятых контролем качества сварных соединений и основного металла. Одновременно был разработан порядок аттестации, предусматривающий допуск их к работе с правом выдачи заключений о качестве продукции (СПВЗ) и без права выдачи заключений (БПВЗ). Наиболее квалифицированные специалисты СПВЗ проходили аттестацию в качестве членов аттестационной комиссии.
Комплект этих документов утверждался на уровне Министерств и Главных управлений, приказами по которым полномочия Головных отраслевых ма-териаловедческих организаций, впоследствии Головных материаловедче-ских организаций (ГМО), были даны указанным выше ЦНИИ «Прометей», НПО «НИКИМТ» и «ЦНИИТМАШ». Документы по аттестации персонала согласовывались соответствующими надзорными органами.
Такая система подготовки и аттестации персонала имела как положительные, так и отрицательные стороны.
Положительной стороной можно считать наличие в ГМО высококвалифицированных специалистов, знающих специфику атомной энергетики, а также научно-производственной инфраструктуры, на базе которой проходила подготовка и аттестация персонала, что в условиях жесткой централизованной системы управления позволяло обеспечивать компетентное и ответственное выполнение данных работ.
Очевидный недостаток такой системы – консервативность и узковедомственные возможности, недостаточно учитывающие передовой отечественный и международный опыт.
Отечественные «Правила аттестации персонала в области неразрушающего контроля» (СДАНК-02-2020) [1], которые были разработаны на базе Европейских правил аттестации персонала ЕN 473, соответствуют Концепции управления Системой НК [2].
Система НК – совокупность участников, которые в рамках регламентирующих норм, правил, методик, условий, критериев и процедур осуществляют деятельность в области одного из видов экспертизы промышленной безопасности, связанной с применением НК
В Системе НК аттестация персонала является одним из ее элементов наряду с аттестацией лабораторий, методических документов и средств НК. Следует отметить, что в Системе НК разработан взаимосвязанный комплекс документов, регламентирующих основные вопросы, входящие в ее компетенцию. В настоящее время основным документом по аттестации персонала по НК в атомной энергетике являются ПНАЭ Г-7-010-89 [3]. Этот документ содержит раздел «Аттестация контролеров», согласно которому «аттестация контролеров (специалистов, дефектоскопистов, лаборантов ОТК, непосредственно выполняющих контроль) осуществляется путем проверки их теоретических знаний и практических навыков по контролю конкретными методами».
Основными методическими документами по НК, которые применяются при реализации требований [3] в части аттестации контролеров, являются:
– ПНАЭ Г-7-016-89 (визуальный и измерительный контроль); – ПНАЭ Г-7-017-89 (радиографический контроль);
– ПНАЭ Г-7-019-89 (контроль герметичности);
– ПНАЭ Г-7-014-89, часть I; ПНАЭ Г-7-030-89, часть II; ПНАЭ Г-7-031-89, часть III; ПНАЭ Г-7-032-89, часть IV (ультразвуковой контроль);
– ПНАЭ Г-7-018-89 (капиллярный контроль);
– ПНАЭ Г-7-015-89 (магнитопорошко-вый контроль).
В связи с необходимостью отражения в атомной энергетике современных тенденций по аттестации персонала и постепенного перехода в общероссийскую Систему НК с учетом специфики атомной отрасли ОАО НПО «ЦНИИТМАШ» разработал «Порядок аттестации контролеров, выполняющих контроль металла на действующих АЭС» [4]. Этот документ развивает основные положения [3]. В частности, аттестация персонала должна проводиться постоянно действующими аттестационными комиссиями (ПДАК) на предприятиях ОАО «Концерн Росэнергоатом» и/или в Аттестационных органах специализированных организаций, к которым относятся ГМО и другие организации (структурные подразделения), имеющие опыт работы в атомной энергетике не менее 5 лет и получившие от Ростехнадзора разрешение или подтверждение полномочий на право проведения аттестации персонала с перечислением методов контроля. Аттестационный орган должен быть признан эксплуатирующей организацией – ОАО «Концерн Росэнергоатом». Члены ПДАК должны проходить периодическую аттестацию в Аттестационном органе по разработанным этим органом программам.
Программы по теоретическим вопросам должны быть общими для всех ПДАК и Аттестационных органов, а экзаменационные вопросы ПДАК на предприятиях ОАО «Концерн Росэнергоатом» и в каждом Аттестационном органе могут быть разными.
Экзаменаторы Аттестационного органа, кроме требований, предъявляемых к контролерам высшего уровня квалификации, должны:
– иметь, как минимум, пятилетний стаж работы в области атомной энергетики;
– являться разработчиками (соавторами) методических, нормативных или технических документов, утвержденных и внедренных на предприятиях атомной энергетики;
– пройти проверку на знание Правил и норм в области использования атомной энергии и руководящих документов Ростехнадзора РФ с оформлением соответствующих удостоверений;
– руководствоваться порядком и требованиями к аттестации персонала [4].
Основной функцией Аттестационного органа и ПДАК предприятий ОАО «Концерн Росэнергоатом» является объективное определение уровня квалификации персонала, занятого в области контроля оборудования и трубопроводов атомных энергетических установок. Обязательным требованием к Аттестационному органу является отсутствие административной, финансовой, юридической и нормативной зависимости от юридических и физических лиц, заинтересованных в результатах аттестации.
Виды аттестации
Аттестация подразделяется на первичную, дополнительную, периодическую и внеочередную [3, 4].
Первичную аттестацию проходят кандидаты, не имевшие ранее удостоверения на право непосредственного выполнения соответствующего контроля и прошедшие теоретическую подготовку по специальной программе.
Дополнительную аттестацию проходят контролеры, прошедшие первичную аттестацию, перед допуском к выполнению работ, не указанных в их удостоверениях, при введении в действие новых методических документов по контролю, а также после перерыва в выполнении соответствующих работ по контролю свыше шести месяцев.
Периодическую аттестацию проходят все контролеры в целях продления срока действия их удостоверений. Периодическая аттестация по проверке теоретических знаний проводится не реже одного раза в три года, а проверка практических навыков – не реже одного раза в год.
Внеочередную аттестацию проходят контролеры перед допуском к выполнению контроля после временного отстранения от работы за нарушение технологии контроля.
Кандидаты на квалификационный уровень должны проходить первичную аттестацию в Аттестационных органах. Дополнительная, периодическая и внеочередная аттестации проводятся в ПДАК и/или в Аттестационных органах.
Уровни квалификации
Порядок аттестации контролеров оборудования и трубопроводов АЭС устанавливает три уровня квалификации при контроле:
– БПВЗ – проведение контроля без права выдачи заключения по результатам контроля;
– СПВЗ – проведение контроля с правом выдачи заключения по результатам контроля;
– СПА – проведение контроля с правом выдачи заключения по результатам контроля и правом аттестации контролеров в качестве члена ПДАК.
При проведении контроля с использованием автоматизированных систем контроля устанавливаются те же три уровня профессиональной квалификации – БПВЗ, СПВЗ, СПА. В этом случае кандидаты проходят дополнительную аттестацию с учетом специфики работы автоматизированных средств контроля и особенностей требований соответствующих методических документов.
Требования к общей и специальной подготовке персонала
Кандидат, претендующий на присвоение квалификационного уровня, должен иметь общее образование, теоретическую и практическую подготовку в соответствии с требованиями табл. 1.
Для допуска к экзаменам на соответствующий квалификационный уровень кандидат должен пройти предаттестаци-онную подготовку по определенному методу контроля в соответствии с программой Аттестационного органа. К аттестации допускаются кандидаты, не имеющие противопоказаний по состоянию здоровья и представившие соответствующее медицинское заключение (справку).
Аттестация в Аттестационном органе
Требования к Аттестационной комиссии
Состав Аттестационной комиссии в Аттестационном органе утверждается Приказом по предприятию.
Для приема экзаменов на уровни квалификации БПВЗ и СПВЗ в комиссии Аттестационного органа должно быть не менее двух контролеров с уровнем СПА. Для приема экзаменов у членов ПДАК предприятий ОАО «Концерн Росэнергоатом» на уровень СПА в Аттестационном органе должно быть не менее трех контролеров с уровнем СПА.
Требования к аттестации персонала
К первичной аттестации допускаются кандидаты, прошедшие теоретическую предаттестационную подготовку по программе, включающей вопросы физики данного метода контроля, технологию и специфику контроля объектов, подведомственных Федеральной службе по экологическому, технологическому и атомному надзору.
Первичная аттестация состоит из двух экзаменов – теоретического и практического. При первичной аттестации кандидата после теоретического экзамена проводится проверка практических навыков по данному методу контроля на экзаменационных образцах.
Уровень квалификации | Требования: | ||
к общему образованию | к специальной подготовке | к стажу по данному виду НК | |
1 | 2 | 3 | 4 |
БПВЗ | Среднее. Средне-техническое. Средне-специальное. Высшее | Подготовка на специальных курсах или по месту работы в подразделениях НК по программе, согласованной с Аттестационным органом | Нет |
СПВЗ | Один год | ||
СПА | Средне-техническое. Средне-специальное. Высшее | Знание учебных пособий, нормативно-методических документов, подготовка контролеров БПВЗ и СПВЗ, участие в конференциях и семинарах. | Иметь уровень квалификации СПВЗ и стаж работы не менее 5 лет |
Табл. 1. Общие требования к подготовке кандидатов на первичную аттестацию
Метод контроля |
Общее количество вопросов в сборнике, не менее |
Количество вопросов, задаваемых на экзамене на уровни квалификации |
||
БПВЗ | СПВЗ | СПА | ||
ТЕОРЕТИЧЕСКИЙ ЭКЗАМЕН | ||||
ЧАСТЬ 1 – ФИЗИЧЕСКИЕ ОСНОВЫ | ||||
Визуальный и измерительный (ВИК) | 60 | 30 | 30 | 40 |
Капиллярный (КК) | 60 | 30 | 30 | 30 |
Магнитопорошковый (МПК) | 80 | 40 | 40 | 40 |
Ультразвуковой (УЗК) | 80 | 40 | 40 | 40 |
Радиографический (РГК) | 80 | 40 | 40 | 40 |
Контроль герметичности (КГ) | 60 | 30 | 30 | 30 |
Вихретоковый (ВТК) | 80 | 40 | 40 | 40 |
Акустико-эмиссионный (АЭ) | 80 | 40 | 40 | 40 |
Телевизионный (ТВК) | 60 | 30 | 30 | 30 |
Телевизионный измерительный (ТИК) | 80 | 40 | 40 | 40 |
ЧАСТЬ 2 – НОРМАТИВНЫЕ И МЕТОДИЧЕСКИЕ ДОКУМЕНТЫ | ||||
Визуальный и измерительный (ВИК) | 60 | 20 | 20 | 20 |
Капиллярный (КК) | 60 | 20 | 20 | 20 |
Магнитопорошковый (МПК) | 60 | 20 | 20 | 20 |
Ультразвуковой (УЗК) | 60 | 20 | 20 | 20 |
Радиографический (РГК) | 60 | 20 | 20 | 20 |
Контроль герметичности (КГ) | 60 | 20 | 20 | 20 |
Вихретоковый (ВТК) | 60 | 20 | 20 | 20 |
Акустико-эмиссионный (АЭ) | 60 | 20 | 20 | 20 |
Телевизионный (ТВК) | 60 | 20 | 20 | 20 |
Телевизионный измерительный (ТИК) | 60 | 20 | 20 | 20 |
Табл. 2. Требования к минимальному количеству вопросов на экзаменах
Дополнительные требования к аттестации персонала, выполняющего автоматизированный контроль, и контроль с применением компьютерных средств обработки
Отличия этих требований от требований в случае контроля с применением ручных средств проявляются в части технологии контроля (специальные сканирующие устройства) и применения компьютерных средств обработки и сбора информации. К квалификации персонала, проводящего контроль с применением автоматизированных систем, предъявляются следующие требования:
Для получения права контроля по методикам автоматизированного контроля необходимо пройти аттестацию на предприятиях ОАО «Концерн Росэнергоатом» или у разработчика (поставщика) оборудования по работе с применением конкретных автоматизированных систем контроля с записью в квалификационном удостоверении.
Основные требования к проведению квалификационных экзаменов
Каждый кандидат при первичной аттестации сдает два экзамена по заявленному методу:
– теоретический экзамен, состоящий из двух частей: по физическим основам данного метода контроля (часть 1) и технологии и нормативно-технической документации НК (часть 2);
– практический экзамен, подтверждающий производственные навыки кандидата для контролера соответствующего уровня квалификации.
Требования к сборнику экзаменационных вопросов по теоретическому экзамену
Сборник экзаменационных вопросов должен быть разработан Аттестационным органом и утвержден его Руководством. Сборник должен содержать количество вопросов, указанное в табл. 2, и может быть представлен как в виде сброшюрованной книги, так и в компьютерной программе.
Требования к аппаратуре, стандартным, контрольным образцам и нормативной документации при проведении практического экзамена
Аппаратура для практического экзамена должна иметь паспорт, быть в рабочем состоянии и поверена, если это указано в паспорте на прибор.
Стандартные и контрольные образцы должны иметь паспорт.
Нормативная документация должна быть предоставлена в последнем издании (с изменениями).
Требования к комплекту экзаменационных образцов для практического экзамена
В комплект образцов для практического экзамена по НК должны входить образцы, соответствующие типам реальных объектов контроля (основной металл с заданным химическим составом или сварное соединение с соответствующей разделкой и технологией сварки), причем в них должны быть несплошности различного типа, возникающие как при производстве, так и в процессе эксплуатации. Комплект образцов для практического экзамена по НК должен содержать отдельные образцы без дефектов. Каждый экзаменационный образец должен иметь паспорт, содержащий сведения об образце и имеющихся в нем несплошностях, де-фектограмму, радиографический снимок и технологическую карту контроля и заключение в соответствии с категорией сварного соединения или основного металла, наплавки. Заключение на экзаменационный образец должно составляться по результатам контроля контролером с уровнем квалификации СПА.
Проведение теоретического экзамена
Теоретический экзамен сдается в письменной форме.
Для каждого уровня квалификации и метода НК должны быть разработаны Аттестационным органом сборники по теоретическим экзаменам, где каждый вопрос имеет многовариантные ответы.
Экзаменационные вопросы выбираются из сборника случайным образом.
Допускается сдача письменного теоретического экзамена на компьютере. После проведения экзамена проводится собеседование с аттестуемым.
В сборник вопросов по радиографическому методу должны входить вопросы по защите от излучения.
Теоретический экзамен при аттестации контролера уровня квалификации СПА включает вопросы на знание:
– технологии металлов и материаловедения, механизмов образования дефектов и их типов;
– методов контроля, на которые кандидат аттестуется в качестве члена аттестационной комиссии предприятия ОАО «Концерн Росэнергоатом».
Проведение практического экзамена
При проведении практического экзамена комиссия выдает кандидату протокол практического экзамена, который включает:
– для БПВЗ – технологическую карту контроля и бланк для фиксирования обнаруженных несплошностей;
– для СПВЗ и СПА – бланк, в котором кандидат должен разработать технологическую карту контроля.
Кандидат на СПВЗ и СПА проводит контроль не менее двух экзаменационных образцов: основного металла и сварного соединения с выдачей заключения по результатам контроля. Кандидат имеет право использовать на практическом экзамене необходимую нормативную документацию (ГОСТ, ОСТ, ПНАЭ Г, РД и т. п.). При аттестации по радиографическому методу кроме контроля образцов кандидат проводит расшифровку рентгеновских снимков: не менее пяти рентгенограмм и не менее трех на артефакты пленки.
Кандидат, претендующий на уровень квалификации СПА, должен сдать практический экзамен в объеме требований уровня квалификации СПВЗ. Кандидат может представить разработанный им документ (технологическую инструкцию, техническое решение, методический документ, экзаменационные билеты по какому-либо методу контроля, курс лекций по теоретическим вопросам или для дополнительной аттестации и т. п.).
Оценка результатов экзаменов и их оформление
Кандидат на уровни квалификации БПВЗ, СПВЗ и СПА считается выдержавшим экзамен, если он набрал в сумме по всему экзамену не менее 80 %, но не менее 70 % по каждой части экзамена.
Оценка ответов по теоретическому экзамену Nтеор, %, либо подсчитывается экзаменаторами, либо распечатывается в протоколах ответов при компьютерном варианте экзамена.
Итоговая оценка практического экзамена определяется путем сравнения полученных кандидатом результатов с паспортом на экзаменационный образец и подсчитывается в соответствии с методикой оценки практического экзамена, разработанной Аттестационным органом для данного метода контроля. В качестве примера представлена методика оценки практического экзамена по капиллярному контролю (табл. 3).
Содержание пунктов билета | Максимальная оценка, % | Оценка образца ¹ 1, % | Оценка образца ¹ 2, % |
1. Составление технологической карты контроля экзаменационного образца | всего 25, из них: | всего 25, из них: | всего 25, из них: |
1.1. Выбор способа контроля | 10 | 10 | 10 |
1.2. Выбор дефектоскопических материалов | 10 | 8 | 10 |
1.3. Выбор комплекта контрольных образцов для проверки чувствительности | 5 | 3 | 5 |
2. Определение чувствительности выбранного дефектоскопического набора | 10 | 6 | 10 |
3. Очистка контролируемой поверхности | 5 | 5 | 5 |
4. Проведение контроля | 15 | 13 | 15 |
5. Оформление дефектограммы | 10 | 9 | 10 |
6. Выявление не менее 80 % дефектов на экзаменационном образце от указанных на контрольной дефектограмме | 10 | 8 | 10 |
7. Оформление результатов контроля | 15 | 12 | 15 |
8. Окончательная очистка экзаменационного образца от дефектоскопических материалов | 5 | 5 | 5 |
9. Соблюдение Правил техники безопасности и охраны окружающей среды | 5 | 5 | 5 |
Итого: | 100 | N1 = 84 | N2 = 100 |
Итоговая оценка за практику: | N = (N + N )/пр 1 2 | 2 = (100 + 84)/ | 2 = 92 % |
Табл. 3. Методика оценки практического экзамена по капиллярному контролю
Итоговая оценка N экзаменов кандидата на уровни квалификации БПВЗ, СПВЗ и СПА рассчитывается по формуле:
N = 0,25N 1теор + 0,25N 2теор + 0,5N пр ;
где N 1теор - оценка по теоретическому экзамену (часть 1);
N 2теор - оценка по теоретическому экзамену (часть 2);
N - оценка по практическому экзамену.
Оформление квалификационного удостоверения в Аттестационном органе
Контролерам, прошедшим проверку теоретических знаний и практических навыков, должны выдаваться удостоверения за подписью председателя комиссии с печатью организации (предприятия), проводящей аттестацию.
Результаты проверки теоретических знаний и практических навыков контролеров указываются в Итоговом протоколе, при этом одновременно оформляется Протокол аттестационной комиссии с указанием решения о допуске к выполнению соответствующих работ.
Аттестация контролеров в ПДАК на предприятиях ОАО «Концерн Росэнергоатом»
В ПДАК предприятий ОАО «Концерн Росэнергоатом» может проходить периодическая, дополнительная и внеочередная аттестации контролеров (БПВЗ, СПВЗ).
ПДАК предприятия назначается приказом директора и включает штатных контролеров предприятия; она состоит из председателя, его заместителя и членов аттестационной комиссии. Члены ПДАК должны проходить периодическую аттестацию один раз в три года в Аттестационном органе.
Все виды аттестаций состоят из двух экзаменов – теоретического и практического. Для приема экзаменов в комиссии должно быть не менее двух контролеров по каждому методу контроля, аттестованных в качестве членов аттестационной комиссии, имеющих квалификационный уровень СПА. Программы должны быть разработаны Аттестационным органом или согласованы с ним, если они разработаны предприятием ОАО «Концерн Росэнергоатом».
После принятия положительного решения ПДАК по результатам экзаменов в квалификационное удостоверение аттестованного контролера, выданное Аттестационным органом, вносится результат аттестации, который подписывается председателем ПДАК и заверяется печатью предприятия ОАО «Концерн Росэнергоатом».
Ежегодная проверка практических навыков фиксируется в удостоверении с указанием номера протокола, даты и подписи председателя ПДАК. К удостоверению при любом виде аттестации прилагается Протокол аттестационной комиссии.
Для продления срока действия удостоверения контролеры проходят периодическую аттестацию по проверке теоретических знаний не реже одного раза в три года, а практических навыков – не реже одного раза в год.
Следует отметить, что в представленном документе [4] не полностью отражен ряд практически важных вопросов. В частности, отсутствуют требования к организационной структуре ПДАК и взаимодействию с надзорными органами, к оснащенности учебно-методическими материалами, обеспеченности паспортизированными экзаменационными образцами и т. д. Не приведены критерии оценки результатов практического экзамена на АЭС, особенно при использовании в качестве объекта контроля находящегося в эксплуатации участка оборудования или трубопровода.
Отсутствует механизм обеспечения объективности и достоверности результатов аттестации, в том числе из-за того, что на данном этапе нельзя признать деятельность ПДАК независимой от администрации АЭС.
Учитывая сказанное, можно рассматривать предложенный порядок аттестации контролеров на действующих АЭС как временный документ по разработке отраслевых правил аттестации персонала контроля в атомной энергетике.
В перспективе эти отраслевые правила аттестации должны базироваться на документе федерального уровня Ростехнадзора РФ СДАНК-02-2020 и отражать специфику отрасли в виде Приложения.
Литература
1. СДАНК-02-2020. Правила аттестации персонала в области неразрушающего контроля (утв. постановлением Госгортехнадзора России от 23.01.2002, ¹ 3; зарегистрировано в Минюсте РФ 17.04.2002, регистрационный ¹ 3378). – В кн.: Сб. документов. Сер. 28. Вып. 3. – М: ГУП «НТЦ «Промышленная безопасность», 2002.
2. Концепция управления Системой нераз-рушающего контроля и основные направления ее развития (утв. Госгортехнадзором России 28.08.1999 – В кн.: Сб. документов. Сер. 28. Вып. 1. – М: ГУП «НТЦ «Промышленная безопасность», 2000, с. 5–16.
3. ПНАЭ Г-7-010-89. Оборудование и трубопроводы атомных энергетических установок. Сварные соединения и наплавки. Правила контроля / Нормативный документ (действует с изменением ¹ 1 от 01.09.2000, постановление Госатомнадзора России от 27.12.1999 ¹ 7). – М.: НТЦ ЯРБ, 2000.
4. ПР 1.3.3.99.0010-2010. Порядок аттестации контролеров, выполняющих контроль металла на действующих АЭС. – М: ОАО «НПО ЦНИИТМАШ», 2010.